Method for recovering copper from copper smelting slag
A technology of copper smelting slag and copper recovery, which is applied to the improvement of process efficiency, flotation, solid separation, etc. It can solve the problems of difficult control of the production process, small crystal size of copper minerals, poor adaptability of copper smelting slag, etc., and achieve improvement Floatability, flotation index fluctuation is small, and the effect of improving flotation recovery rate
- Summary
- Abstract
- Description
- Claims
- Application Information
AI Technical Summary
Problems solved by technology
Method used
Image
Examples
preparation example Construction
[0030] The composite additive used in the present invention adopts the following preparation method: weighing and mixing pyrite, chalcopyrite, coke powder and sodium humate according to the mass ratio, adding an appropriate amount of water, and then pelletizing on a disc 3-5mm pellets are prepared in the machine, and finally the pellets are dried until the moisture content is less than 2% to obtain the compound additive.
[0031] In the following examples, crushing and grinding are to coarsely crush the modified slag to -5 mm, then crush it to -1 mm by a high-pressure roller mill, and then grind it in a ball mill.
Embodiment 1
[0035] For copper smelting electric furnace depleted molten slag, the copper grade is 0.60%, and 3% of the copper smelting slag quality is added with compound additives (pyrite 45%, chalcopyrite 5%, coke powder 40%, sodium humate 10% ) Modification of molten slag, fully mixed and melted under the action of ultrasonic field, modified slag is slowly cooled (under the action of centrifugal force and magnetic field, rotating speed 10r / min, magnetic field intensity 0.2T), crushing and grinding Afterwards, flotation obtains copper concentrate. Modification is carried out under the conditions of melting temperature of 1250℃, cooling rate of 1.5℃ / min, and cooling end temperature of 900℃. The modified slag is subjected to copper flotation conditions: grinding fineness -0.045mm 90%; butyl xanthate 80g / t After three times of selection and three times of sweeping, the grade of crude copper concentrate is 20.56% and the copper recovery rate is 74.45%.
Embodiment 2
[0037] For copper smelting electric furnace depleted molten slag, the copper grade is 0.60%, and compound additives are added according to 4% of the copper smelting slag quality (pyrite 40%, chalcopyrite 10%, coke powder 45%, sodium humate 5%) The slag is modified, mixed and melted under the action of ultrasonic field, and the modified slag is slowly cooled (under the action of centrifugal force and magnetic field, the speed is 15r / min, the magnetic field intensity is 0.25T), after crushing and grinding , Flotation obtains copper concentrate. Modification is carried out under the conditions of melting temperature of 1300℃, cooling rate of 1.5℃ / min, and cooling end temperature of 900℃. The modified slag is subjected to copper flotation conditions: grinding fineness -0.045mm 90%; butyl xanthate 80g / t After three times of selection and three times of sweeping, the grade of crude copper concentrate is 21.34%, and the copper recovery rate is 76.57%.
PUM
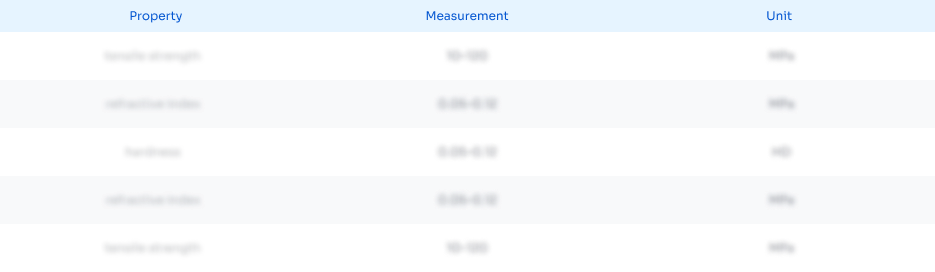
Abstract
Description
Claims
Application Information

- Generate Ideas
- Intellectual Property
- Life Sciences
- Materials
- Tech Scout
- Unparalleled Data Quality
- Higher Quality Content
- 60% Fewer Hallucinations
Browse by: Latest US Patents, China's latest patents, Technical Efficacy Thesaurus, Application Domain, Technology Topic, Popular Technical Reports.
© 2025 PatSnap. All rights reserved.Legal|Privacy policy|Modern Slavery Act Transparency Statement|Sitemap|About US| Contact US: help@patsnap.com