Bio-based diatom mud coating material preparation method
A technology based on diatom mud and paint, applied in the field of diatom mud paint preparation, can solve the problems of harming the environment and human health, and the paint is prone to produce harmful substances, and achieves the effects of reducing the preparation cost, strengthening the self-cleaning function and simple process
- Summary
- Abstract
- Description
- Claims
- Application Information
AI Technical Summary
Problems solved by technology
Method used
Examples
example 1
[0019] First weigh 100g of bamboo slices, cut the bamboo slices into 5cm pieces, dry the cut bamboo slices in a 95°C oven until the moisture content of the bamboo slices is 20%, and place the dried bamboo slices in a 25KHz plasma processor , under normal temperature and pressure for 20 minutes to obtain pretreated bamboo chips; then add the pretreated bamboo chips to pulverizer, sieve to obtain 100 mesh bamboo chip powder, and add the bamboo chip powder to the muffle furnace, Control the temperature at 300°C, calcining for 6 hours, raising the temperature to 600°C, calcining for 5 hours, continuing to raise the temperature to 1000°C, and calcining for 8 hours to obtain bamboo charcoal fibers for later use; In the beaker, add 200mL deionized water into the beaker, place the beaker on a 3000W ultrasonic extraction machine, ultrasonically extract for 20min, filter, collect the filtrate and filter residue respectively, put the filter residue in the beaker, add 100mL deionized water...
example 2
[0022] First weigh 150g of bamboo slices, cut the bamboo slices into 8cm pieces, dry the cut bamboo slices in an oven at 100°C until the moisture content of the bamboo slices is 25%, and place the dried bamboo slices in a 28KHz plasma processor , under normal temperature and pressure for 25min to obtain pretreated bamboo chips; then add the pretreated bamboo chips to pulverize in a pulverizer, and sieve to obtain 110 mesh bamboo chip powders, and add the bamboo chip powders to the muffle furnace, Control the temperature at 350°C, calcined for 7 hours, raise the temperature to 700°C, calcined for 5.5 hours, continue to raise the temperature to 1100°C, and calcined for 9 hours to obtain bamboo charcoal fibers for later use; into the beaker, add 250mL deionized water to the beaker, place the beaker on a 3100W ultrasonic extraction machine, ultrasonically extract for 25min, filter, collect the filtrate and filter residue respectively, put the filter residue in the beaker, add 150mL...
example 3
[0025]First weigh 200g of bamboo slices, cut the bamboo slices into 10cm pieces, dry the cut bamboo slices in an oven at 105°C until the moisture content of the bamboo slices is 30%, and place the dried bamboo slices in a 30KHz plasma processor , treated under normal temperature and pressure for 30min to obtain pretreated bamboo chips; then add the pretreated bamboo chips to pulverizer, sieve to obtain 120 mesh bamboo chip powder, and add the bamboo chip powder to the muffle furnace, Control the temperature at 400°C, calcining for 8 hours, raising the temperature to 800°C, calcining for 6 hours, continuing to raise the temperature to 1200°C, and calcining for 10 hours to obtain bamboo charcoal fibers for later use; In the beaker, add 300mL deionized water into the beaker, place the beaker on a 3200W ultrasonic extraction machine, ultrasonically extract for 30min, filter, collect the filtrate and filter residue respectively, put the filter residue in the beaker, add 200mL deioni...
PUM
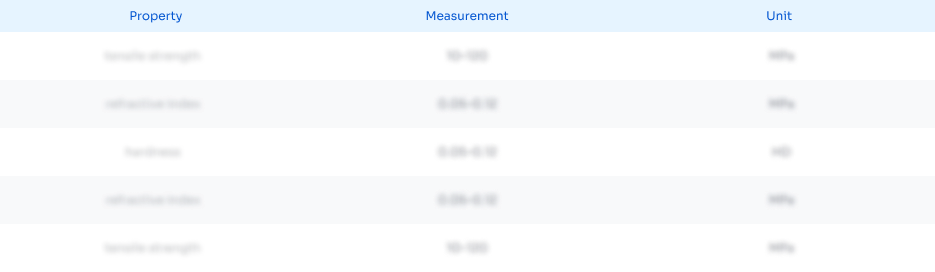
Abstract
Description
Claims
Application Information

- Generate Ideas
- Intellectual Property
- Life Sciences
- Materials
- Tech Scout
- Unparalleled Data Quality
- Higher Quality Content
- 60% Fewer Hallucinations
Browse by: Latest US Patents, China's latest patents, Technical Efficacy Thesaurus, Application Domain, Technology Topic, Popular Technical Reports.
© 2025 PatSnap. All rights reserved.Legal|Privacy policy|Modern Slavery Act Transparency Statement|Sitemap|About US| Contact US: help@patsnap.com