Converter chromium-preparation method for low-carbon Cr-containing alloy steel
An alloy steel and converter technology, which is applied in the manufacture of converters and other directions, can solve the problems of long duration of alloy addition, unmatched production rhythm, and large addition of ferrochromium, avoiding heat loss, increasing Cr content, and increasing the addition amount. Effect
- Summary
- Abstract
- Description
- Claims
- Application Information
AI Technical Summary
Problems solved by technology
Method used
Examples
Embodiment 1
[0016] The deep dephosphorized molten iron is smelted by oxygen blowing in the converter to decarburize and heat up. When the temperature of the molten steel in the molten pool is 1740°C and the carbon content is 0.028%, the oxygen blowing is stopped, and the ferrochrome alloy with a preheating temperature of 400°C is added. Among them, the high Carbon ferrochrome 10.2t, micro carbon ferrochrome 6.4t. After the ferrochrome alloy is added, no oxygen is blown in the converter, no ferrosilicon or aluminum powder is added, and the bottom blowing is increased. The final tapping temperature is 1620°C, the carbon content of the molten steel is 0.40%, and 100kg of aluminum is added to the ladle to deoxidize the molten steel during the tapping process, and the Cr content of the molten steel is 5.26%.
Embodiment 2
[0018] The deep dephosphorized molten iron is smelted by oxygen blowing in the converter to decarburize and heat up. When the temperature of the molten steel in the molten pool is 1710°C and the carbon content is 0.046%, the oxygen blowing is stopped, and the ferrochrome alloy with a preheating temperature of 400°C is added. Among them, the high Carbon ferrochrome 6.5t, micro carbon ferrochrome 8.9t. After the ferrochrome alloy is added, no oxygen is blown in the converter, no ferrosilicon or aluminum powder is added, and the bottom blowing is increased. The final tapping temperature is 1590°C, the carbon content of the molten steel is 0.25%, and 120kg of aluminum is added to the ladle during the tapping process to deoxidize the molten steel, and the Cr content of the molten steel is 5.02%.
PUM
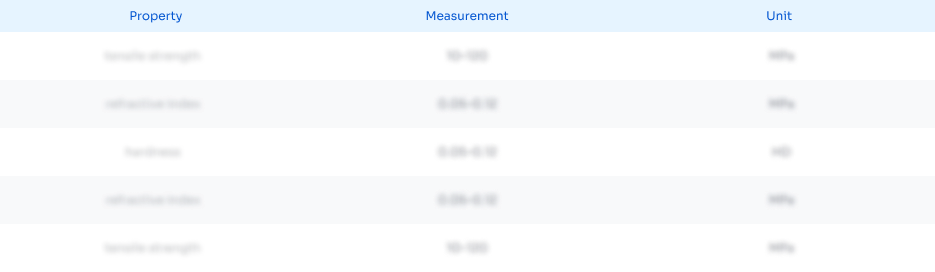
Abstract
Description
Claims
Application Information

- Generate Ideas
- Intellectual Property
- Life Sciences
- Materials
- Tech Scout
- Unparalleled Data Quality
- Higher Quality Content
- 60% Fewer Hallucinations
Browse by: Latest US Patents, China's latest patents, Technical Efficacy Thesaurus, Application Domain, Technology Topic, Popular Technical Reports.
© 2025 PatSnap. All rights reserved.Legal|Privacy policy|Modern Slavery Act Transparency Statement|Sitemap|About US| Contact US: help@patsnap.com