Thermal treatment process for high-hardenability alloy bushing
A high hardenability and alloy technology, applied in heat treatment furnaces, heat treatment equipment, manufacturing tools, etc., can solve the problems of high energy consumption, long production cycle of high hardenability alloy bushings, and easy aging of the medium, and achieve production quality. Stabilize, improve product quality and production efficiency, and avoid the effect of deformation
- Summary
- Abstract
- Description
- Claims
- Application Information
AI Technical Summary
Problems solved by technology
Method used
Examples
Embodiment 1
[0014] Example 1 A heat treatment process for a high-hardenability alloy bushing. The alloy bushing is composed of the following chemical components by mass percentage: 0.22% carbon, 0.45% manganese, 0.67% silicon, 1.6% chromium, 0.2% molybdenum, nickel 0.25%, titanium 0.08%, niobium 0.6%, vanadium 0.12%, phosphorus ≤ 0.004%, sulfur ≤ 0.003%, and the rest is iron.
[0015] A heat treatment process for a high-hardenability alloy bushing, comprising the following steps:
[0016] (1) The alloy bushing is heated at a temperature of 960° C., kept for 24 hours, cooled to room temperature in an intermediate frequency furnace, and preformed and forged;
[0017] (2) Correct and trim the above-mentioned forged alloy bushings, stack the products after trimming, put them in a quenching furnace with a temperature of 920-960 ° C for 30 minutes, and take out the water to cool to room temperature;
[0018] (3) Put the alloy bushing in a tempering furnace for high-temperature tempering. The h...
Embodiment 2
[0021] Example 2 A heat treatment process for a high-hardenability alloy bushing, the alloy bushing is composed of the following chemical components by mass percentage: 0.35% carbon, 0.76% manganese, 0.83% silicon, 2.5% chromium, 0.24% molybdenum, nickel 0.36%, titanium 0.22%, niobium 0.85%, vanadium 0.20%, phosphorus ≤ 0.004%, sulfur ≤ 0.003%, and the rest is iron.
[0022] A heat treatment process for a high-hardenability alloy bushing, comprising the following steps:
[0023] (1) The alloy bushing is heated at a temperature of 960° C., kept for 24 hours, cooled to room temperature in an intermediate frequency furnace, and preformed and forged;
[0024] (2) Correct and trim the above-mentioned forged alloy bushings, stack the products after trimming, put them in a quenching furnace with a temperature of 920-960 ° C for 30 minutes, and take out the water to cool to room temperature;
[0025] (3) Put the alloy bushing in a tempering furnace for high-temperature tempering. The...
Embodiment 3
[0028] Example 3 A heat treatment process for a high-hardenability alloy bushing. The alloy bushing is composed of the following chemical components by mass percentage: 0.28% carbon, 0.58% manganese, 0.72% silicon, 1.8% chromium, 0.22% molybdenum, nickel 0.32%, titanium 0.17%, niobium 0.65%, vanadium 0.18%, phosphorus ≤ 0.004%, sulfur ≤ 0.003%, and the rest is iron.
[0029] A heat treatment process for a high-hardenability alloy bushing, comprising the following steps:
[0030] (1) The alloy bushing is heated at a temperature of 960° C., kept for 24 hours, cooled to room temperature in an intermediate frequency furnace, and preformed and forged;
[0031] (2) Correct and trim the above-mentioned forged alloy bushings, stack the products after trimming, put them in a quenching furnace with a temperature of 920-960 ° C for 30 minutes, and take out the water to cool to room temperature;
[0032] (3) Put the alloy bushing in a tempering furnace for high-temperature tempering. The...
PUM
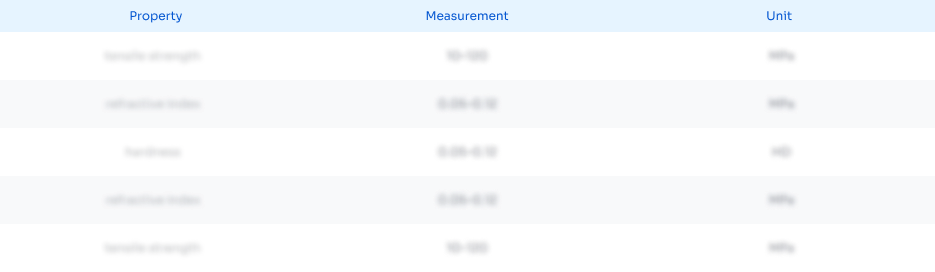
Abstract
Description
Claims
Application Information

- Generate Ideas
- Intellectual Property
- Life Sciences
- Materials
- Tech Scout
- Unparalleled Data Quality
- Higher Quality Content
- 60% Fewer Hallucinations
Browse by: Latest US Patents, China's latest patents, Technical Efficacy Thesaurus, Application Domain, Technology Topic, Popular Technical Reports.
© 2025 PatSnap. All rights reserved.Legal|Privacy policy|Modern Slavery Act Transparency Statement|Sitemap|About US| Contact US: help@patsnap.com