Method for treating waste gas in ethyl nitrite production process
A technology of ethyl nitrite and treatment method, which is applied in the field of waste gas treatment in the process of ethyl nitrite generation, can solve the problems of inability to achieve absorption effect, low proportion of ethyl nitrite, harsh reaction conditions, etc., and achieve good economic benefits and social benefits, environmental protection, mild reaction conditions
- Summary
- Abstract
- Description
- Claims
- Application Information
AI Technical Summary
Problems solved by technology
Method used
Image
Examples
Embodiment 1
[0037] Mix 51g (0.51mol) 98% concentrated sulfuric acid and pure water into a 50% sulfuric acid solution. The obtained sulfuric acid solution is dropped into 69.7g (1.0mol) 99% sodium nitrite aqueous solution under stirring, and the reaction temperature is controlled at 25-40℃ , About two hours after dropping sulfuric acid. Pass the generated gas through the air supply bottle connected to the air pump, which is the air supply oxidation device. The red-brown gas after the air supply is passed into a two-stage absorption bottle with an absorption liquid temperature of 40℃. The composition of the two-stage absorption liquid is 300g ( 5mol) urea+588.7g (1.5mol) 31% hydrochloric acid+5g ammonium nitrate+606.3g water is a 20% urea acid solution. All waste gas was collected and analyzed by spectrophotometry with naphthalene ethylene diamine hydrochloride, and the conversion rate of nitrogen oxides reached 99.7%.
Embodiment 2
[0039] Add 75g (1mol) ethyl nitrite into 150g of 80% ethanol aqueous solution, heat it in a water bath at 35°C for 1 hour, increase the temperature of the water bath to 50°C and heat it for another hour, and pass the produced ethyl nitrite gas directly into the absorption liquid without condensation. It is a two-stage absorption bottle at 40℃. The composition of the two-stage absorption liquid is 300g (5mol) urea + 588.7g (1.5mol) 31% hydrochloric acid + 5g ammonium nitrate + 606.3g water to form a 20% urea acidic solution. Absorbed by absolute ethanol at 5°C. After the reaction, gas chromatography was used to detect the absolute ethanol that absorbed the exhaust gas, and the conversion rate of ethyl nitrite was 99.3%.
Embodiment 3
[0041] Mix 51g (0.51mol) 98% concentrated sulfuric acid and pure water into a 50% sulfuric acid solution, and the resulting sulfuric acid solution is dripped with 69.7g (1.0mol) 99% sodium nitrite + 46.9g 99% ethanol (1.01mol) + 150g while stirring In the mixed solution composed of pure water, the reaction temperature is controlled at 25-40°C, and the sulfuric acid is dropped in about two hours. The gas produced is first collected by the refrigerant at -5°C to collect most of the ethyl nitrite, and then the uncondensed gas is passed through the gas cylinder connected to the air pump. The reddish-brown gas after the gas supply is passed into the two-stage absorption bottle. The composition of the grade absorption liquid is a 20% urea acidic solution made up of 300g (5mol) urea+588.7g (1.5mol) 31% hydrochloric acid+5g ammonium nitrate+606.3g water. The exhaust gas was first absorbed by absolute ethanol at -5°C, and all that could not be absorbed was collected and analyzed by the ...
PUM
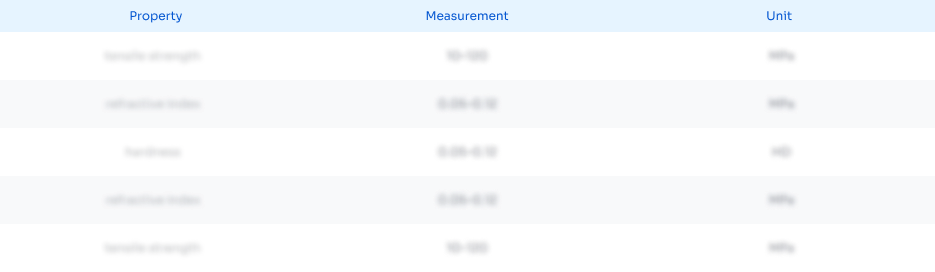
Abstract
Description
Claims
Application Information

- R&D Engineer
- R&D Manager
- IP Professional
- Industry Leading Data Capabilities
- Powerful AI technology
- Patent DNA Extraction
Browse by: Latest US Patents, China's latest patents, Technical Efficacy Thesaurus, Application Domain, Technology Topic, Popular Technical Reports.
© 2024 PatSnap. All rights reserved.Legal|Privacy policy|Modern Slavery Act Transparency Statement|Sitemap|About US| Contact US: help@patsnap.com