Method for improving component uniformity of W elements in GH4720Li alloy
A technology of element composition and uniformity, which is applied in the field of improving the uniformity of W element composition of GH4720Li alloy, can solve problems such as uneven distribution of W elements, and achieve the effects of solving performance uniformity, uniform distribution of W elements, and solving composition differences
- Summary
- Abstract
- Description
- Claims
- Application Information
AI Technical Summary
Problems solved by technology
Method used
Image
Examples
Embodiment 1
[0041] Melting GH4720Li superalloy ingots with a diameter of Φ510mm.
[0042] 1. Raw material processing:
[0043] Electrolytic Ni and electrolytic cobalt are subjected to surface sandblasting, and after treatment, they are dried with nickel-tungsten alloy, nickel-molybdenum alloy, pure titanium, pure aluminum, and pure chromium at 100°C for 10 hours.
[0044] 2. Ingredients:
[0045] Determine the alloy ratio, and feed according to the ratio. The alloy ratio and the raw materials and amounts used are shown in Tables 2 and 3.
[0046] Table 2 Alloy chemical composition ratio, wt%
[0047]
[0048] Table 3 raw materials and dosage
[0049]
[0050] 3. Vacuum induction melting:
[0051] The ingot mold of Φ350mm is used for vacuum induction melting, the melting speed is 700kg / h, the refining temperature is 1480℃, and the refining time is 60min; the pouring temperature is 1480℃. Grinding is done after smelting.
[0052] 4. Vacuum consumable melting:
[0053] The electro...
Embodiment 2
[0058] Melting GH4720Li superalloy ingots with a diameter of Φ440mm.
[0059] 1. Raw material processing:
[0060] Electrolytic Ni and electrolytic cobalt are subjected to surface sandblasting, and after treatment, they are dried with nickel-tungsten alloy, nickel-molybdenum alloy, pure titanium, pure aluminum, and pure chromium at 100°C for 10 hours.
[0061] 2. Ingredients:
[0062] Determine the alloy ratio, and feed according to the ratio. The alloy ratio, raw materials and amounts used are shown in Tables 5 and 6.
[0063] Table 5 Alloy chemical composition ratio, wt%
[0064]
[0065] Table 6 raw materials and dosage
[0066]
[0067] 3. Vacuum induction melting:
[0068] Vacuum induction melting uses Φ280mm ingot mold, melting speed is 300kg / h, refining temperature is 1450℃, refining time is 30min; pouring temperature is 1450℃. Grinding is done after smelting.
[0069] 4. Vacuum consumable melting:
[0070] The electrode is turned around for welding and sme...
Embodiment 3
[0075] Melting GH4720Li superalloy ingots with a diameter of Φ560mm.
[0076] 1. Raw material processing:
[0077] Electrolytic Ni and electrolytic cobalt are subjected to surface sandblasting, and after treatment, they are dried with nickel-tungsten alloy, nickel-molybdenum alloy, pure titanium, pure aluminum, and pure chromium at 100°C for 10 hours.
[0078] 2. Ingredients:
[0079] Determine the alloy ratio, and feed according to the ratio. The alloy ratio, raw materials and consumption are shown in Tables 8 and 9.
[0080] Table 8 Alloy chemical composition ratio, wt%
[0081]
[0082] Table 9 Materials and dosage
[0083]
[0084] 3. Vacuum induction melting:
[0085] Vacuum induction melting uses a Φ400mm ingot mold, the melting speed is 700kg / h, the refining temperature is 1550°C, and the refining time is 90min; the pouring temperature is 1550°C. Grinding is done after smelting.
[0086] 4. Vacuum consumable melting:
[0087] The electrode is turned around ...
PUM
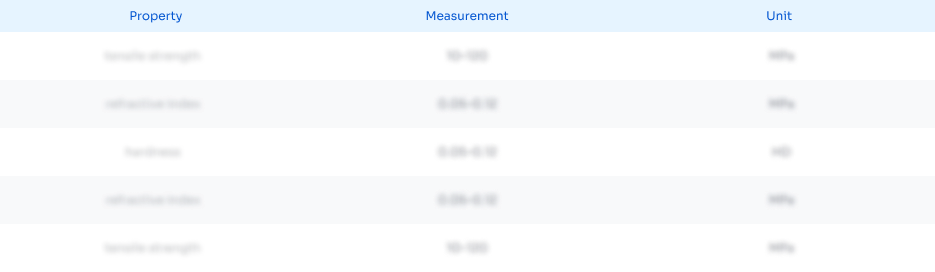
Abstract
Description
Claims
Application Information

- R&D Engineer
- R&D Manager
- IP Professional
- Industry Leading Data Capabilities
- Powerful AI technology
- Patent DNA Extraction
Browse by: Latest US Patents, China's latest patents, Technical Efficacy Thesaurus, Application Domain, Technology Topic, Popular Technical Reports.
© 2024 PatSnap. All rights reserved.Legal|Privacy policy|Modern Slavery Act Transparency Statement|Sitemap|About US| Contact US: help@patsnap.com