Novel high-performance composite material for cable and preparation method
A high-performance, new material technology, applied in circuits, electrical components, plastic/resin/wax insulators, etc., to achieve the effects of easy degradation, low environmental pollution, and high strength
- Summary
- Abstract
- Description
- Claims
- Application Information
AI Technical Summary
Problems solved by technology
Method used
Examples
Embodiment 1
[0016] A new high-performance composite material for cables, which is made of the following raw materials in parts by weight: 50 parts of polyvinyl chloride resin, 30 parts of acrylonitrile-butadiene-styrene resin, 8 parts of polycarbonate, trimene 5 parts of trioctyl ester, 4 parts of decabromodiphenyl ether, 5 parts of epoxidized soybean oil, 10 parts of anilinomethyltriethoxysilane, 5 parts of bacterial cellulose, 3 parts of nano calcium carbonate, 4 parts of mercaptoethanol, 1 part of pineapple hemp fiber, 5 parts of coke powder, 5 parts of compound additives;
[0017] The composite auxiliary agent is prepared by the following method: by weight, 10 parts of chitosan, 8 parts of mica powder, 20 parts of kaolin, 5 parts of activated carbon, 1 part of magnesium hydroxide, 0.5 parts of cocoyl diethanolamine, acrylic acid 1.2 parts of hydroxyethyl ester; dissolving chitosan in 4% acetic acid aqueous solution with a volume concentration 3 times its weight, then adding mica powde...
Embodiment 2
[0025] A new high-performance composite material for cables, made of the following raw materials in parts by weight: 55 parts of polyvinyl chloride resin, 25 parts of acrylonitrile-butadiene-styrene resin, 10 parts of polycarbonate, trimene 6 parts of trioctyl ester, 5 parts of decabromodiphenyl ether, 6 parts of epoxidized soybean oil, 11 parts of anilinomethyltriethoxysilane, 8 parts of bacterial cellulose, 4 parts of nano calcium carbonate, 5 parts of mercaptoethanol, 2 parts of pineapple hemp fiber, 6 parts of coke powder, 8 parts of compound additives;
[0026] The composite auxiliary agent is prepared by the following method: by weight, 11 parts of chitosan, 10 parts of mica powder, 15 parts of kaolin, 6 parts of activated carbon, 2 parts of magnesium hydroxide, 1.0 parts of cocoamide diethanolamine, acrylic acid 1.3 parts of hydroxyethyl ester; dissolving chitosan in 4% acetic acid aqueous solution with a volume concentration 3 times of its weight, then adding mica powd...
Embodiment 3
[0034] A new high-performance composite material for cables, made of the following raw materials in parts by weight: 60 parts of polyvinyl chloride resin, 20 parts of acrylonitrile-butadiene-styrene resin, 12 parts of polycarbonate, trimellitate 7 parts of trioctyl ester, 6 parts of decabromodiphenyl ether, 7 parts of epoxidized soybean oil, 12 parts of anilinomethyltriethoxysilane, 10 parts of bacterial cellulose, 5 parts of nano calcium carbonate, 6 parts of mercaptoethanol, 3 parts of pineapple hemp fiber, 7 parts of coke powder, 10 parts of compound additives;
[0035] The composite auxiliary agent is prepared by the following method: by weight, 12 parts of chitosan, 15 parts of mica powder, 10 parts of kaolin, 7 parts of activated carbon, 3 parts of magnesium hydroxide, 1.5 parts of cocoamide diethanolamine, acrylic acid 1.5 parts of hydroxyethyl ester; dissolving chitosan in 4% acetic acid aqueous solution with a volume concentration 3 times its weight, then adding mica ...
PUM
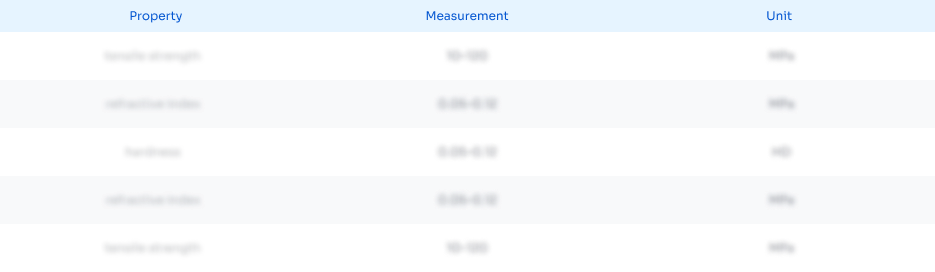
Abstract
Description
Claims
Application Information

- Generate Ideas
- Intellectual Property
- Life Sciences
- Materials
- Tech Scout
- Unparalleled Data Quality
- Higher Quality Content
- 60% Fewer Hallucinations
Browse by: Latest US Patents, China's latest patents, Technical Efficacy Thesaurus, Application Domain, Technology Topic, Popular Technical Reports.
© 2025 PatSnap. All rights reserved.Legal|Privacy policy|Modern Slavery Act Transparency Statement|Sitemap|About US| Contact US: help@patsnap.com