Fiber reinforced concrete and preparation method thereof
A fiber-reinforced concrete technology, applied in the field of concrete, can solve problems such as structural damage, functional degradation, social loss, etc., and achieve the effects of improving impermeability, prolonging service life, and improving mechanical properties
- Summary
- Abstract
- Description
- Claims
- Application Information
AI Technical Summary
Problems solved by technology
Method used
Examples
Embodiment 1
[0032] (1) 5 parts of ultra-short glass fiber, 75 parts of polyvinyl chloride chips, 0.5 parts of inorganic ceramic powder, 0.5 parts of coupling agent γ-aminopropyltriethoxysilane, and 0.5 parts of lubricant ethylene bisstearic acid amide The parts are mixed evenly to obtain the premix; after the premix is heated and melted, it is introduced into the spinning box and heated at a high pressure of 150kg / cm 2 Extruded from a porous spinneret, then stretched through 40 times the spinneret holes for multiple times, and then cut into PVC modified glass fibers with a length of 3-5mm;
[0033] (2) 500 parts of Portland cement, 800 parts of fly ash, 200 parts of sand and 250 parts of water are stirred and mixed into cement slurry;
[0034] (3) After mixing 50 parts of polyvinyl chloride modified glass fiber and cement slurry, add 20 parts of water reducing agent and 70 parts of nano-kaolin and continue mixing evenly to obtain fiber reinforced concrete.
Embodiment 2
[0036] (1) 25 parts of ultra-short glass fiber, 95 parts of polyvinyl chloride chips, 3 parts of inorganic ceramic powder, 3 parts of coupling agent γ-(2,3-glycidyloxy) propyltrimethoxysilane, lubricant 1 part of ethylene bis stearamide is mixed uniformly to obtain a premix; after the premix is heated and melted, it is introduced into the spinning box at a high pressure of 200kg / cm 2 Extruded from a porous spinneret, then stretched through 60 times of spinneret holes for multiple times, and then cut into PVC modified glass fibers with a length of 3-5mm;
[0037] (2) 600 parts of Portland cement, 800 parts of fly ash, 300 parts of sand and 300 parts of water are stirred and mixed into cement slurry;
[0038] (3) After mixing 80 parts of polyvinyl chloride modified glass fiber and cement slurry, add 30 parts of water reducer and 50 parts of nano silicon dioxide and continue to mix evenly to obtain fiber reinforced concrete.
Embodiment 3
[0040] (1) 15 parts of ultra-short glass fiber, 85 parts of polyvinyl chloride chips, 2 parts of inorganic ceramic powder, 1 part of coupling agent γ-(2,3-glycidyloxy) propyltrimethoxysilane, lubricant 0.8 parts of pentaerythritol stearate are mixed uniformly to obtain a premix; after the premix is heated and melted, it is introduced into the spinning box at a high pressure of 180kg / cm 2 Extruded from a porous spinneret, then stretched through 50 times the spinneret holes for multiple times, and then cut into PVC modified glass fibers with a length of 3-5mm;
[0041] (2) 550 parts of Portland cement, 700 parts of fly ash, 250 parts of sand and 280 parts of water are stirred and mixed into cement slurry;
[0042] (3) After mixing 60 parts of polyvinyl chloride modified glass fiber and cement slurry, add 25 parts of water reducer and 60 parts of nano-diatomaceous earth and continue mixing evenly to obtain fiber reinforced concrete.
PUM
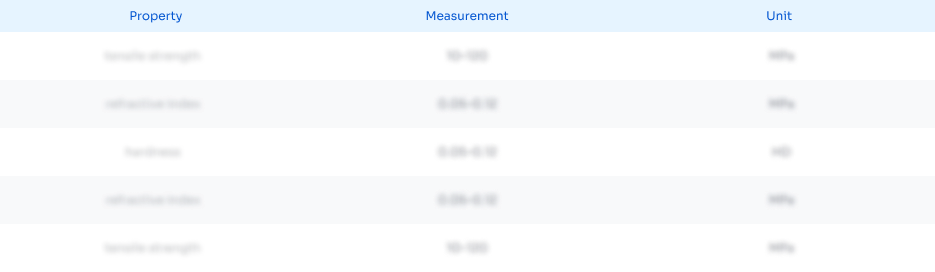
Abstract
Description
Claims
Application Information

- R&D
- Intellectual Property
- Life Sciences
- Materials
- Tech Scout
- Unparalleled Data Quality
- Higher Quality Content
- 60% Fewer Hallucinations
Browse by: Latest US Patents, China's latest patents, Technical Efficacy Thesaurus, Application Domain, Technology Topic, Popular Technical Reports.
© 2025 PatSnap. All rights reserved.Legal|Privacy policy|Modern Slavery Act Transparency Statement|Sitemap|About US| Contact US: help@patsnap.com