Preparation method of 1,1-difluoroethylene
A technology of ethylene difluoride and chloroethane, which is applied in the direction of dehydrohalogenation preparation, chemical instruments and methods, metal/metal oxide/metal hydroxide catalysts, etc., can solve the problem of poor stability and service life of catalysts and inability of catalytic cracking Industrialization and other issues, to achieve the effect of low cost, significant social and economic benefits, and fewer steps
- Summary
- Abstract
- Description
- Claims
- Application Information
AI Technical Summary
Problems solved by technology
Method used
Examples
Embodiment 1
[0027] Barium hydroxide is placed in a roasting furnace at 800 ° C for 4 hours to obtain a barium oxide catalyst,
[0028] The obtained barium oxide catalyst is then used to catalyze the removal of HCl from 1,1-difluoro-1-chloroethane to prepare 1,1-difluoroethylene. The reaction is carried out in a plug-flow tubular reactor. The reaction tube of the tubular reactor is a Ni tube with an inner diameter of 20mm and a length of 800mm, and is placed in a heating furnace to heat up and the temperature is raised to 400°C for reaction. The reaction pressure At normal pressure, before the reaction, N 2 (with an airspeed of 1000 h -1 ), the temperature of the catalyst bed was raised from room temperature to 200°C at a rate of 5°C / min and dried for 2 h, then raised to 400°C at a rate of 5°C / min and then cooled to 200°C after catalyst treatment for 2 h. HCFC-142b continued to process for another 2 hours. After heating up to 400°C, pass HCFC-142b and N 2 The mixed gas undergoes a gas-...
Embodiment 2-6
[0030] Barium hydroxide is placed in a roasting furnace at 800 ° C for 4 h to obtain a barium oxide catalyst, and 5 wt % of CoF 3 、NiF 2 、CuF 2 、LaF 3 , CeF 3 Mix with barium oxide in solid phase to obtain a bimetallic catalyst.
[0031]Then the bimetallic catalyst obtained for 5 was used to catalyze the dehydrochlorination of 1,1-difluoro-1-chloroethane to prepare 1,1-difluoroethylene. The reaction is carried out in a plug-flow tube reactor. The reaction tube of the tube reactor is a Ni tube with an inner diameter of 20mm and a length of 800mm, and is placed in a heating furnace to heat up to 400°C for reaction. The reaction pressure is normal pressure. Before the reaction, pass N 2 (with an airspeed of 4000 h -1 ), the temperature of the catalyst bed was raised from room temperature to 200 °C at a rate of 5 °C / min and dried for 2 h. Then, the temperature was raised to 400°C at a rate of 5°C / min and the catalyst was treated for 2 hours, then the temperature was lowere...
Embodiment 7
[0036] The barium hydroxide was placed in a roasting furnace at 800°C for 4 hours to obtain a barium oxide catalyst. Barium oxide was treated with 20 mL / min of HCl gas for 5 h to obtain a barium chloride catalyst.
[0037] The obtained barium chloride catalyst is then used to catalyze the removal of HCl from 1,1-difluoro-1-chloroethane to prepare 1,1-difluoroethylene. The reaction is carried out in a plug-flow tube reactor. The reaction tube of the tube reactor is a Ni tube with an inner diameter of 20mm and a length of 800mm, and is placed in a heating furnace to heat up to 400°C for reaction. The reaction pressure is normal pressure. Before the reaction, pass N 2 (with an airspeed of 1000 h -1 ), the temperature of the catalyst bed was raised from room temperature to 200 °C at a rate of 5 °C / min and dried for 2 h. Then, the temperature was raised to 400°C at a rate of 5°C / min and the catalyst was treated for 2 hours, then the temperature was lowered to 200°C, and HCFC-14...
PUM
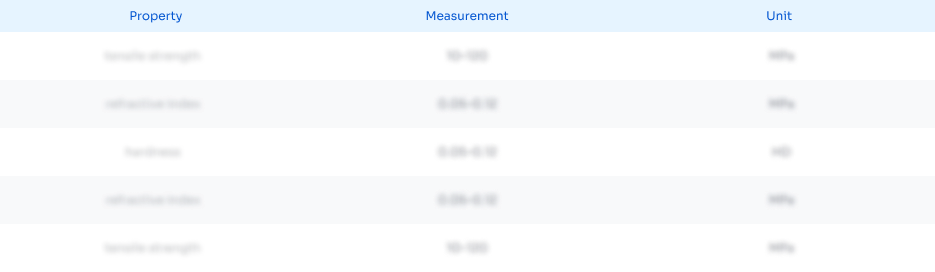
Abstract
Description
Claims
Application Information

- R&D
- Intellectual Property
- Life Sciences
- Materials
- Tech Scout
- Unparalleled Data Quality
- Higher Quality Content
- 60% Fewer Hallucinations
Browse by: Latest US Patents, China's latest patents, Technical Efficacy Thesaurus, Application Domain, Technology Topic, Popular Technical Reports.
© 2025 PatSnap. All rights reserved.Legal|Privacy policy|Modern Slavery Act Transparency Statement|Sitemap|About US| Contact US: help@patsnap.com