Method for preparing glass ceramics
A technology of glass micro-glass and glass-ceramic, applied in the field of glass micro-crystal preparation, can solve the problems that have not yet been seen, and achieve the effects of novel principle, stable performance and reliable process
- Summary
- Abstract
- Description
- Claims
- Application Information
AI Technical Summary
Problems solved by technology
Method used
Examples
Embodiment 1
[0015] Select the barium oxide-titanium oxide-silicon oxide (BTS) glass system, according to the ordinary glass preparation process, mix the ingredients of chemically pure grade raw materials evenly, put them into the melting crucible, and place the crucible in the high temperature zone of the high temperature furnace. Melt at 1400-1500°C for 2-18 hours, stirring intermittently during the melting process. Pour the melted molten glass into a cast iron or graphite mold, and pour it into a cylindrical sample with a diameter of 60mm and a height of 40mm. The sample is annealed at 500-600°C for 1-4 hours. The annealed and cooled cylindrical glass sample is cut into a disc-shaped sample with a thickness of 6mm, and the two ends are properly ground and polished. Then put the treated sample on the high-gradient temperature directional crystallization furnace, and place positive and negative high-temperature electrode plates on both surfaces of the wafer. The relative positive and nega...
Embodiment 2
[0017] Select barium oxide-titanium oxide-silicon oxide (BTS) basic glass system, use chemically pure grade raw material ingredients, weigh the basic glass raw material powder to form glass ceramics in proportion, add 1% by weight of ZrO2 as the network external body addition , and then put the batch material into the alumina ceramic ball mill for wet mixing and grinding for 6-18 hours. After drying, put the mixed abrasive into the alumina ceramic crucible. The length, width and height of the inner wall of the alumina ceramic crucible are 60mm, 80mm and 6mm respectively, and can be designed according to the shape requirements. Place the alumina crucible with batch materials in the high temperature zone of the silicon-molybdenum rod electric furnace, and then place high-temperature electrode plates on the upper and lower parallel surfaces of the melting crucible, and the relative positive and negative plate areas completely cover the glass to be melted and polarized For the sam...
PUM
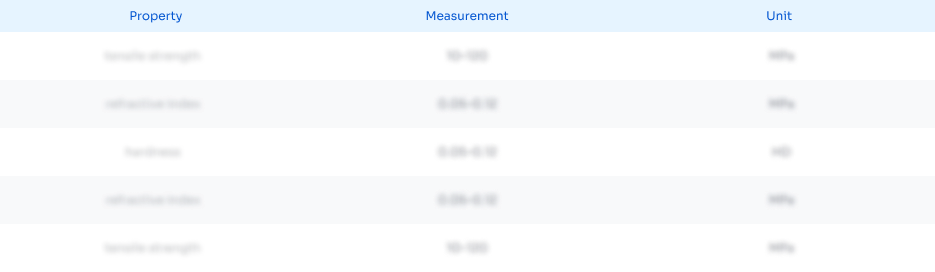
Abstract
Description
Claims
Application Information

- R&D Engineer
- R&D Manager
- IP Professional
- Industry Leading Data Capabilities
- Powerful AI technology
- Patent DNA Extraction
Browse by: Latest US Patents, China's latest patents, Technical Efficacy Thesaurus, Application Domain, Technology Topic, Popular Technical Reports.
© 2024 PatSnap. All rights reserved.Legal|Privacy policy|Modern Slavery Act Transparency Statement|Sitemap|About US| Contact US: help@patsnap.com