Alkylphosphinate derivative fire retardant containing phosphaphenanthrene group and preparation method thereof
A technology of alkyl phosphinate and derivatives, applied in the field of alkyl phosphinate derivative flame retardants and their preparation, can solve problems such as unreported
- Summary
- Abstract
- Description
- Claims
- Application Information
AI Technical Summary
Problems solved by technology
Method used
Image
Examples
Embodiment 1
[0035] Add 84.11g (0.20mol) of o-diallyl bisphenol A diglycidyl ether and 86.47g (0.40mol) of DOPO into the reaction vessel, raise the temperature of the reaction system to 160°C under stirring conditions, and react at constant temperature for 6 hours Afterwards, the reaction was terminated, and the molten fluid reaction product flowed out of the reaction vessel, and cooled to room temperature to form a light yellow glassy transparent solid, which was the primary intermediate ABD, and its infrared spectrum was as attached figure 1 As shown, the thermogravimetric curve is attached figure 2 shown.
[0036] Take 85.29g (0.10mol) of primary intermediate ABD and 31.68g (0.24mol) of 50wt.% hypophosphorous acid aqueous solution into a reaction vessel containing 500mL of propanol, heat up to 65°C, and stir until the reactants are completely After dissolving, add 9.85g (0.06mol) azobisisobutyronitrile initiator, stir and react at a constant temperature for 48 hours to obtain the seco...
Embodiment 2
[0038] Add 42.05g (0.10mol) of o-diallyl bisphenol A diglycidyl ether, 64.85g (0.30mol) of DOPO and 100mL of dichlorobenzene into the reaction vessel, and raise the temperature of the reaction system to 170°C while stirring. After stirring the reaction at constant temperature for 8 hours, the reaction was terminated, and the solvent dichlorobenzene was distilled off under reduced pressure, and the molten liquid reaction product was flowed out of the reaction vessel, and cooled to room temperature to form a light yellow glassy transparent solid, which was the primary intermediate Body ABD.
[0039] Take 85.29g (0.10mol) of primary intermediate ABD and 7.92g (0.12mol) of anhydrous hypophosphorous acid into a reaction vessel filled with 400mL of ethanol, raise the temperature to 66°C, stir well until the reactants are completely dissolved, then add 3.45 g (0.015mol) dimethyl azobisisobutyrate initiator, stirred and reacted at a constant temperature for 36 hours to obtain the seco...
Embodiment 3
[0041] Add 84.11g (0.20mol) of o-diallyl bisphenol A diglycidyl ether, 86.47g (0.40mol) of DOPO and 150mL of xylene into the reaction vessel, and raise the temperature of the reaction system to 145°C under stirring conditions, and keep the temperature constant After stirring the reaction for 10 hours, the reaction was terminated, and the solvent xylene was removed by distillation under reduced pressure, and the molten liquid reaction product flowed out of the reaction vessel, and cooled to room temperature to form a light yellow glassy transparent solid, which was the primary intermediate ABD .
[0042] Take 85.29g (0.10mol) of primary intermediate ABD and 19.36g (0.22mol) of sodium hypophosphite into a reaction vessel containing 600mL of ethanol, raise the temperature to 71°C, stir well until the reactants are completely dissolved, then add 19.38g (0.08mol) dibenzoyl peroxide initiator, after constant temperature stirring reaction for 45 hours, the secondary intermediate ABDP...
PUM
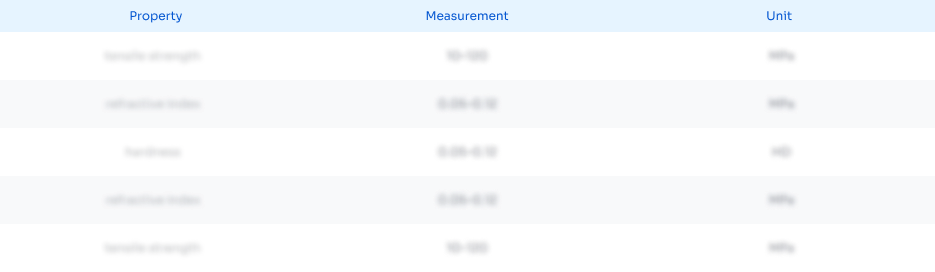
Abstract
Description
Claims
Application Information

- R&D
- Intellectual Property
- Life Sciences
- Materials
- Tech Scout
- Unparalleled Data Quality
- Higher Quality Content
- 60% Fewer Hallucinations
Browse by: Latest US Patents, China's latest patents, Technical Efficacy Thesaurus, Application Domain, Technology Topic, Popular Technical Reports.
© 2025 PatSnap. All rights reserved.Legal|Privacy policy|Modern Slavery Act Transparency Statement|Sitemap|About US| Contact US: help@patsnap.com