Improved multi-phase dephosphorizing agent for high-phosphorus molten iron and application of improved multi-phase dephosphorizing agent
A phase dephosphorization agent and an improved technology, applied in the field of iron and steel metallurgy, can solve the problems of environmental problems, slow dephosphorization and slagging, pollution, etc., and achieve the effects of facilitating recycling, improving dephosphorization effect, and reducing production costs.
- Summary
- Abstract
- Description
- Claims
- Application Information
AI Technical Summary
Problems solved by technology
Method used
Image
Examples
Embodiment 1
[0039] Each component of the heterogeneous dephosphorization agent is calculated as Fe by mass percentage 2 o 3 51%, CaO 22%, Al 2 o 3 3%, SiO 2 16%, Na 2 O 5%, BaO 3%.
[0040] Dephosphorization process of heterogeneous dephosphorization agent:
[0041] 1) Put 400g of prepared pig iron into the induction furnace to melt into molten iron (the composition of molten iron is [P]=0.723wt.%, [Si]=0.105wt.%, [C]=4.05wt.%);
[0042] 2) By adjusting the power of the induction furnace, control the dephosphorization temperature to 1370°C, add 35g of the prepared dephosphorization agent into the molten iron, and stir evenly with a steel rod;
[0043] 3) Dephosphorization ends after 25 minutes.
[0044] After the dephosphorization, the molten iron sample was taken for elemental analysis and detection. After the dephosphorization treatment, the molten iron contained 0.050wt.% phosphorus, and the dephosphorization rate was 91.3%.
[0045] The heterogeneous dephosphorization final ...
Embodiment 2
[0047] Each component of the heterogeneous dephosphorization agent is calculated as Fe by mass percentage 2 o 3 51%, CaO 20%, Al 2 o 3 4%, SiO 2 17%, Na 2 O 6%, BaO 2%.
[0048] Dephosphorization process of heterogeneous dephosphorization agent:
[0049] 1) Put 400g of prepared pig iron into the induction furnace to melt into molten iron (the composition of molten iron is [P]=0.453wt.%, [Si]=0.10wt.%, [C]=4.05wt.%);
[0050] 2) By adjusting the power of the induction furnace, control the dephosphorization temperature to 1370°C, add 35g of the prepared dephosphorization agent into the molten iron, and stir evenly with a steel rod;
[0051] 3) Dephosphorization ends after 25 minutes.
[0052] After the dephosphorization, the molten iron sample was taken for elemental analysis and detection. After the dephosphorization treatment, the molten iron contained 0.033wt.% phosphorus, and the dephosphorization rate was 92.8%.
Embodiment 3
[0054] Each component of the heterogeneous dephosphorization agent is calculated as Fe by mass percentage 2 o 3 55%, CaO16%, Al 2 o 3 4%, SiO 2 17%, Na 2 O 5%, BaO 2%.
[0055] Dephosphorization process of heterogeneous dephosphorization agent:
[0056] 1) Put 400g of prepared pig iron into the induction furnace to melt into molten iron (the composition of molten iron is [P]=0.993wt.%, [Si]=0.10wt.%, [C]=4.05wt.%);
[0057] 2) By adjusting the power of the induction furnace, control the dephosphorization temperature to 1410°C, add 35g of the prepared dephosphorization agent into the molten iron, and stir evenly with a steel rod;
[0058] 3) Dephosphorization ends after 25 minutes.
[0059] After dephosphorization, the molten iron sample was taken for elemental analysis and detection. After dephosphorization, the molten iron contained 0.058wt.% phosphorus, and the dephosphorization rate was 94.1%.
PUM
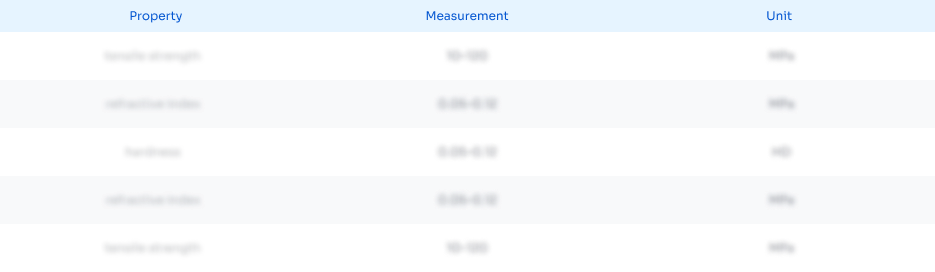
Abstract
Description
Claims
Application Information

- R&D Engineer
- R&D Manager
- IP Professional
- Industry Leading Data Capabilities
- Powerful AI technology
- Patent DNA Extraction
Browse by: Latest US Patents, China's latest patents, Technical Efficacy Thesaurus, Application Domain, Technology Topic, Popular Technical Reports.
© 2024 PatSnap. All rights reserved.Legal|Privacy policy|Modern Slavery Act Transparency Statement|Sitemap|About US| Contact US: help@patsnap.com