Micro-fluidic chip manufacturing method based on nanofiber template method
A microfluidic chip and nanofiber technology, applied in chemical instruments and methods, laboratory containers, laboratory utensils, etc., can solve the problems of high molding pressure, low machining surface accuracy, long heating time, etc. The effect of high molding precision
- Summary
- Abstract
- Description
- Claims
- Application Information
AI Technical Summary
Problems solved by technology
Method used
Image
Examples
Embodiment 1
[0023] The present invention proposes a method for manufacturing a microfluidic chip based on the nanofiber template method, including: firstly, placing the receiving plate 2 on the three-dimensional motion platform 3, following the motion platform 3 to perform three-dimensional motion, and placing the motion platform 3 and the receiving plate 2 on the device. In the container with the liquid light-curable material 4, make the liquid light-curable material 4 submerge the receiving plate 2 for a certain distance, turn on the surface light sources 6 distributed on both sides of the spinning nozzle 1, and solidify the liquid light-curable material above the receiving plate 2 , forming a microfluidic chip substrate. The soluble polymer solution / melt is passed through the spinning nozzle 1 for near-field electrospinning or microflow spinning, and the fibers are ordered on the receiving plate 2 by controlling the relationship between the falling speed of the fibers and the moving spe...
Embodiment 2
[0026] Apply a layer of acrylic resin on the receiving plate 2 as the light-curing material 4, and place it on the moving platform 3 as the spinning receiving plate 2, follow the moving platform 3 for three-dimensional movement, and place the moving platform 3 and the receiving plate 2 on the In the container containing the acrylic resin, make the liquid photocurable material 4 acrylic resin submerge the receiving plate 2 for a certain distance, turn on the surface light sources 6 distributed on both sides of the spinning nozzle 1, and solidify the liquid photocurable material above the receiving plate 2 , to form a microfluidic chip substrate; add PEG pellets to the polymer melt spinning nozzle 1, heat the temperature to 60°C to melt and plasticize it, and adjust the distance between the spinning nozzle 1 and the receiving plate 2 to 5mm , the spinning voltage is 1kV, and the near-field melt electrospinning is started; the moving speed of the moving platform 3 is adjusted to 3...
PUM
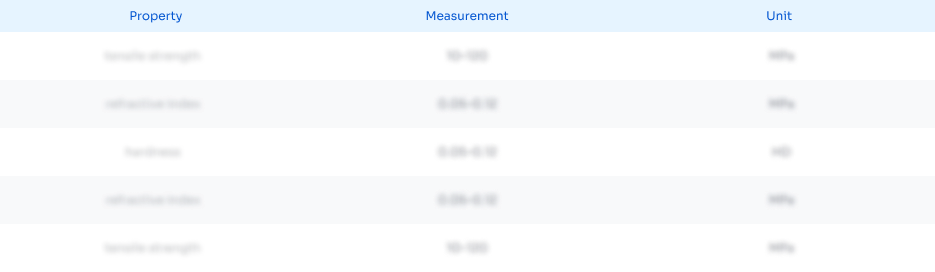
Abstract
Description
Claims
Application Information

- R&D
- Intellectual Property
- Life Sciences
- Materials
- Tech Scout
- Unparalleled Data Quality
- Higher Quality Content
- 60% Fewer Hallucinations
Browse by: Latest US Patents, China's latest patents, Technical Efficacy Thesaurus, Application Domain, Technology Topic, Popular Technical Reports.
© 2025 PatSnap. All rights reserved.Legal|Privacy policy|Modern Slavery Act Transparency Statement|Sitemap|About US| Contact US: help@patsnap.com