Clamp for polishing of auto-rotation abrasive flow of rotator workpiece and design method thereof
A design method and self-rotation technology, applied in grinding/polishing equipment, machine tools for surface polishing, machine tools suitable for grinding the edge of workpieces, etc., can solve the problem that the clamping point cannot be polished, the contact between the workpiece and the fixture is damaged, and the rotation Eliminate the uneven material removal on the surface of the workpiece, achieve the effect of convenient mold assembly and disassembly, improve the uniformity of surface processing, and reduce surface roughness
- Summary
- Abstract
- Description
- Claims
- Application Information
AI Technical Summary
Problems solved by technology
Method used
Image
Examples
Embodiment Construction
[0039] The present invention will be further described below in conjunction with the accompanying drawings.
[0040] figure 1 It is a schematic diagram of the eccentric clamping method and the flow channel of the workpiece 1, and is also a schematic diagram of the structure of a single mold 7, Figure 2-3Shown is a schematic diagram of clamping for the non-clamping eccentric rotating abrasive flow machining method of the rotary workpiece 1 (the arrow in the figure is the direction of abrasive flow). It can be seen from the figure that the size of the flow channel is selected according to the actual size of the workpiece 1 , the choice of runner size should ensure the following conditions:
[0041] (1) if Figure 2-3 The size L of the flow channel shown should be approximately equal to and slightly larger than the size of the workpiece 1. On the one hand, it can ensure the smooth clamping of the workpiece 1 during batch processing. On the other hand, it can ensure that the wo...
PUM
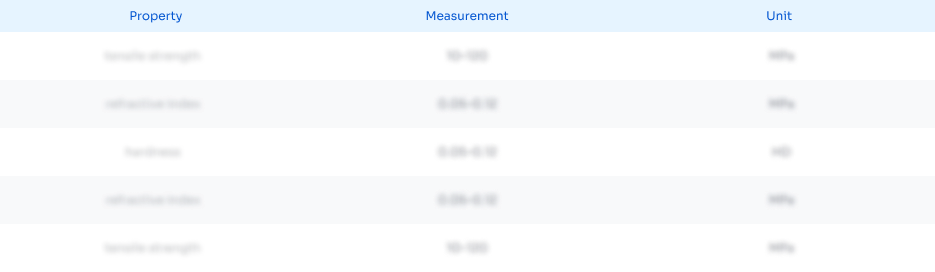
Abstract
Description
Claims
Application Information

- R&D
- Intellectual Property
- Life Sciences
- Materials
- Tech Scout
- Unparalleled Data Quality
- Higher Quality Content
- 60% Fewer Hallucinations
Browse by: Latest US Patents, China's latest patents, Technical Efficacy Thesaurus, Application Domain, Technology Topic, Popular Technical Reports.
© 2025 PatSnap. All rights reserved.Legal|Privacy policy|Modern Slavery Act Transparency Statement|Sitemap|About US| Contact US: help@patsnap.com