Method for recovering waste secondary battery iron
A secondary battery and recycling method technology, applied in battery recycling, waste collector recycling, recycling technology, etc., can solve the problems of a large amount of impurities, low iron recovery efficiency, poor battery crushing effect, etc., to achieve complete separation and recycling The effect of high efficiency and improved crushing efficiency
- Summary
- Abstract
- Description
- Claims
- Application Information
AI Technical Summary
Problems solved by technology
Method used
Image
Examples
Embodiment 1
[0029] A kind of recycling method of waste secondary battery iron, such as figure 1 As shown, it specifically includes the following steps:
[0030] a. Put the waste Ni-MH battery into the tank filled with electrolyte, so that the residual power in the waste Ni-MH battery is fully discharged;
[0031] b. Evenly send the discharged waste nickel-hydrogen batteries into the combustion chamber of the rotary kiln for roasting, the roasting temperature is 700°C, and the roasting time is 2.5 hours, and the easily decomposed organic solvents and electrolytes in the waste nickel-hydrogen batteries are heated, decomposed and released;
[0032] c. Preliminarily cut the roasted waste Ni-MH batteries with a vertical crusher, cut the waste Ni-MH batteries, and then use a double-shaft shredder for in-depth impact treatment to completely tear the waste Ni-MH batteries crushed, and then crushed with an energy-saving ball mill to crush and separate the different substances;
[0033] d. Sieve ...
Embodiment 2
[0038] A kind of recycling method of waste secondary battery iron, such as figure 1 As shown, it specifically includes the following steps:
[0039] a. Put the waste lithium battery into the tank filled with electrolyte, so that the residual power in the waste lithium battery is fully discharged;
[0040] b. Evenly send the discharged waste lithium batteries into the combustion chamber of the rotary kiln for roasting, the roasting temperature is 900°C, and the roasting time is 1.5 hours, and the easily decomposed organic solvents and electrolytes in the waste lithium batteries are decomposed and released by heating;
[0041] c. Preliminarily cut the roasted waste lithium battery with a vertical crusher, cut the waste lithium battery, and then use a double-shaft shredder for in-depth impact treatment to completely shred the waste lithium battery, and then , and then crushed with an energy-saving ball mill to crush and separate the different substances;
[0042] d. Sieve the p...
Embodiment 3
[0047] A kind of recycling method of waste secondary battery iron, such as figure 1 As shown, it specifically includes the following steps:
[0048] a. Put the waste lithium battery into the tank filled with electrolyte, so that the residual power in the waste lithium battery is fully discharged;
[0049] b. Evenly send the discharged waste lithium batteries into the combustion chamber of the rotary kiln for roasting, the roasting temperature is 800°C, and the roasting time is 2 hours, and the easily decomposed organic solvents and electrolytes in the waste lithium batteries are decomposed and released by heating;
[0050] c. Preliminarily cut the roasted waste lithium battery with a vertical crusher, cut the waste lithium battery, and then use a double-shaft shredder for in-depth impact treatment to completely shred the waste lithium battery, and then , and then crushed with an energy-saving ball mill to crush and separate the different substances;
[0051] d. Sieve the pul...
PUM
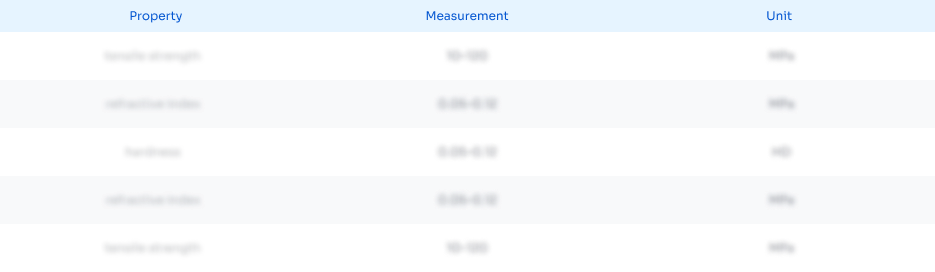
Abstract
Description
Claims
Application Information

- R&D
- Intellectual Property
- Life Sciences
- Materials
- Tech Scout
- Unparalleled Data Quality
- Higher Quality Content
- 60% Fewer Hallucinations
Browse by: Latest US Patents, China's latest patents, Technical Efficacy Thesaurus, Application Domain, Technology Topic, Popular Technical Reports.
© 2025 PatSnap. All rights reserved.Legal|Privacy policy|Modern Slavery Act Transparency Statement|Sitemap|About US| Contact US: help@patsnap.com