Carbon fiber coating layer modifying treatment method
A treatment method and carbon fiber technology, which is applied in fiber treatment, carbon fiber, textiles and papermaking, etc., can solve problems such as increased roughness and carbon fiber surface damage, and achieve the effects of preventing material damage, relieving stress concentration, and improving mechanical properties
- Summary
- Abstract
- Description
- Claims
- Application Information
AI Technical Summary
Problems solved by technology
Method used
Examples
Embodiment 1
[0026] A carbon fiber coating modification treatment method, comprising the steps of:
[0027] 1) Preparation of titanium dioxide sol: adding tetrabutyl titanate into ethanol solution, then slowly adding alcohol solution of hydrochloric acid dropwise, and continuing to stir for 0.5 h after the dropwise addition, to obtain titanium dioxide sol.
[0028] 2) Immerse 6g of acrylonitrile carbon fiber in an organic solvent solution grafted with 10wt% maleic anhydride and heat it to 50°C for 5h, then dry it to obtain CF-1.
[0029] 3) Under ultrasonic conditions of 100°C, add CF-1 into 150ml of potassium permanganate sulfuric acid solution for oxidation etching treatment, after the treatment, naturally cool down to room temperature and wash with water until the pH is 6, and dry to obtain CF-2: The sulfuric acid solution of potassium permanganate is a solution prepared by adding 0.4 g of potassium permanganate to 50 ml of sulfuric acid with a molar concentration of 0.5 mol / L.
[0030...
Embodiment 2
[0033] A carbon fiber coating modification treatment method, comprising the steps of:
[0034] 1) Titanium dioxide sol preparation: adding tetrabutyl titanate to ethanol solution, then slowly adding hydrochloric acid alcohol solution dropwise, and continuing to stir for 0.8 h after the dropwise addition, to obtain titanium dioxide sol.
[0035] 2) Immerse 5g of high-performance pitch-based carbon fiber in acetone solution of 12wt% styrene-acrylonitrile-glycidyl methacrylate, heat it to 60°C for 2 hours, and dry it to obtain CF-1.
[0036] 3) Under ultrasonic conditions at 120°C, add CF-1 into the sulfuric acid solution of potassium permanganate for oxidation and etching treatment. After the treatment, naturally cool down to room temperature and wash with water until the pH is 8, then dry to obtain CF -2; The sulfuric acid solution of potassium permanganate refers to a solution prepared by adding 0.6 g of potassium permanganate to 55 ml of sulfuric acid with a molar concentrati...
Embodiment 3
[0040] A carbon fiber coating modification treatment method, comprising the steps of:
[0041] 1) Preparation of titanium dioxide sol: adding tetrabutyl titanate to ethanol solution, then slowly adding alcohol solution of hydrochloric acid dropwise, and continuing to stir for 1 hour after the dropwise addition, to obtain titanium dioxide sol.
[0042] 2) Dip 8g of acrylonitrile carbon fiber in 15wt% maleic anhydride-grafted ethanol solution and heat to 60°C for 2h, then dry to obtain CF-1.
[0043] 3) Under ultrasonic conditions of 150°C, add CF-1 into the sulfuric acid solution of potassium permanganate for oxidation etching treatment. After the treatment, naturally cool down to room temperature and wash with water until the pH is 7, and dry to obtain CF -2. The sulfuric acid solution of potassium permanganate refers to a solution prepared by adding 0.8 g of potassium permanganate to 60 ml of sulfuric acid with a molar concentration of 0.9 mol / L.
[0044] 4) Disperse CF-2 i...
PUM
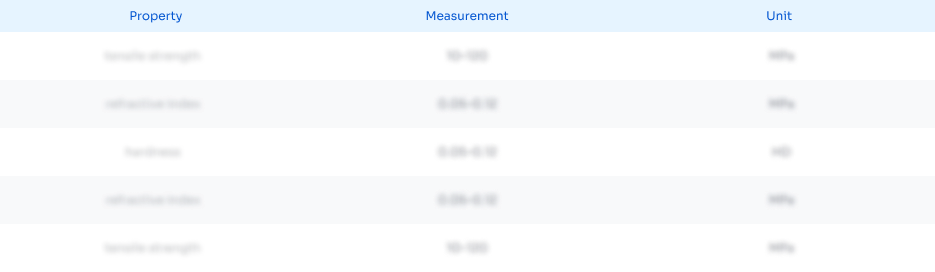
Abstract
Description
Claims
Application Information

- R&D Engineer
- R&D Manager
- IP Professional
- Industry Leading Data Capabilities
- Powerful AI technology
- Patent DNA Extraction
Browse by: Latest US Patents, China's latest patents, Technical Efficacy Thesaurus, Application Domain, Technology Topic, Popular Technical Reports.
© 2024 PatSnap. All rights reserved.Legal|Privacy policy|Modern Slavery Act Transparency Statement|Sitemap|About US| Contact US: help@patsnap.com