Method for preparing Sm-Co alloy magnetic material through electric dechloridation
A magnetic material, samarium-cobalt technology, which is applied in the field of preparing samarium-cobalt alloy magnetic materials, can solve the problems of easy cracks, complicated process, and high risk of samarium-cobalt alloy, and achieve the effect of low cost, simple and efficient process, and green metallurgy
- Summary
- Abstract
- Description
- Claims
- Application Information
AI Technical Summary
Problems solved by technology
Method used
Image
Examples
specific Embodiment approach 1
[0017] Specific embodiment one: a kind of method for preparing samarium-cobalt alloy magnetic material by electric dechlorination of the present embodiment is carried out according to the following steps:
[0018] 1. According to LiCl, KCl, SmCl 3 、CoCl 2 The mass ratio is (44~45):(44~45):(2~10):3 Weigh LiCl, KCl, SmCl 3 and CoCl 2 , first add LiCl and KCl to the electrolytic tank of the electrolytic furnace, heat and melt, and then add SmCl 3 and CoCl 2 , continue heating and melting to obtain LiCl-KCl-SmCl 3 -CoCl 2 electrolyte system;
[0019] 2. Using metal molybdenum as the working electrode and graphite as the auxiliary electrode, the electrolysis temperature is 640-850°C and the current is 1.55-5.90Acm -2 Under the conditions of electrolysis for 1 to 2 hours, the material deposited in the electrolytic cell is taken out, lowered to normal temperature, the solid phase is filtered out, washed and dried to obtain a samarium cobalt alloy magnetic material.
specific Embodiment approach 2
[0020] Specific embodiment two: the difference between this embodiment and specific embodiment one is that LiCl, KCl, SmCl in step one 3 、CoCl 2 The mass ratio is (44~45):(44~45):4:3. Others are the same as in the first embodiment.
[0021] The samarium-cobalt alloy obtained under the electrolyte ratio conditions of this embodiment is Sm 2 co 17 .
specific Embodiment approach 3
[0022] Specific embodiment three: the difference between this embodiment and specific embodiment one or two is that LiCl, KCl, SmCl in step one 3 、CoCl 2 The mass ratio is (44~45):(44~45):6:3. Others are the same as in the first or second embodiment.
[0023] The samarium-cobalt alloy obtained under the electrolyte ratio conditions of this embodiment is Sm 2 co 17 .
PUM
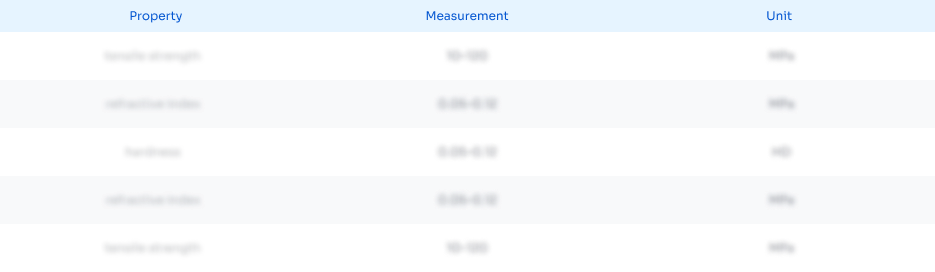
Abstract
Description
Claims
Application Information

- R&D Engineer
- R&D Manager
- IP Professional
- Industry Leading Data Capabilities
- Powerful AI technology
- Patent DNA Extraction
Browse by: Latest US Patents, China's latest patents, Technical Efficacy Thesaurus, Application Domain, Technology Topic, Popular Technical Reports.
© 2024 PatSnap. All rights reserved.Legal|Privacy policy|Modern Slavery Act Transparency Statement|Sitemap|About US| Contact US: help@patsnap.com