A method for wet separation and recovery of valuable metals in Kaldor furnace smelting slag
A technology for wet separation and valuable metals, applied in the direction of non-metallic elements, chemical instruments and methods, process efficiency improvement, etc., can solve the problem of large amount of smelting slag, affecting copper smelting system and copper electrolysis system, without considering antimony and bismuth Selenium and tellurium recovery issues and other issues, to achieve high enrichment, good compatibility, and avoid adverse effects
- Summary
- Abstract
- Description
- Claims
- Application Information
AI Technical Summary
Problems solved by technology
Method used
Image
Examples
Embodiment 1
[0021] A method for wet separation and recovery of valuable metals in Kaldor furnace smelting slag is carried out according to the following steps:
[0022] (1) Sampling and crushing
[0023] A total of 8kg of Kaldor furnace smelting slag in the comprehensive workshop of Baiyin Nonferrous Metals Group Corporation was used for small-scale test. All the Kaldor furnace smelting slag samples obtained were crushed into small particles with a particle size of 0-5mm for use. The raw material composition and content of Kaldor furnace smelting slag are: Pb 28.89%; S 3.58%; Na 10.48%; Ba 7.20%; Cu 12.39%; Sb 10.18%; Bi 6.47%; Ag4.82%; As 1.71%; Si 1.57%; Ca 0.72%; Mg 0.78%; Sn 1.14%; K 0.57%; Fe 1.55%; Cl 0.45%; Al 0.26%; Te 0.20%; Se 0.32%; Ni 0.29%.
[0024] (2) Grinding and water leaching desalination
[0025] Weigh 500g of the broken sample into a ball mill, add 500g of water, and grind for 10 minutes. At this time, the mineral fineness is -200 mesh and 95%. Then rinse with 500g of water a...
Embodiment 2
[0035] (1) The smelting slag of Kaldor furnace in the comprehensive workshop of Baiyin Nonferrous Metals Group Corporation is used for small-scale test. The raw material composition and content are the same as in Example 1.
[0036] (2) Weigh 150g of the broken sample into a ball mill, add 150g of water, and grind for 10 minutes. At this time, the mineral fineness is -200 mesh, which is 98%.
[0037] (3) Pressure acid leaching to remove copper
[0038] Weigh 100g of the ground desalinated material into a 1L small autoclave, add 400g of water, and 20g of 98% concentrated sulfuric acid. After the addition is complete, close the autoclave, turn on stirring and electric heating, and raise the temperature to 120°C. Stop heating, control a certain pressure at this time, and release part of the pressure in the kettle to remove nitrogen. Then close the valve and pass oxygen into the autoclave for 5 hours. After the pressure in the autoclave reaches 12MPa and the temperature in the autoclave...
Embodiment 3
[0046] (1) The smelting slag of Kaldor furnace in the comprehensive workshop of Baiyin Nonferrous Metals Group Corporation was used for small-scale test. The raw material composition and content were the same as in Example 1.
[0047] (2) Weigh 150g of the crushed sample into a ball mill, add 150g of water, and grind for 10 minutes. At this time, the mineral fineness is -200 mesh and 98%.
[0048] (3) Pressure acid leaching to remove copper
[0049] Weigh 100g of the ground desalinated material into a 1L small autoclave, add 400g of water, and 50g of 98% concentrated sulfuric acid. After the addition is complete, close the autoclave, turn on stirring and electric heating, and raise the temperature to 180°C. Stop heating, control a certain pressure at this time, and release part of the pressure in the kettle to remove nitrogen. Then close the valve and pass oxygen into the autoclave for 6 hours. After the pressure in the autoclave reaches 10MPa and the temperature in the autoclave re...
PUM
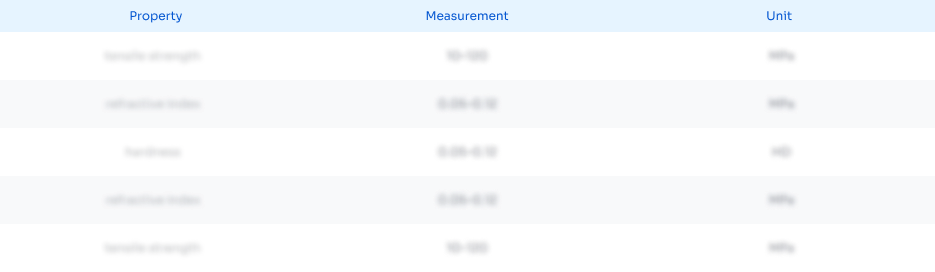
Abstract
Description
Claims
Application Information

- R&D
- Intellectual Property
- Life Sciences
- Materials
- Tech Scout
- Unparalleled Data Quality
- Higher Quality Content
- 60% Fewer Hallucinations
Browse by: Latest US Patents, China's latest patents, Technical Efficacy Thesaurus, Application Domain, Technology Topic, Popular Technical Reports.
© 2025 PatSnap. All rights reserved.Legal|Privacy policy|Modern Slavery Act Transparency Statement|Sitemap|About US| Contact US: help@patsnap.com