A method of producing high-purity sodium sulfide
A production method and technology for sodium sulfide, applied in chemical instruments and methods, sulfur compounds, alkali metal sulfides/polysulfides, etc., can solve the problems of incomplete calcination of pulverized coal, high iron content, small contact area, etc. The effect of improving the conversion rate of raw materials, reducing the content of SO2, and reducing the content of iron ions
- Summary
- Abstract
- Description
- Claims
- Application Information
AI Technical Summary
Problems solved by technology
Method used
Examples
Embodiment 1
[0010] The present embodiment focuses on the production method of high-purity sodium sulfide, which may further comprise the steps:
[0011] S100: Put raw coal, Glauber's salt, and catalyst ferric oxide in a ball mill, and grind to 120-130 mesh. Among them, Glauber's salt: coal: ferric oxide is: 5:2:0.04 (weight ratio).
[0012] S200: After grinding, send it to the mixer for mixing and stirring. After grinding, the contact area between pulverized coal powder and Glauber's salt increases, thereby improving the completeness of the reaction. Stir the pulverized coal powder and thenardite powder to make it evenly mixed, so as to make the full contact between the thenardite powder and the coal powder, and improve the completeness of the reaction.
[0013] S300: After the stirring is completed, the mixture is sprayed into a calciner, and calcined and reduced at a high temperature of 900-1100°C. The impurity in industrial sodium sulfide products is Na 2 CO 3 、Na 2 S x 、Na 2 S...
experiment example 1
[0019] Add 3100g / m 3 Sodium carbonate and 900g / m 3 Sodium sulfide, then add sodium hydroxide to make the pH value of Glauber's salt carbon reduction leaching solution reach 10; then add 0.35%wt polyferric chloride to settle the various precipitates generated, and finally add sulfuric acid to adjust Glauber's salt carbon reduction leaching solution The PH value reaches 7.2, so that the Glauber's salt carbon reduction leaching solution with extremely low impurity content can be obtained after refining and purification treatment, and then input into the Glauber's salt carbon reduction leaching solution storage tank, and then pumped into the crystallizer for 70 minutes to quickly freeze and crystallize in a vacuum to the process The temperature is 30°C, the vacuum degree is controlled at -0.096Mp, and it is put into a static separation device for 35 minutes, and then the centrifuge is used for solid-liquid separation. The mother liquor is sent to the mother liquor storage tank, an...
experiment example 2
[0021] Add 2900g / m 3 Sodium carbonate and 980.3g / m 3Sodium sulfide, then add sodium hydroxide to make the pH value of Glauber's salt carbon reduction leaching solution reach 10; then add 0.45%wt polyferric chloride to settle the various precipitates generated, and finally add sulfuric acid to adjust Glauber's salt carbon reduction leaching solution The PH value reaches 6.8. In this way, the Glauber’s salt carbon reduction leaching solution with extremely low impurity content can be obtained after refining and purification treatment, which is input into the Glauber’s salt carbon reduction leaching solution storage tank, and then pumped into the crystallizer for 80 minutes to freeze and crystallize quickly in a vacuum. The process temperature is 60°C, the vacuum degree is controlled at -0.089Mpa, and it is put into a static separation device for 40 minutes, and then the centrifuge is used for solid-liquid separation. The mother liquor is sent to the mother liquor storage tank, a...
PUM
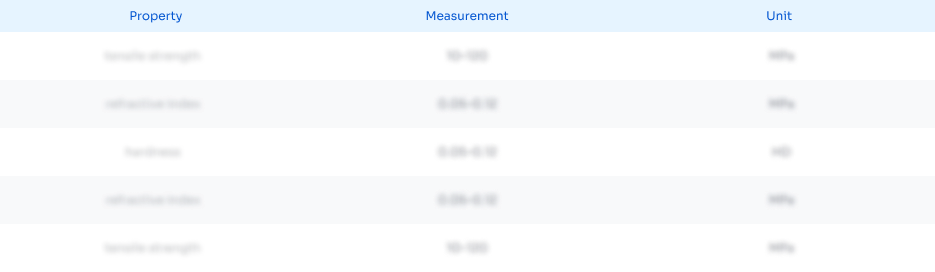
Abstract
Description
Claims
Application Information

- R&D
- Intellectual Property
- Life Sciences
- Materials
- Tech Scout
- Unparalleled Data Quality
- Higher Quality Content
- 60% Fewer Hallucinations
Browse by: Latest US Patents, China's latest patents, Technical Efficacy Thesaurus, Application Domain, Technology Topic, Popular Technical Reports.
© 2025 PatSnap. All rights reserved.Legal|Privacy policy|Modern Slavery Act Transparency Statement|Sitemap|About US| Contact US: help@patsnap.com