Method for preparing ungraphitised carbon and polypyrrole collaboratively coated sulfur
A technology of non-graphitized carbon and polypyrrole, which is applied in the direction of structural parts, electrical components, battery electrodes, etc., to achieve the effects of simple and easy experimental operation, increased electrical conductivity, and reduced experimental cost and process complexity
- Summary
- Abstract
- Description
- Claims
- Application Information
AI Technical Summary
Problems solved by technology
Method used
Image
Examples
Embodiment 1
[0023] (1) Prepare tubular polypyrrole by template method: add 1.01 g of ferric chloride hexahydrate to 50 ml of methyl orange solution, stir at room temperature for 5 minutes; then add 0.1 g of distilled pyrrole monomer dropwise, React for 6 hours at room temperature to obtain tubular polypyrrole;
[0024] (2) Placing the tubular polypyrrole obtained in step (1) in a tube furnace protected by argon at 700 degrees Celsius for heat treatment for 2 hours to obtain non-graphitized carbon;
[0025] (3) Add 0.1 g of the non-graphitized carbon obtained in step (2) to 100 ml of deionized water for ultrasonic for 10 minutes. After the dispersion is uniform, add 5.12 g of sodium thiosulfate pentahydrate and add dropwise with a pipette Concentrated hydrochloric acid 3ml, stirred at room temperature for 6 hours; then put the reacted mixture in an ice-water bath, continue to stir the reaction, add 1.31 g of sodium p-toluenesulfonate, and add 0.1 g of pyrrole monomer to the mixture ; Then diss...
Embodiment 2
[0028] (1) Prepare tubular polypyrrole by template method: add 2.03 g of ferric chloride hexahydrate to 150 ml of methyl orange solution, stir at room temperature for 15 minutes; then add 0.5 g of rectified pyrrole monomer dropwise, React for 24 hours at room temperature to obtain tubular polypyrrole;
[0029] (2) Place the tubular polypyrrole obtained in step (1) in a tube furnace protected by argon for heat treatment at 900 degrees Celsius for 5 hours to obtain non-graphitized carbon;
[0030] (3) Add 0.3 g of the non-graphitized carbon obtained in step (2) to 450 ml of deionized water for ultrasonic for 30 minutes. After the dispersion is uniform, add 9.93 g of sodium thiosulfate pentahydrate and add dropwise with a pipette Concentrated hydrochloric acid 8ml, stirred at room temperature for 24 hours; then put the reacted mixture in an ice-water bath, continue to stir the reaction, add 2.62 g of sodium p-toluenesulfonate, and add 0.3 g of pyrrole monomer to the mixture; Then dis...
Embodiment 3
[0034] (1) Prepare tubular polypyrrole by template method: add 1.21 g of ferric chloride hexahydrate to 75 ml of methyl orange solution and stir for 8 minutes at room temperature; then add 0.3 g of distilled pyrrole monomer dropwise, React for 12 hours at room temperature to obtain tubular polypyrrole;
[0035] (2) Placing the tubular polypyrrole obtained in step (1) in a tube furnace protected by argon at 750 degrees Celsius for heat treatment for 3 hours to obtain non-graphitized carbon;
[0036] (3) Add 0.15 g of the non-graphitized carbon obtained in step (2) to 200 ml of deionized water for 20 minutes, and after the dispersion is uniform, add 6.30 g of sodium thiosulfate pentahydrate, and add dropwise with a pipette Concentrated hydrochloric acid 4ml, stirred at room temperature for 8 hours; then put the reacted mixture in an ice-water bath, continue to stir the reaction, add 3.30 g of sodium p-toluenesulfonate, add 0.18 g of pyrrole monomer to the mixture; Then, 1.50 g of fe...
PUM
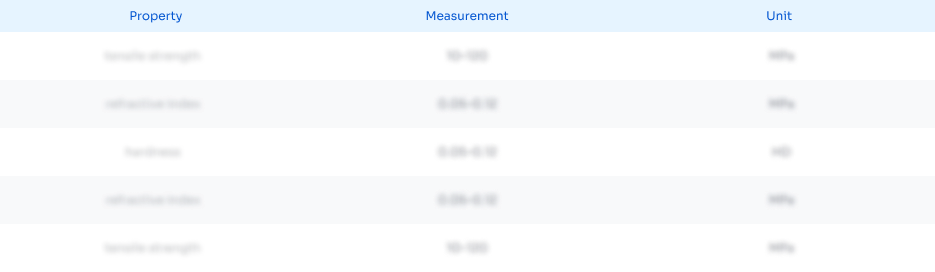
Abstract
Description
Claims
Application Information

- R&D
- Intellectual Property
- Life Sciences
- Materials
- Tech Scout
- Unparalleled Data Quality
- Higher Quality Content
- 60% Fewer Hallucinations
Browse by: Latest US Patents, China's latest patents, Technical Efficacy Thesaurus, Application Domain, Technology Topic, Popular Technical Reports.
© 2025 PatSnap. All rights reserved.Legal|Privacy policy|Modern Slavery Act Transparency Statement|Sitemap|About US| Contact US: help@patsnap.com