Biomedical magnesium alloy and preparation method thereof
A biomedical and magnesium alloy technology, applied in the field of biomedical metal materials, can solve problems such as fast degradation rate, achieve low raw material cost, enhance solid solution strengthening effect, and ensure mechanical properties
- Summary
- Abstract
- Description
- Claims
- Application Information
AI Technical Summary
Problems solved by technology
Method used
Image
Examples
Embodiment 1
[0027] Preparation of as-cast Mg-4.0wt% Zn-0.1wt% Mn-0.2wt% Ca magnesium alloy, Zn / Ca (atomic ratio 12.25) in the alloy.
[0028] 1) Raw material preparation: The test raw materials are 916g of pure magnesium (99.9wt.%), 43.7g of pure zinc (99.99wt.%) (calculated according to 10% burning loss), 27.5g of Mg-9.4wt.%Ca master alloy ( Calculated by 30% burning loss) and 17.4g of Mg-7.4wt.%Mn master alloy (calculated based on 30% burning loss), and the raw materials were polished with grinding wheels to remove surface oxides.
[0029] 2) Melting:
[0030] In order to prevent the oxidation or combustion of the magnesium alloy melt, N 2 +SF 6 The mixed protective gas, where, N 2 and SF 6 The flow ratio is 100:1;
[0031] a) Dry the crucible, slag removal tool, stirring rod and mold in an oven at 200°C for use;
[0032] b) Put the treated crucible into a resistance furnace, set the temperature to 300°C, and when the furnace temperature reaches, pass in protective gas;
[0033] ...
Embodiment 2
[0039] Preparation of as-cast Mg-2.0wt% Zn-0.2wt% Mn-0.5wt% Ca magnesium alloy, Zn / Ca (atomic ratio 2.45) in the alloy.
[0040] 1) Raw material preparation: The test raw materials are 882g of pure magnesium (99.9wt.%), 21.9g of pure zinc (99.99wt.%) (calculated according to 15% burning loss), 68.8g of Mg-9.4wt.% Ca master alloy ( 30% burning loss calculation) and Mg-7.4wt.%Mn master alloy 34.9g (calculation is based on 30% burning loss), and the raw material is polished with a grinding wheel to remove surface oxides.
[0041] 2) Melting:
[0042] In order to prevent the oxidation or combustion of the magnesium alloy melt, N 2 +SF 6 The mixed protective gas, where, N 2 and SF 6 The flow ratio is 100:1;
[0043] a) Dry the crucible, slag removal tool, stirring rod and mold in an oven at 200°C for use;
[0044] b) Put the treated crucible into a resistance furnace, set the temperature to 300°C, and when the furnace temperature reaches, pass in protective gas;
[0045] c) ...
Embodiment 3
[0051] Preparation of as-cast Mg-1.0wt% Zn-0.05wt% Mn-0.2wt% Ca magnesium alloy, Zn / Ca (atomic ratio 3.06) in the alloy.
[0052] 1) Raw material preparation: The test raw materials are 924g of pure magnesium (99.9wt.%), 10.9g of pure zinc (99.99wt.%) (calculated according to 15% burning loss), 27.61g of Mg-9.4wt.%Ca master alloy ( Calculated by 30% burning loss) and 8.77g of Mg-7.4wt.% Mn master alloy (calculated by 30% burning loss), and the raw materials were polished with grinding wheels to remove surface oxides.
[0053] 2) Melting:
[0054] In order to prevent the oxidation or combustion of the magnesium alloy melt, N 2 +SF 6 The mixed protective gas, where, N 2 and SF 6 The flow ratio is 100:1;
[0055] a) Dry the crucible, slag removal tool, stirring rod and mold in an oven at 200°C for use;
[0056] b) Put the treated crucible into a resistance furnace, set the temperature to 300°C, and when the furnace temperature reaches, pass in protective gas;
[0057] c) A...
PUM
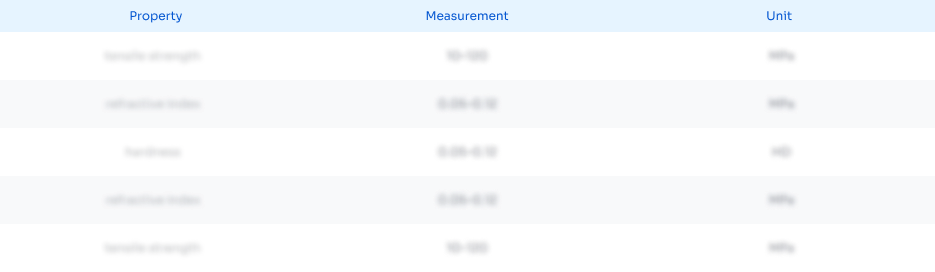
Abstract
Description
Claims
Application Information

- R&D
- Intellectual Property
- Life Sciences
- Materials
- Tech Scout
- Unparalleled Data Quality
- Higher Quality Content
- 60% Fewer Hallucinations
Browse by: Latest US Patents, China's latest patents, Technical Efficacy Thesaurus, Application Domain, Technology Topic, Popular Technical Reports.
© 2025 PatSnap. All rights reserved.Legal|Privacy policy|Modern Slavery Act Transparency Statement|Sitemap|About US| Contact US: help@patsnap.com