Compound powder for modified polypropylene and preparation method thereof
A technology of composite powder and polypropylene, which is applied in the field of filling materials, can solve problems such as singleness, and achieve the effects of improving dispersion, reducing production costs, and increasing bonding
- Summary
- Abstract
- Description
- Claims
- Application Information
AI Technical Summary
Problems solved by technology
Method used
Image
Examples
Embodiment 1
[0032] A composite powder for modified polypropylene, characterized in that it contains the following components in parts by weight: 1 part of calcium carbonate surface-treated with stearic acid, 2-5 parts of wollastonite treated with a silane coupling agent, titanium 2-5 parts of talcum powder treated with ester coupling agent.
[0033] The preparation process of the calcium carbonate of described stearic acid surface treatment is that stearic acid is added in 2500 order calcium carbonates, and the addition amount of stearic acid is 1.5% of calcium carbonate quality, mixes under the rotating speed of 500-2000 rev / min Modification, modification temperature 110°C, modification time 40min.
[0034] The preparation process of the wollastonite treated with the silane coupling agent is to add the silane coupling agent to 1250 mesh wollastonite, the aspect ratio of the wollastonite is 1:(15~20), and the silane coupling agent is added The amount is 1.5% of wollastonite mass, mixed a...
Embodiment 2
[0045] A composite powder for modified polypropylene, characterized in that it contains the following components in parts by weight: 1 part of calcium carbonate surface-treated with stearic acid, 2-5 parts of wollastonite treated with silane coupling agent, titanium 2-5 parts of talcum powder treated with ester coupling agent.
[0046] The preparation process of the calcium carbonate of described stearic acid surface treatment is that stearic acid is added in 2000 mesh calcium carbonate, and the amount of stearic acid added is 1% of calcium carbonate quality, mixes under the rotating speed of 500-2000 rev / min Modification, modification temperature 105°C, modification time 45min.
[0047] The preparation process of the wollastonite treated with the silane coupling agent is to add the silane coupling agent to the 1000 mesh wollastonite, the aspect ratio of the wollastonite is 1:(15~20), and the silane coupling agent is added The amount is 1% of the mass of wollastonite, mixed a...
Embodiment 3
[0058] A composite powder for modified polypropylene, characterized in that it contains the following components in parts by weight: 1 part of calcium carbonate surface-treated with stearic acid, 2-5 parts of wollastonite treated with a silane coupling agent, titanium 2-5 parts of talcum powder treated with ester coupling agent.
[0059] The preparation process of the calcium carbonate of described stearic acid surface treatment is that stearic acid is added in 3000 order calcium carbonates, and the addition amount of stearic acid is 2% of calcium carbonate quality, mixes under the rotating speed of 500-2000 rev / min Modification, modification temperature 120°C, modification time 30min.
[0060] The preparation process of the wollastonite treated with the silane coupling agent is to add the silane coupling agent to 1500 mesh wollastonite, the aspect ratio of the wollastonite is 1:(15~20), and the silane coupling agent is added The amount is 2% of the wollastonite mass, mixed a...
PUM
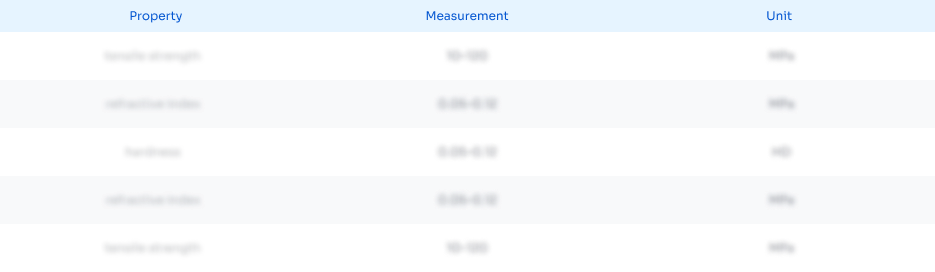
Abstract
Description
Claims
Application Information

- R&D Engineer
- R&D Manager
- IP Professional
- Industry Leading Data Capabilities
- Powerful AI technology
- Patent DNA Extraction
Browse by: Latest US Patents, China's latest patents, Technical Efficacy Thesaurus, Application Domain, Technology Topic, Popular Technical Reports.
© 2024 PatSnap. All rights reserved.Legal|Privacy policy|Modern Slavery Act Transparency Statement|Sitemap|About US| Contact US: help@patsnap.com