Method for preparing shrinkage reducing agent with water reducing performance
A technology of shrinkage reducing agent and performance, applied in the field of preparation of shrinkage reducing agent, can solve the problem of low water reducing rate, achieve good water reducing performance, good freeze-thaw resistance, and low carbonization speed
- Summary
- Abstract
- Description
- Claims
- Application Information
AI Technical Summary
Problems solved by technology
Method used
Image
Examples
preparation example Construction
[0023] The steps of the preparation method of the shrinkage reducing agent with water-reducing properties in the present invention are as follows:
[0024] Put a certain amount of dipropylene glycol monomethyl ether and catalyst into the reactor, heat up to 90-110°C, put in a certain amount of maleic anhydride, and keep it warm for 4-6 hours; then cool it down to 50-60°C and keep it warm. Add a certain amount of water and unsaturated polyoxyethylene ether monomer, stir until completely dissolved; then put a certain amount of oxidant into the reaction kettle, and stir evenly. Add material A made of unsaturated carboxylic acid and water and material B made of chain transfer agent, reducing agent and water; in the process of dropping, add trifluoroethyl methacrylate in batches, A The dropping time of material is 3-4 hours, and the dropping time of material B is 20-40 minutes longer than that of material A; continue to react for 1-2 hours, then cool down to 30--35°C, add to the al...
example 1
[0036] Put 0.51g of dipropylene glycol monomethyl ether and 0.2g of concentrated sulfuric acid into a 500mL four-necked bottle, heat the oil bath to 90°C, add 4.2g of maleic anhydride, turn on the magnetic stirring, and react for 5h; then cool down to 50°C and keep warm , add 84g of water and 89g of methallyl polyoxyethylene ether to it and stir until completely dissolved; then put 1.6g of 30% hydrogen peroxide into it and stir evenly. Then start to drop the A material made of 9.1g acrylic acid and 21g water and the B material made of 0.2g ascorbic acid, 0.32g mercaptoacetic acid, 0.08g ferrous ammonium sulfate and 30g water; Add 0.02g of trifluoroethyl methacrylate in half an hour, the dropping time of material A is 3-4 hours, and the dropping time of material B is 25 minutes longer than that of material A; continue to react for one and a half hours, add water Dilute to a solid content of 40%, and then neutralize with a 32wt% potassium hydroxide solution to a pH of 6-8 to obt...
example 2
[0038]Put 0.37g of dipropylene glycol monomethyl ether and 0.3g of p-toluenesulfonic acid into a 500L four-necked bottle, heat the oil bath to 95°C, put in 2.5g of maleic anhydride, turn on the magnetic stirring, and react for 4 hours; then cool down Keep warm at 55°C, add 84g of water and 89g of propylene polyoxyethylene ether into it and stir until completely dissolved; then add 3.3g of 30% hydrogen peroxide into it and stir evenly. Then start to drop A material made of 8.1g acrylic acid 3.2g methacrylic acid and 19g water and B material made of 0.05g Diabolite block, 0.31g mercaptopropionic acid, 0.08g mercaptoethanol and 30g water; During the addition process, add 0.17g of trifluoroethyl methacrylate every half hour, the dropping time of material A is 3-4 hours, and the dropping time of material B is 25 minutes longer than that of material A; continue React for one and a half hours, add water to dilute to a solid content of 40%, and add 32 wt% potassium hydroxide solution ...
PUM
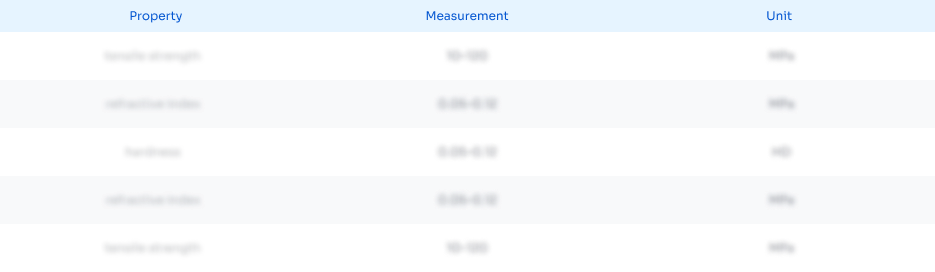
Abstract
Description
Claims
Application Information

- R&D
- Intellectual Property
- Life Sciences
- Materials
- Tech Scout
- Unparalleled Data Quality
- Higher Quality Content
- 60% Fewer Hallucinations
Browse by: Latest US Patents, China's latest patents, Technical Efficacy Thesaurus, Application Domain, Technology Topic, Popular Technical Reports.
© 2025 PatSnap. All rights reserved.Legal|Privacy policy|Modern Slavery Act Transparency Statement|Sitemap|About US| Contact US: help@patsnap.com