Waste polyurethane recycling technique
A technology for recycling and processing polyurethane, which is applied in the field of recycling and processing waste polyurethane, which can solve the problems of secondary pollution by heat recovery method, unfavorable recycling, difficult purification of polyols, etc., to promote product stratification, shorten heating and cooling Time, the effect of lowering the temperature
- Summary
- Abstract
- Description
- Claims
- Application Information
AI Technical Summary
Problems solved by technology
Method used
Examples
Embodiment
[0025] A recycling process for waste polyurethane, comprising the following steps:
[0026] Step S1: crushing waste polyurethane into polyurethane particles;
[0027] Step S2: Add polyurethane particles, water, antioxidant, lithium hydroxide, decomposing agent and catalyst into the reaction kettle. Adding lithium hydroxide can effectively accelerate the hydrolysis reaction, which is beneficial to reduce the temperature required for hydrolysis and reduce the cost of hydrolysis. The required energy consumption is protected by inert gas. The reaction kettle is heated in a salt bath and kept at 218~399°C and 50~150kPa for 3~5 hours. The catalyst is carbodiimide, and the decomposition agent can be selected One or more combinations of 1,4-butanediol, 1,2-propanediol, diethylene glycol, diethylene glycol, dipropylene glycol, neopentyl glycol, and methylpropanediol, and the amount of the decomposer is polyurethane particles 1.5~2 times of that, the antioxidants are hindered phenolic ...
PUM
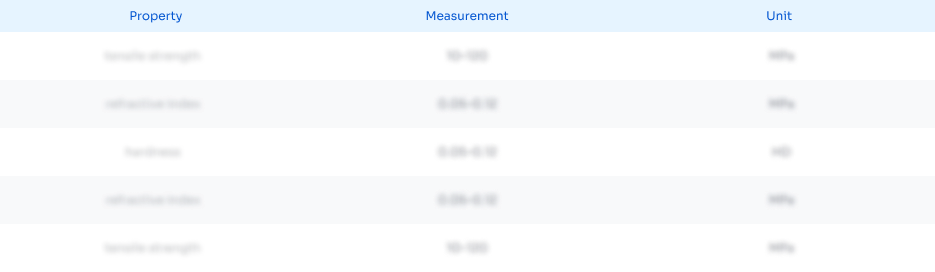
Abstract
Description
Claims
Application Information

- R&D
- Intellectual Property
- Life Sciences
- Materials
- Tech Scout
- Unparalleled Data Quality
- Higher Quality Content
- 60% Fewer Hallucinations
Browse by: Latest US Patents, China's latest patents, Technical Efficacy Thesaurus, Application Domain, Technology Topic, Popular Technical Reports.
© 2025 PatSnap. All rights reserved.Legal|Privacy policy|Modern Slavery Act Transparency Statement|Sitemap|About US| Contact US: help@patsnap.com