Copper block burying method of printed circuit board
A technology of printed circuit boards and buried copper blocks, which is applied in the fields of printed circuit, printed circuit, and printed circuit manufacturing. High pass rate and good binding effect
- Summary
- Abstract
- Description
- Claims
- Application Information
AI Technical Summary
Problems solved by technology
Method used
Image
Examples
Embodiment Construction
[0029] The present invention will be further described below in conjunction with accompanying drawing and specific embodiment:
[0030] Such as figure 1 Shown, the printed circuit board buried copper block method of the present invention comprises the following steps:
[0031] (1) Use CNC to control the depth of the base material out of the groove, the size of the groove is larger than the size of the copper block, preferably, the size of the groove is 0.1-0.5mm larger than the size of the copper block;
[0032] (2) Carry out browning treatment to base material and copper block surface;
[0033] (3) affix protective film on both sides of base material and single side of copper block, described protective film is preferably high-temperature protective film, and the protective film of groove position on the base material is cut off, and groove is hollowed out;
[0034] (4) Use dispensing equipment to fill the pre-prepared resin to the four sides of the groove, the filling widt...
PUM
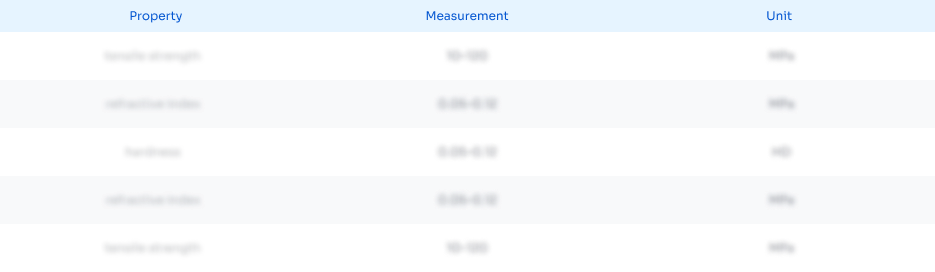
Abstract
Description
Claims
Application Information

- R&D
- Intellectual Property
- Life Sciences
- Materials
- Tech Scout
- Unparalleled Data Quality
- Higher Quality Content
- 60% Fewer Hallucinations
Browse by: Latest US Patents, China's latest patents, Technical Efficacy Thesaurus, Application Domain, Technology Topic, Popular Technical Reports.
© 2025 PatSnap. All rights reserved.Legal|Privacy policy|Modern Slavery Act Transparency Statement|Sitemap|About US| Contact US: help@patsnap.com