High-heat-resistant polypropylene composite material and preparation method thereof
A composite material, polypropylene technology, applied in the field of polypropylene polymer materials, can solve the problems of strict storage conditions and difficulty in purchasing powder materials, and achieves the effect of being extremely easy to realize and improving the dispersing ability.
- Summary
- Abstract
- Description
- Claims
- Application Information
AI Technical Summary
Problems solved by technology
Method used
Image
Examples
Embodiment 1
[0047] Accurately weigh homopolypropylene 66.4, talcum powder 30.0, polyethylene wax 0.05, polytetrafluoroethylene 3.0, antioxidant 1010 0.2, antioxidant DSTP 0.15, antioxidant 168 0.2 and place in a high-speed mixer by mass parts Mix for 5 minutes, then melt, extrude, and granulate through a twin-screw extruder.
[0048] The process parameters of the extruder are: zone 1 190-200°C, zone 2 200-210°C, zone 3 210-220°C, zone 4 205-215°C; the residence time of the entire extrusion process is 1-2 minutes, and the pressure is 12-18MPa.
Embodiment 2
[0050] Accurately weigh homopolypropylene 66.0, talcum powder 30.3, polyethylene wax 0.1, polytetrafluoroethylene 3.0, antioxidant 1010 0.2, antioxidant DSTP 0.2, antioxidant 168 0.2 and place in a high-speed mixer by mass parts Mix for 5 minutes, then melt, extrude, and granulate through a twin-screw extruder.
[0051] The process parameters of the extruder are: zone 1 190-200°C, zone 2 200-210°C, zone 3 210-220°C, zone 4 205-215°C; the residence time of the entire extrusion process is 1-2 minutes, and the pressure is 12-18MPa.
Embodiment 3
[0053] Accurately weigh homopolypropylene 64.9, talcum powder 30.5, polyethylene wax 1.0, polytetrafluoroethylene 3.0, antioxidant 1010 0.2, antioxidant DSTP 0.2, antioxidant 168 0.2 by mass parts and place in a high-speed mixer Mix for 5 minutes, then melt, extrude, and granulate through a twin-screw extruder.
[0054] The process parameters of the extruder are: zone 1 190-200°C, zone 2 200-210°C, zone 3 210-220°C, zone 4 205-215°C; the residence time of the entire extrusion process is 1-2 minutes, and the pressure is 12-18MPa.
PUM
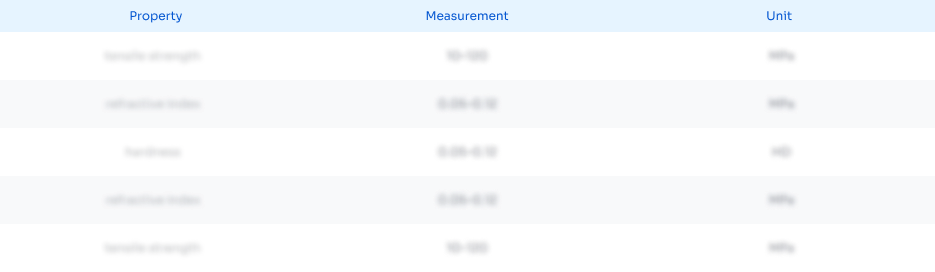
Abstract
Description
Claims
Application Information

- R&D
- Intellectual Property
- Life Sciences
- Materials
- Tech Scout
- Unparalleled Data Quality
- Higher Quality Content
- 60% Fewer Hallucinations
Browse by: Latest US Patents, China's latest patents, Technical Efficacy Thesaurus, Application Domain, Technology Topic, Popular Technical Reports.
© 2025 PatSnap. All rights reserved.Legal|Privacy policy|Modern Slavery Act Transparency Statement|Sitemap|About US| Contact US: help@patsnap.com