Method for high throughput preparation of magnesium alloy block samples
A high-throughput technology for magnesium alloys, applied in the field of high-throughput experiments of materials, can solve the problems of long magnesium alloy cycle, unsuitable for rapid preparation of magnesium alloy materials, inaccurate control of magnesium alloy components, etc., and achieve a fast configuration process Effect
- Summary
- Abstract
- Description
- Claims
- Application Information
AI Technical Summary
Problems solved by technology
Method used
Image
Examples
Embodiment 1
[0034] It is necessary to prepare 16 magnesium alloy samples of Mg-(0.25~4)Zn(at.%), and the concentration changes quasi-continuously. Complete the quasi-negative electrode preparation as described in the manual, insert the quasi-negative electrode into the gradient composite ceramic sleeve to complete the negative electrode assembly. Configure galvanizing solution, the formula is: zinc oxide 45~58g / L, potassium chloride 125~158g / L, boric acid 35~50g / L, ethanolamine 0.45~0.58g / L, linalin 0.5~0.8g / L, Triethanolamine 0.9~1.0g / L, control temperature during electroplating process is 20~48℃, cathode current density 0.5~6A / dm 2 . Installing the zinc positive electrode, it is measured that it takes 30 seconds to complete Mg-0.25Zn (at.%). Fully immerse the negative electrode in the galvanizing electrolyte, and move it up 3cm every 30 seconds, which is the position of 2 sample windows. The electroplating of zinc is completed after 8 minutes. Plating took a total of 8 minutes. Dis...
Embodiment 2
[0036] It is necessary to prepare 128 magnesium alloy samples of Mg-(0.4~3.5)Zn-(0.3~0.6)Gd (at.%), and the concentration changes quasi-continuously. Complete the quasi-negative electrode preparation according to the process described in the manual, and insert the 4 quasi-negative electrodes into the gradient composite ceramic sleeve to complete the assembly of the 4 negative electrodes. Configure galvanizing solution, the formula is: zinc oxide 45~58g / L, potassium chloride 125~158g / L, boric acid 35~50g / L, ethanolamine 0.45~0.58g / L, linalin 0.5~0.8g / L, Triethanolamine 0.9~1.0g / L, control temperature during electroplating process is 20~48℃, cathode current density 0.5~6A / dm 2 . Install the zinc positive electrode, and it takes 12 seconds to complete Mg-0.1Zn (at.%). The 4 negative electrodes were completely immersed in the galvanizing electrolyte, and the electroplating was completed for 48 seconds to complete Mg-0.4Zn (at.%) electroplating. Then move up 1.5cm every 12 secon...
Embodiment 3
[0038] It is necessary to prepare 16 magnesium alloy samples of Mg-(3.3~3.6)Zn-(0.325~0.4)Cu(at.%), and the composition changes separately. Complete the quasi-negative electrode preparation according to the process described in the manual, insert 4 quasi-negative electrodes into holes 1, 9, 17, and 25 in the quaternary discrete composite ceramic jacket A1, and complete the negative electrode assembly A1. Configure galvanizing solution, the formula is: zinc oxide 45~58g / L, potassium chloride 125~158g / L, boric acid 35~50g / L, ethanolamine 0.45~0.58g / L, linalin 0.5~0.8g / L, Triethanolamine 0.9~1.0g / L, control temperature during electroplating process is 20~48℃, cathode current density 0.5~6A / dm 2 . Install the zinc positive electrode, and it takes 12 seconds to complete Mg-0.1Zn (at.%). The negative electrode is completely immersed in the galvanizing electrolyte, and the 3.3Zn (at.%) electroplating is completed in 6 minutes and 36 seconds. Then insert 4 quasi-negative electrodes...
PUM
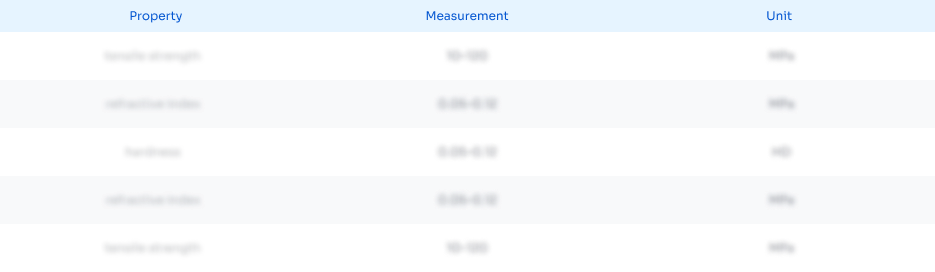
Abstract
Description
Claims
Application Information

- R&D
- Intellectual Property
- Life Sciences
- Materials
- Tech Scout
- Unparalleled Data Quality
- Higher Quality Content
- 60% Fewer Hallucinations
Browse by: Latest US Patents, China's latest patents, Technical Efficacy Thesaurus, Application Domain, Technology Topic, Popular Technical Reports.
© 2025 PatSnap. All rights reserved.Legal|Privacy policy|Modern Slavery Act Transparency Statement|Sitemap|About US| Contact US: help@patsnap.com