Double-layer high-temperature-resistant heat insulation and wave absorption composite material preparation method
A composite material, high temperature resistant technology, applied in chemical instruments and methods, other chemical processes, etc., can solve the problems of poor adhesion of wave absorbing coatings, high absorption efficiency, narrow absorption frequency band, etc., and achieve good environmental and temperature adaptability. , Good physical and mechanical properties, the effect of absorbing frequency bandwidth
- Summary
- Abstract
- Description
- Claims
- Application Information
AI Technical Summary
Problems solved by technology
Method used
Examples
example 1
[0018] Weigh 40g of aluminum trichloride, 1g of zirconium carbonate, 0.5g of yttrium acetate and 0.1g of lanthanum acetate into 150mL of deionized water, adjust the pH to 4 with 10% acetic acid solution by mass fraction, heat to 60°C after adjustment, and keep stirring After mixing for 20 minutes, add 1 g of triethyl phosphate, continue to stir for 20 minutes, and then distill under reduced pressure at 30 kPa for 30 minutes after stirring. Dry at ℃ for 8 hours, put the dried filamentous fibers into a tube furnace, raise the temperature to 700℃ under the protection of nitrogen atmosphere, heat treat for 2 hours, pulverize after heat treatment, and pass through 80 mesh sieve to obtain ceramic fiber powder; weigh 3g respectively Add nano-silica, 0.3g 3-glycidyl etheroxypropyl triethoxysilane and 0.3g dodecyl alcohol ester to 150g deionized water, stir and mix, add 10g of the above ceramic fiber powder, and ultrasonically disperse for 10min after adding , after dispersing, heat to...
example 2
[0021]Weigh 45g of aluminum trichloride, 2g of zirconium carbonate, 0.6g of yttrium acetate and 0.2g of lanthanum acetate into 175mL of deionized water, adjust the pH to 4.5 with 10% acetic acid solution by mass fraction, heat to 70°C after adjustment, and keep stirring After mixing for 25 minutes, add 2.5 g of triethyl phosphate, continue to stir for 25 minutes, and then distill under reduced pressure at 40 kPa for 40 minutes after stirring. After distillation, the concentrated solution is obtained, and the concentrated solution is spun, and the filamentous fibers are collected and placed in an oven. Dry at 110°C for 9 hours, put the dried filamentous fibers into a tube furnace, raise the temperature to 800°C under the protection of nitrogen atmosphere, heat treatment for 2.5 hours, pulverize after heat treatment, and pass through a 90-mesh sieve to obtain ceramic fiber powder; Take 4g of nano-silica, 0.4g of 3-glycidyl etheroxypropyl triethoxysilane and 0.4g of dodecyl alcoho...
example 3
[0024] Weigh 50g of aluminum trichloride, 3g of zirconium carbonate, 0.7g of yttrium acetate and 0.3g of lanthanum acetate into 200mL of deionized water, adjust the pH to 5 with 10% acetic acid solution by mass fraction, heat to 80°C after adjustment, and keep stirring After mixing for 30 minutes, add 4 g of triethyl phosphate, continue to stir for 30 minutes, and then distill under reduced pressure at 50 kPa for 50 minutes after stirring. After distillation, the concentrated solution is obtained, and the concentrated solution is spun, and the filamentous fibers are collected and placed in an oven. Dry at ℃ for 10 hours, put the dried filamentous fibers into a tube furnace, raise the temperature to 900℃ under the protection of nitrogen atmosphere, heat treat for 3 hours, pulverize after heat treatment, and pass through a 100-mesh sieve to obtain ceramic fiber powder; weigh 5g respectively Add nano-silica, 0.5g 3-glycidyl etheroxypropyl triethoxysilane and 0.5g dodecyl alcohol e...
PUM
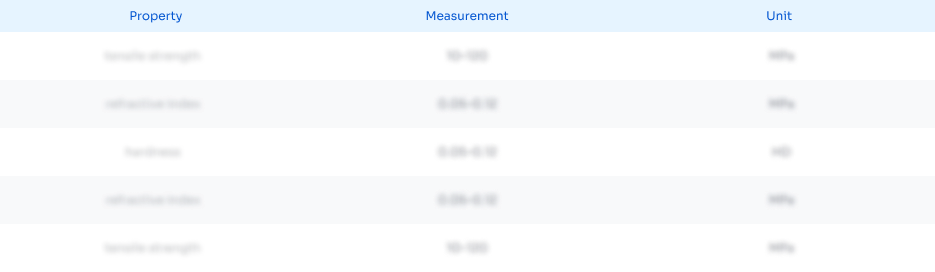
Abstract
Description
Claims
Application Information

- R&D
- Intellectual Property
- Life Sciences
- Materials
- Tech Scout
- Unparalleled Data Quality
- Higher Quality Content
- 60% Fewer Hallucinations
Browse by: Latest US Patents, China's latest patents, Technical Efficacy Thesaurus, Application Domain, Technology Topic, Popular Technical Reports.
© 2025 PatSnap. All rights reserved.Legal|Privacy policy|Modern Slavery Act Transparency Statement|Sitemap|About US| Contact US: help@patsnap.com