High-sulfur coal gangue efficient utilization machining process
A technology of high-sulfur coal gangue and processing technology, which is applied in the direction of solid separation, wet separation, chemical instruments and methods, etc., can solve the problems of low utilization rate of high-sulfur coal gangue and small value-added space, and reduce the cost of product sorting , The processing technology is simple, and the effect of improving the value-added utilization rate
- Summary
- Abstract
- Description
- Claims
- Application Information
AI Technical Summary
Problems solved by technology
Method used
Examples
Embodiment 1
[0022] The invention provides a process for efficient utilization of high-sulfur coal gangue, comprising the following steps:
[0023] Step 1, ore grinding: first crush the high-sulfur coal gangue with a pulverizer, and grind it with a ball mill to obtain coal gangue particles, and the particle size of the coal gangue particles is 140 mesh;
[0024] Step 2, mixing slurry: adding water to the gangue particles and preparing slurry in the adjustment tank, the mass concentration of the slurry is 18%, and stirring the slurry for 12 minutes;
[0025] Step 3, cyclone separation: the ore slurry is separated by a hydrocyclone, the cone angle of the hydrocyclone is 16°, the cone ratio is 0.50, the cyclone separation pressure is 0.16MPa, and the cyclone separation time 3 to 5 minutes;
[0026] Step 4, pulp preparation: the upper layer of wood obtained by separating the cyclone separator can be further sorted to obtain coal slime, and the lower layer of material is prepared in the adjust...
Embodiment 2
[0029] The invention provides a process for efficient utilization of high-sulfur coal gangue, comprising the following steps:
[0030] Step 1, ore grinding: first crush the high-sulfur coal gangue with a pulverizer, and grind it with a ball mill to obtain coal gangue particles, and the particle size of the coal gangue particles is 200 mesh;
[0031] Step 2, mixing slurry: adding water to the gangue particles and preparing slurry in the adjustment tank, the mass concentration of the slurry is 18%, and stirring the slurry for 12 minutes;
[0032] Step 3, cyclone separation: the ore slurry is separated by a hydrocyclone, the cone angle of the hydrocyclone is 16°, the cone ratio is 0.50, the cyclone separation pressure is 0.16MPa, and the cyclone separation time 3 to 5 minutes;
[0033] Step 4, pulp preparation: the upper layer of wood obtained by separating the cyclone separator can be further sorted to obtain coal slime, and the lower layer of material is prepared in the adjust...
Embodiment 3
[0036] The invention provides a process for efficient utilization of high-sulfur coal gangue, comprising the following steps:
[0037] Step 1, ore grinding: first crush the high-sulfur coal gangue with a pulverizer, and grind it with a ball mill to obtain coal gangue particles, the particle size of the coal gangue particles is 270 mesh;
[0038] Step 2, mixing slurry: adding water to the gangue particles and preparing slurry in the adjustment tank, the mass concentration of the slurry is 18%, and stirring the slurry for 12 minutes;
[0039] Step 3, cyclone separation: the ore slurry is separated by a hydrocyclone, the cone angle of the hydrocyclone is 16°, the cone ratio is 0.50, the cyclone separation pressure is 0.16MPa, and the cyclone separation time 3 to 5 minutes;
[0040] Step 4, pulp preparation: the upper layer of wood obtained by separating the cyclone separator can be further sorted to obtain coal slime, and the lower layer of material is prepared in the adjustment...
PUM
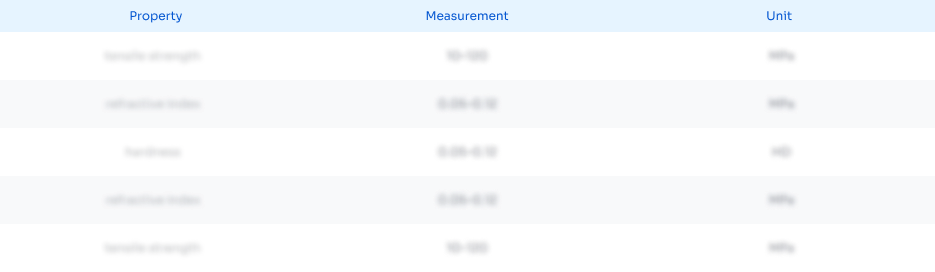
Abstract
Description
Claims
Application Information

- R&D Engineer
- R&D Manager
- IP Professional
- Industry Leading Data Capabilities
- Powerful AI technology
- Patent DNA Extraction
Browse by: Latest US Patents, China's latest patents, Technical Efficacy Thesaurus, Application Domain, Technology Topic, Popular Technical Reports.
© 2024 PatSnap. All rights reserved.Legal|Privacy policy|Modern Slavery Act Transparency Statement|Sitemap|About US| Contact US: help@patsnap.com