Preparation method for gradient change silicon-nitrogen-carbon ceramic fibers
A technology of silicon nitrogen carbon ceramics and gradient change, which is applied to the chemical characteristics of fibers, textiles and papermaking, etc. It can solve problems such as difficult to meet the use requirements, and achieve the effects of novel fiber structure, controllability, and simple operation process
- Summary
- Abstract
- Description
- Claims
- Application Information
AI Technical Summary
Problems solved by technology
Method used
Image
Examples
Embodiment 1
[0024] 1) Non-melting treatment: use polymer solid polycarbosilane as a precursor for melt spinning, and then irradiate the precursor with electron beams for crosslinking;
[0025] 2) Nitriding treatment: Put the cross-linked wire obtained in step 1) into a tube furnace, pump and exchange air three times, and pass NH 3 , 1°C / min heating up to 450°C;
[0026] 3) High temperature pyrolysis: Step 2) NH 3 Change to N 2 , the temperature was raised to 1000°C at a heating rate of 2°C / min, kept at a temperature of 120min, and the temperature was lowered to room temperature by program, that is, the gradient silicon nitride / silicon carbide fiber was prepared.
Embodiment 2
[0028] 1) Non-melting treatment: Polymer solid polycarbosilane is used as a precursor for melt spinning, and then the precursor is crosslinked with hot air;
[0029] 2) Nitriding treatment: Put the cross-linked wire obtained in step 1) into a tube furnace, pump and exchange air three times, and pass NH 3 , 3°C / min heating up to 550°C;
[0030] 3) High temperature pyrolysis: Step 2) NH 3 Change to N 2 , the temperature was raised to 1200°C at a heating rate of 5°C / min, kept at a temperature of 60 minutes, and the temperature was lowered to room temperature by program, that is, the gradient silicon nitride / silicon carbide fiber was prepared.
Embodiment 3
[0032] 1) Non-melting treatment: using ultra-high molecular weight solid polycarbosilane as a precursor, melt-spinning to obtain precursors, and then high-temperature thermochemical self-crosslinking to obtain crosslinked fibers;
[0033] 2) Nitriding treatment: Put the cross-linked wire obtained in step 1) into a tube furnace, pump and exchange air three times, and pass NH 3 , 5°C / min to heat up to 650°C;
[0034] 3) High temperature pyrolysis: Step 2) NH 3 Change to N 2 , the temperature was raised to 1400°C at a heating rate of 8°C / min, kept at a temperature of 30min, and then the temperature was lowered to room temperature by program, that is, the gradient silicon nitride / silicon carbide fiber was prepared.
PUM
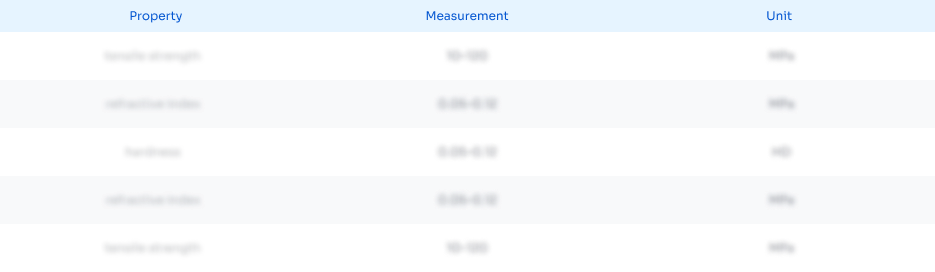
Abstract
Description
Claims
Application Information

- R&D
- Intellectual Property
- Life Sciences
- Materials
- Tech Scout
- Unparalleled Data Quality
- Higher Quality Content
- 60% Fewer Hallucinations
Browse by: Latest US Patents, China's latest patents, Technical Efficacy Thesaurus, Application Domain, Technology Topic, Popular Technical Reports.
© 2025 PatSnap. All rights reserved.Legal|Privacy policy|Modern Slavery Act Transparency Statement|Sitemap|About US| Contact US: help@patsnap.com