Method of vegetable fat recycling from spent bleaching clay
A technology for vegetable oil and waste clay, which is applied in the production of fat oil/fat, refining of fat oil/fat, and fat production, etc., can solve the problems of high safety requirements in the production workshop, high residual moisture in oil, and difficulty in demulsification of the emulsion. The effect of shortening the oil-water separation time, promoting the thermal effect, and shortening the emulsification time
- Summary
- Abstract
- Description
- Claims
- Application Information
AI Technical Summary
Problems solved by technology
Method used
Image
Examples
Embodiment 1
[0029] A method for recovering vegetable oil from waste white clay, using the waste white clay produced by the linseed oil refining process as raw material, the oil content in the waste white clay is 37.1% (w / w), and the water content is 3% (w / w) , the method includes the steps of:
[0030] ① Heat the waste clay to 70°C and centrifuge at 4000r / min for 25min to obtain waste clay and liquid I with an oil content of 25.5% (w / w) after centrifugation;
[0031] ② Crush the centrifuged waste clay to 30 meshes, add water twice the weight of the centrifuged and crushed waste clay, set the ultrasonic power to 400W, microwave power to 450W, and conduct ultrasonic-microwave treatment at 65°C for 9 minutes;
[0032] Then add 0.3% (w / v) composite surfactant, the composite surfactant is 3:1 by weight, mix sodium lauryl sulfate with fatty alcohol polyoxyethylene ether, the power of superemulsification is 270W, 65 ℃ ultrasonic emulsification 7min;
[0033] The power of microwave demulsificat...
Embodiment 2
[0038] A method for recovering vegetable oil from waste white clay, using the waste white clay produced by perilla oil refining process as raw material, the oil content in the waste white clay is 35.3% (w / w), and the water content is 2.8% (w / w) , the method includes the steps of:
[0039] ① Heat the waste clay to 75°C and centrifuge at 3500r / min for 30min to obtain waste clay and liquid I with an oil content of 23.7% (w / w) after centrifugation;
[0040] ② Crush the centrifuged waste clay to 30 mesh, add water twice the weight of the centrifuged and crushed waste clay, set the ultrasonic power to 350W, microwave power to 500W, and conduct ultrasonic-microwave treatment at 65°C for 10 minutes;
[0041] Then add 0.3% (w / v) composite surfactant, the composite surfactant is 4:1 by weight, mix sodium lauryl sulfate with fatty alcohol polyoxyethylene ether, the power of ultrasonic emulsification is 300W, 65 ℃ ultrasonic emulsification 6min;
[0042] The power of microwave demulsifi...
Embodiment 3
[0047] A method for recovering vegetable oil from waste white clay, using the waste white clay produced by the refining process of sunflower oil as raw material, the oil content in the waste white clay is 32.6% (w / w), and the water content is 3.3% (w / w) , the method includes the steps of:
[0048] ① Heat the waste clay to 80°C and centrifuge at 4000r / min for 25min to obtain waste clay and liquid I with an oil content of 21.7% (w / w) after centrifugation;
[0049] ② Crush the centrifuged waste clay to 40 meshes, add water twice the weight of the centrifuged and crushed waste clay, set the ultrasonic power to 400W, microwave power to 500W, and conduct ultrasonic-microwave treatment at 65°C for 7 minutes;
[0050] Then add 0.2% (w / v) composite surfactant, the composite surfactant is 4:1 by weight, mix sodium lauryl sulfate with fatty alcohol polyoxyethylene ether, the power of ultrasonic emulsification is 300W, 65 ℃ Phacoemulsification 7min
[0051] The power of microwave demuls...
PUM
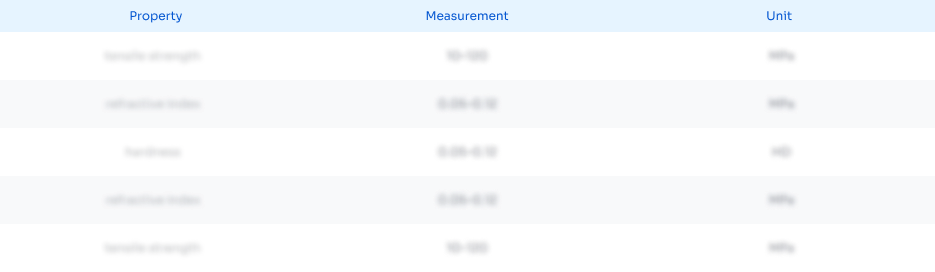
Abstract
Description
Claims
Application Information

- R&D
- Intellectual Property
- Life Sciences
- Materials
- Tech Scout
- Unparalleled Data Quality
- Higher Quality Content
- 60% Fewer Hallucinations
Browse by: Latest US Patents, China's latest patents, Technical Efficacy Thesaurus, Application Domain, Technology Topic, Popular Technical Reports.
© 2025 PatSnap. All rights reserved.Legal|Privacy policy|Modern Slavery Act Transparency Statement|Sitemap|About US| Contact US: help@patsnap.com