Adhesive for dye-sublimation transfer printing, and synthesis process thereof
A synthesis process and adhesive technology, applied in the direction of adhesives, adhesive additives, epoxy resin glue, etc., can solve the problems of scratch resistance, adhesion, water resistance and high temperature resistance, etc., and achieve environmental protection in the preparation process No pollution, high adhesion, good physical properties
- Summary
- Abstract
- Description
- Claims
- Application Information
AI Technical Summary
Problems solved by technology
Method used
Image
Examples
Embodiment 1
[0018] In this embodiment, the adhesive components include 40 parts by weight of bisphenol A epoxy resin, 10 parts of polyurethane resin, 3 parts of toughening agent, 3 parts of sodium acrylate, 3 parts of glycerin, ethylene-acetic acid 5 parts of ethylene copolymer, 5 parts of oil-absorbing filler, 3 parts of organic bentonite, 4 parts of kaolin, 2 parts of antioxidant, 5 parts of ethylene glycol and 1 part of nano silicon oxide.
[0019] The synthesis technique of the present embodiment comprises the following steps:
[0020] A. Mix bisphenol A epoxy resin, polyurethane resin, toughening agent, sodium acrylate, glycerol, and ethylene-vinyl acetate copolymer and add them to the stirring tank for stirring. The stirring tank speed is 3000 rpm, and the stirring time For 20min, stand still to obtain mixture A;
[0021] B. Add oil-absorbing filler, organic bentonite, kaolin, antioxidant, ethylene glycol, and nano-silicon oxide to the mixture A. After mixing, add it to the reactio...
Embodiment 2
[0024] In this embodiment, the adhesive components include 60 parts by weight of bisphenol A epoxy resin, 20 parts of polyurethane resin, 8 parts of toughening agent, 8 parts of sodium acrylate, 10 parts of glycerol, ethylene-acetic acid 12 parts of ethylene copolymer, 12 parts of oil-absorbing filler, 8 parts of organic bentonite, 10 parts of kaolin, 8 parts of antioxidant, 15 parts of ethylene glycol and 4 parts of nano silicon oxide;
[0025] The synthesis technique of the present embodiment comprises the following steps:
[0026] A. Mix bisphenol A epoxy resin, polyurethane resin, toughening agent, sodium acrylate, glycerol, and ethylene-vinyl acetate copolymer and add them to the stirring tank for stirring. The stirring tank speed is 5000 rpm, and the stirring time For 40min, stand still to obtain mixture A;
[0027] B. Add oil-absorbing filler, organic bentonite, kaolin, antioxidant, ethylene glycol and nano-silicon oxide to the mixture A, mix and add to the reaction ke...
Embodiment 3
[0030] In this embodiment, the adhesive components include 45 parts by weight of bisphenol A epoxy resin, 12 parts of polyurethane resin, 4 parts of toughening agent, 4 parts of sodium acrylate, 4 parts of glycerin, ethylene-acetic acid 6 parts of ethylene copolymer, 6 parts of oil-absorbing filler, 4 parts of organic bentonite, 5 parts of kaolin, 3 parts of antioxidant, 6 parts of ethylene glycol and 2 parts of nano silicon oxide.
[0031] The synthesis technique of the present embodiment comprises the following steps:
[0032] A. Mix bisphenol A epoxy resin, polyurethane resin, toughening agent, sodium acrylate, glycerol, and ethylene-vinyl acetate copolymer and add them to the stirring tank for stirring. The rotating speed of the stirring tank is 3500 rpm, and the stirring time For 25min, stand still to obtain mixture A;
[0033] B. Add oil-absorbing filler, organic bentonite, kaolin, antioxidant, ethylene glycol and nano-silicon oxide to the mixture A. After mixing, add i...
PUM
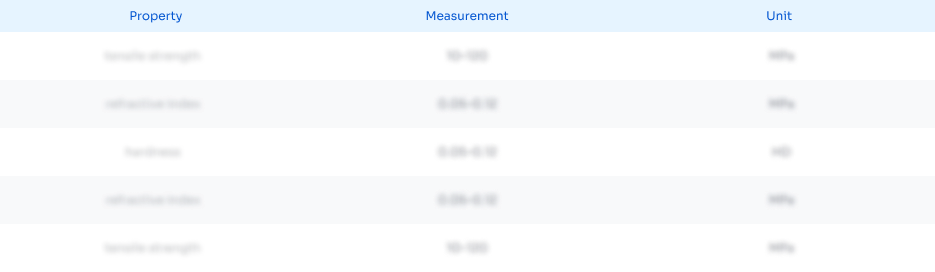
Abstract
Description
Claims
Application Information

- R&D
- Intellectual Property
- Life Sciences
- Materials
- Tech Scout
- Unparalleled Data Quality
- Higher Quality Content
- 60% Fewer Hallucinations
Browse by: Latest US Patents, China's latest patents, Technical Efficacy Thesaurus, Application Domain, Technology Topic, Popular Technical Reports.
© 2025 PatSnap. All rights reserved.Legal|Privacy policy|Modern Slavery Act Transparency Statement|Sitemap|About US| Contact US: help@patsnap.com