Electrode processing method applied to direct synthesis of hydrogen peroxide through oxygen electroreduction
A treatment method, hydrogen peroxide technology, applied in the direction of electrodes, electrolysis process, electrolysis components, etc., can solve the problems of low catalytic activity of electrodes, rough and porous, etc., and achieve the effect of improving electrode activity without affecting stability and increasing specific surface area
- Summary
- Abstract
- Description
- Claims
- Application Information
AI Technical Summary
Problems solved by technology
Method used
Image
Examples
Embodiment 1
[0028] An electrode treatment method applied to the direct synthesis of hydrogen peroxide by oxygen electroreduction, comprising the following process steps:
[0029] 1) The purchased graphite felt material was cut into a size of 1.0cm×2.0cm, washed with 5mL of acetone, ethanol, and deionized water, and dried for later use; figure 1 It is the electron micrograph of the purchased commercial graphite felt electrode material.
[0030] 2) Put the graphite felt into a sealed tube furnace, raise the temperature to 1000°C at a rate of 10°C / min under a nitrogen atmosphere with an air flow rate of 150mL / min, and simultaneously add ferrocene (5wt%)-glacial acetic acid The vaporized steam of the solution is injected into the tube furnace for 1 hour and then stopped;
[0031] 3) Under the protection of an inert gas, cool down to room temperature at a certain rate (10°C / min), take out the graphite felt, soak it in 0.5mol / L dilute hydrochloric acid solution for 2h, rinse it with deionized ...
Embodiment 2
[0035] 1) The purchased graphite felt material was cut into a size of 1.0cm×2.0cm, washed with 5mL of acetone, ethanol, and deionized water, and dried for later use;
[0036] 2) Put the graphite felt into a sealed tube furnace, raise the temperature to 900°C at a rate of 5°C / min under a nitrogen atmosphere with an air flow rate of 200mL / min, and simultaneously ferrocene (5wt.%)-ice The vaporized steam of the acetic acid solution is injected into the tube furnace and stopped after keeping for 1 hour;
[0037] 3) Under the protection of nitrogen, cool down to room temperature at a certain rate (5°C / min), take out the graphite felt, soak it in 0.5mol / L dilute hydrochloric acid solution for 2h, rinse it with deionized water, and dry it at 70°C for 12h;
[0038] The graphite felt material treated by the invention is used as an electrode for directly synthesizing hydrogen peroxide by oxygen electroreduction.
[0039] The graphite felt material that this embodiment 2 obtains is nega...
Embodiment 3
[0041] 1) The purchased graphite felt material was cut into a size of 1.0cm×2.0cm, washed with 5mL of acetone, ethanol, and deionized water, and dried for later use;
[0042] 2) Put the graphite felt into a sealed tube furnace, raise the temperature to 800°C at a rate of 7°C / min under a nitrogen atmosphere with an air flow rate of 180mL / min, and simultaneously ferrocene (5wt.%)-ice The vaporized steam of the acetic acid solution is injected into the tube furnace and stopped after keeping for 1 hour;
[0043] 3) Under the protection of nitrogen, cool down to room temperature at a certain rate (7°C / min), take out the graphite felt, soak it in 0.5mol / L dilute hydrochloric acid solution for 2h, rinse it with deionized water, and dry it at 80°C for 12h;
[0044] The graphite felt material treated by the invention is used as an electrode for directly synthesizing hydrogen peroxide by oxygen electroreduction.
[0045] The graphite felt material obtained in Example 2 is used as the c...
PUM
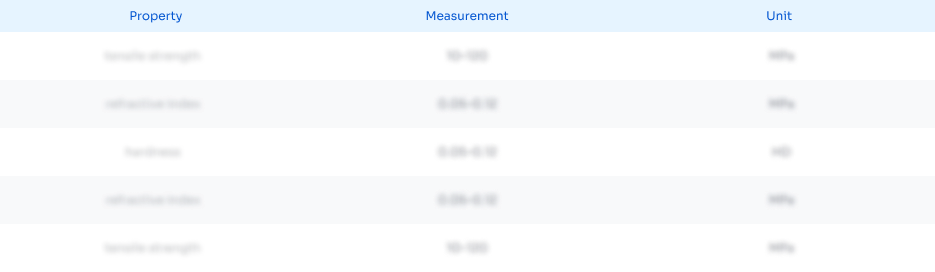
Abstract
Description
Claims
Application Information

- R&D
- Intellectual Property
- Life Sciences
- Materials
- Tech Scout
- Unparalleled Data Quality
- Higher Quality Content
- 60% Fewer Hallucinations
Browse by: Latest US Patents, China's latest patents, Technical Efficacy Thesaurus, Application Domain, Technology Topic, Popular Technical Reports.
© 2025 PatSnap. All rights reserved.Legal|Privacy policy|Modern Slavery Act Transparency Statement|Sitemap|About US| Contact US: help@patsnap.com