Preparation method of tea dyed costume fabric
A fabric and clothing technology, applied in the field of tea-dyed clothing fabric preparation, can solve the problems of low wash fastness, poor dyeing reproducibility, low dyeing rate, etc., to improve wet rubbing fastness, uniform dyeing, and dyeing The effect of fastness enhancement
- Summary
- Abstract
- Description
- Claims
- Application Information
AI Technical Summary
Problems solved by technology
Method used
Examples
example 1
[0045] (1) Add 50g of crushed tea leaves and 1g of fatty alcohol polyoxyethylene ether into 900ml of tap water, raise the temperature to 98°C, control the extraction time at 3 hours, add water during the period to keep the total liquid volume unchanged, and filter after extraction Residue, concentrate solution to the tea dye solution that mass fraction is 3%;
[0046] (2) Preparation of finishing solution
[0047] 100 g of glacial acetic acid aqueous solution with a mass concentration of 4% was gradually added to chitosan powder 15 g and guar gum hydroxypropyltrimethylammonium chloride 2.6 g, and after stirring evenly, add 100 g of water and mix thoroughly to obtain a finishing solution;
[0048] (3) Finish the pure cotton knitted fabric by padding method by using the finishing solution: 60g of the finishing solution of the pure cotton knitted fabric in the padding step (2), after the second dipping and the second rolling, dry at an ambient temperature of 65°C for 3 min;
[00...
example 2
[0051] (1) Add 60g of crushed tea leaves and 2g of sodium citrate into 1000ml of tap water, raise the temperature to 98°C, control the extraction time at 3 hours, add water during the period to keep the total liquid volume constant, and filter the residue after extraction. Concentrating the solution to a mass fraction of 5% tea dye solution;
[0052] (2) Preparation of finishing solution
[0053] Gradually add 200 g of glacial acetic acid solution with a mass concentration of 4% into 18 g of chitosan powder and 3.6 g of trehalose, stir evenly at the same time, add 150 g of water and mix thoroughly to obtain a finishing solution;
[0054] (3) Finish the pure cotton knitted fabric with the padding method by using the finishing solution: 70g of the pure cotton knitted fabric is soaked with the finishing solution in step (2), after the second dipping and the second rolling, dry it at an ambient temperature of 75°C for 3 min;
[0055] (4) Dye the pure cotton knitted fabric after ...
example 3
[0057] (1) Add 70g of pulverized tea leaves and 1.4g of hydroxypropyl methylcellulose into 1200ml of tap water, raise the temperature to 98°C, control the extraction time at 4 hours, add water during the period to keep the total liquid volume unchanged, and extract Finish filtering residue, concentrate solution to the tea dye solution that mass fraction is 4%;
[0058] (2) Preparation of finishing solution
[0059] Gradually add 200 g of glacial acetic acid solution with a mass concentration of 4% into 20 g of chitosan powder and 3.6 g of glucosamine sulfate, stir evenly at the same time, add 100 g of water and mix thoroughly to obtain a finishing solution;
[0060] (3) Finish the pure cotton knitted fabric by padding method with the finishing solution; take 60g of the finishing solution of the pure cotton knitted fabric in the padding step (2), after the second dipping and the second rolling, dry it at an ambient temperature of 75°C for 4 min;
[0061] (4) Dye the pure cott...
PUM
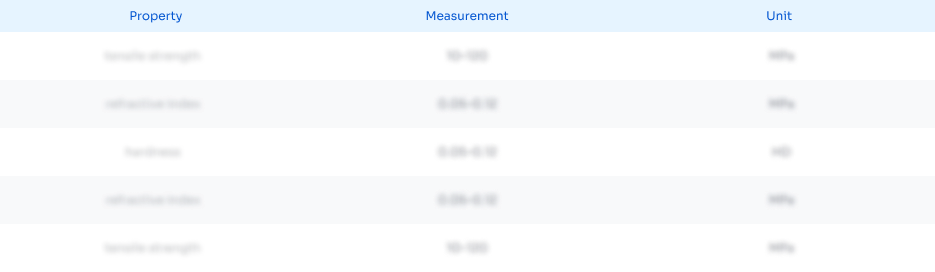
Abstract
Description
Claims
Application Information

- R&D Engineer
- R&D Manager
- IP Professional
- Industry Leading Data Capabilities
- Powerful AI technology
- Patent DNA Extraction
Browse by: Latest US Patents, China's latest patents, Technical Efficacy Thesaurus, Application Domain, Technology Topic, Popular Technical Reports.
© 2024 PatSnap. All rights reserved.Legal|Privacy policy|Modern Slavery Act Transparency Statement|Sitemap|About US| Contact US: help@patsnap.com