Alloy for precise machining clamp and preparation method for alloy
A technology for precision machining and alloying, applied in the field of alloys for precision machining fixtures and their preparation, to achieve the effects of high fracture toughness and corrosion resistance, long service life and high hardness
- Summary
- Abstract
- Description
- Claims
- Application Information
AI Technical Summary
Problems solved by technology
Method used
Examples
Embodiment 1
[0019] In the embodiment of the present invention, an alloy for precision machining fixtures is composed of the following raw materials according to mass percentage: beryllium powder 1.5%, zirconium powder 1.9%, calcium 5.3%, molybdenum powder 3.0%, vanadium powder 0.8%, tin powder 0.3% %, copper powder 7.2%, and the balance is aluminum powder. Weigh beryllium powder, zirconium powder, calcium, molybdenum powder, vanadium powder, tin powder, copper powder and aluminum powder according to mass percentage, mix them evenly, and make quick-setting sheets with an average thickness of 0.1-0.3 mm after melting. The quick-setting sheet is subjected to hydrogen crushing, dehydrogenated and crushed to obtain alloy coarse powder. The alloy coarse powder is cold-pressed to 300MPa, and then placed in a sintering furnace for calcination. First, the temperature is raised to 580°C, and kept at this temperature for 1 hour, then the temperature is raised to 650°C, and vacuum is drawn at this te...
Embodiment 2
[0021] In the embodiment of the present invention, an alloy for precision machining fixtures is composed of the following raw materials according to mass percentage: beryllium powder 2.3%, zirconium powder 2.7%, calcium 6.1%, molybdenum powder 3.8%, vanadium powder 1.5%, tin powder 0.7% %, copper powder 8%, and the balance is aluminum powder. Weigh beryllium powder, zirconium powder, calcium, molybdenum powder, vanadium powder, tin powder, copper powder and aluminum powder according to mass percentage, mix them evenly, and make quick-setting sheets with an average thickness of 0.1-0.3 mm after melting. The quick-setting sheet is subjected to hydrogen crushing, dehydrogenated and crushed to obtain alloy coarse powder. The alloy coarse powder is cold-pressed to 320MPa, and then placed in a sintering furnace for calcination. First, the temperature is raised to 600°C, and kept at this temperature for 1.2h, and then the temperature is raised to 650°C, and pumped at this temperature...
Embodiment 3
[0023] In the embodiment of the present invention, an alloy for precision machining fixtures is composed of the following raw materials according to mass percentage: beryllium powder 1.8%, zirconium powder 2.1%, calcium 5.5%, molybdenum powder 3.2%, vanadium powder 1%, tin powder 0.4% %, copper powder 7.4%, and the balance is aluminum powder. Weigh beryllium powder, zirconium powder, calcium, molybdenum powder, vanadium powder, tin powder, copper powder and aluminum powder according to mass percentage, mix them evenly, and make quick-setting sheets with an average thickness of 0.1-0.3 mm after melting. The quick-setting sheet is subjected to hydrogen crushing, dehydrogenated and crushed to obtain alloy coarse powder. The alloy coarse powder is cold-pressed to 310MPa, and then placed in a sintering furnace for calcination. First, the temperature is raised to 590°C, and kept at this temperature for 1.1h, and then the temperature is raised to 650°C, and pumped at this temperature...
PUM
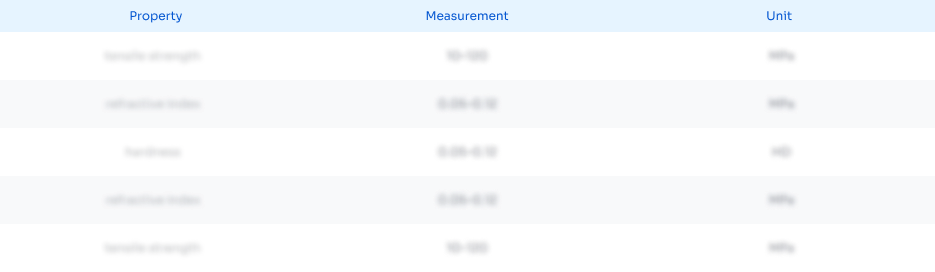
Abstract
Description
Claims
Application Information

- Generate Ideas
- Intellectual Property
- Life Sciences
- Materials
- Tech Scout
- Unparalleled Data Quality
- Higher Quality Content
- 60% Fewer Hallucinations
Browse by: Latest US Patents, China's latest patents, Technical Efficacy Thesaurus, Application Domain, Technology Topic, Popular Technical Reports.
© 2025 PatSnap. All rights reserved.Legal|Privacy policy|Modern Slavery Act Transparency Statement|Sitemap|About US| Contact US: help@patsnap.com