Preparing method for synthesizing and fusion casting of high-entropy alloy through self-propagating combustion
A self-propagating combustion, high-entropy alloy technology, applied in the field of self-propagating combustion synthesis casting high-entropy alloy preparation, can solve the problems of complex, high-entropy alloy preparation cost, difficult to form parts with complex shapes, etc. The effect of manufacturing cost and reducing manufacturing cost
- Summary
- Abstract
- Description
- Claims
- Application Information
AI Technical Summary
Problems solved by technology
Method used
Image
Examples
Embodiment 1
[0020] Embodiment 1: The preparation method of self-propagating combustion synthesis casting high-entropy alloy in this embodiment is as follows:
[0021] Step 1: Use aluminum powder, iron oxide, cobalt oxide, nickelous oxide, chromium oxide, and manganese oxide as raw materials, weigh the materials in a mass ratio of 1:0.65:0.65:0.7:0.7:0.7, and add 1% by mass of oxide Aluminum is used as a reactive diluent, and the mixed powder is ball milled, dried and ground, and then pressed through a die to obtain a prefabricated block with a relative density of 60%;
[0022] Step 2: Assemble the graphite crucible and the graphite mold, and pour the casting gypsum. After the gypsum mold is evacuated and degassed, it is placed in a muffle furnace according to the heating sequence of 150 °C for three hours, 350 °C for three hours, and 720 °C for one hour. mold, and then air-cooled until the mold temperature reached 200 °C to prepare for casting;
[0023] Step 3: place the prefabricated bl...
Embodiment 2
[0025] Embodiment 2: This embodiment is different from Embodiment 1. In step 1, the mass ratio of the six raw materials is 1:0.85:0.85:0.85:0.8:0.8, and the relative density of the prefabricated block is 70%. Others are the same as the first embodiment
Embodiment 3
[0026] Example three: . The mass ratio of the six raw materials in step 1, which is different from the first embodiment, is 1:0.75:0.75:0.77:0.75:0.75, and the relative density of the prefabricated block is 65%. Others are the same as the first embodiment.
PUM
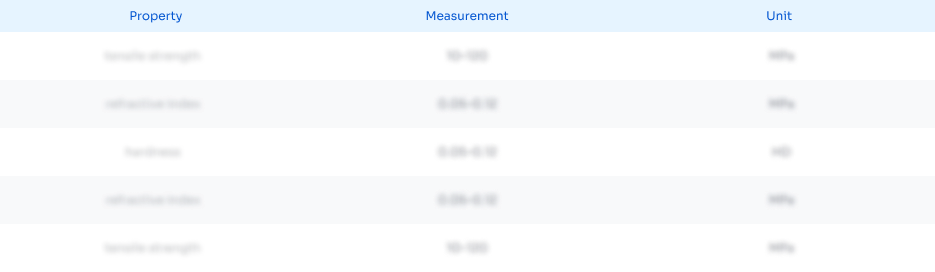
Abstract
Description
Claims
Application Information

- R&D
- Intellectual Property
- Life Sciences
- Materials
- Tech Scout
- Unparalleled Data Quality
- Higher Quality Content
- 60% Fewer Hallucinations
Browse by: Latest US Patents, China's latest patents, Technical Efficacy Thesaurus, Application Domain, Technology Topic, Popular Technical Reports.
© 2025 PatSnap. All rights reserved.Legal|Privacy policy|Modern Slavery Act Transparency Statement|Sitemap|About US| Contact US: help@patsnap.com