Low carbon alloy steel treatment method
A low-carbon alloy steel and a processing method technology, applied in the field of metal processing, can solve the problems of increasing the strength and plastic product of steel, and achieve the effects of promoting the distribution of alloy elements, increasing the enrichment degree and increasing the aggregation effect
- Summary
- Abstract
- Description
- Claims
- Application Information
AI Technical Summary
Problems solved by technology
Method used
Image
Examples
Embodiment 1
[0035] Steel slabs with the following compositions were smelted in a ZG-50 vacuum induction melting furnace and forged into slabs with a thickness of 75mm;
[0036] 0.19wt% of C; 1.5wt% of Si; 1.3wt% of Mn; 0.010wt% of P; 0.017wt% of Al; 0.009wt% of S; 0.0003wt% of B; the balance of Fe;
[0037] The slab is heated to 1200°C in a high-temperature box-type heating furnace and kept for 3 hours to homogenize the composition of alloy elements, and then it is hot-rolled. After rolling at 950°C for 5 passes, a hot-rolled sheet for thermal simulation experiments with a thickness of 15mm was rolled, and turned into a cylindrical sample of Φ8mm×12mm;
[0038] The sample was heated to 770°C at a rate of 10°C / s, and then the sample was immediately heated for 1s -1 The deformation rate was compressed by 10%, held for 1800s, and then water quenched to room temperature.
Embodiment 2
[0045] Steel slabs with the following compositions were smelted in a ZG-50 vacuum induction melting furnace and forged into slabs with a thickness of 75mm;
[0046] 0.18wt% C; 1.58wt% Si; 2.06wt% Mn; 0.41wt% Cu; 0.33wt% Ni; 0.008wt% P; 0.005wt% S; Fe;
[0047] The slab is heated to 1200°C in a high-temperature box-type heating furnace and kept for 3 hours to homogenize the composition of alloy elements, and then it is hot-rolled. After rolling at 950°C for 5 passes, a hot-rolled sheet for thermal simulation experiments with a thickness of 15mm was rolled, and turned into a cylindrical sample of Φ8mm×12mm;
[0048] The sample was heated to 740°C at a rate of 10°C / s, and then the sample was immediately heated for 1s -1 The deformation rate was compressed by 10%, held for 600s, and then water quenched to room temperature.
PUM
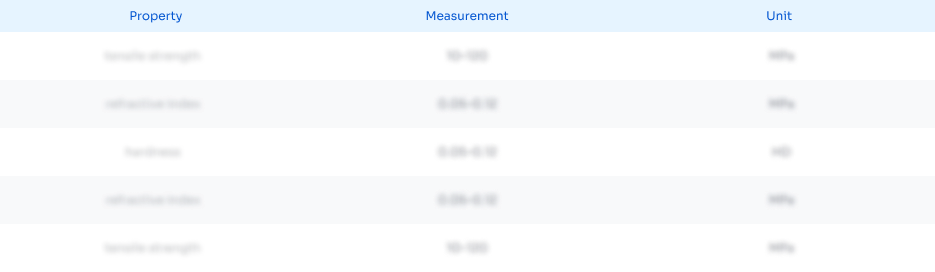
Abstract
Description
Claims
Application Information

- Generate Ideas
- Intellectual Property
- Life Sciences
- Materials
- Tech Scout
- Unparalleled Data Quality
- Higher Quality Content
- 60% Fewer Hallucinations
Browse by: Latest US Patents, China's latest patents, Technical Efficacy Thesaurus, Application Domain, Technology Topic, Popular Technical Reports.
© 2025 PatSnap. All rights reserved.Legal|Privacy policy|Modern Slavery Act Transparency Statement|Sitemap|About US| Contact US: help@patsnap.com