A kind of beneficiation method for separating molybdenum tungsten oxide and molybdenum sulfide ore in molybdenum tungsten ore
A beneficiation method and molybdenum oxide technology, applied in chemical instruments and methods, magnetic separation, solid separation, etc., can solve the problems of unfriendly environment, high processing cost, poor separation effect, etc., to simplify the flotation process, reduce The effect of simple production cost and beneficiation process
- Summary
- Abstract
- Description
- Claims
- Application Information
AI Technical Summary
Problems solved by technology
Method used
Image
Examples
Embodiment 1
[0045] The present embodiment selects the high skarn mixed ore as the ore dressing raw material, wherein the percentage of skarn is 65%, the percentage of porphyry is 35%, and the grade of molybdenum in the raw ore is 0.11%, WO 3 The grade of TFe is 0.21%, and the content of TFe is 6.87%.
[0046] The high skarn mixed ore is roughly crushed in a primary crusher (gyratory crusher or jaw crusher) to obtain molybdenum-tungsten ore dressing raw materials, wherein the crushing particle size is 50mm. The molybdenum and tungsten ore raw materials after the coarse crushing step are sieved in a screening equipment (self-centering sieve or circular vibrating sieve) with a sieving particle size of 10 mm. Then, the underscreen product of one stage of sieving step is subjected to two magnetic separation treatments.
[0047] The on-screen product after a stage of sieving step is carried out in the medium crushing crusher (cone crusher, compound crusher or jaw crusher) for medium crushing, ...
Embodiment 2
[0056] This embodiment selects molybdenum-tungsten ore containing low iron as the ore dressing raw material, and mainly porphyry, wherein the percentage of skarn is 23%, the percentage of porphyry is 77%, and the grade of molybdenum in the raw ore is 0.25%, WO 3 The grade is 0.08%, and the content of TFe is 3.17%.
[0057] The molybdenum-tungsten ore containing low iron is roughly crushed in a primary crusher (gyratory crusher or jaw crusher) to obtain molybdenum-tungsten ore dressing raw materials, wherein the crushing particle size is 70mm. The molybdenum and tungsten ore raw materials after the rough crushing step are screened in a screening equipment (self-centered sieve or circular vibrating sieve) with a sieving particle size of 15 mm. Then, the underscreen product of one stage of sieving step is subjected to two magnetic separation treatments.
[0058] The on-screen product after a stage of sieving is carried out in a secondary crushing machine (cone crusher, compound...
Embodiment 3
[0068] The present embodiment selects the mixed ore of skarn and porphyry with high iron content, wherein the percentage of skarn is 55%, the percentage of porphyry is 45%, and the grade of molybdenum in the raw ore is 0.17%, WO 3 The grade of TFe is 0.11%, and the content of TFe is 5.08%.
[0069] The skarn and porphyry mixed ore with high iron content is roughly crushed in a primary crusher (gyratory crusher or jaw crusher) to obtain molybdenum and tungsten ore dressing raw materials, wherein the crushing particle size is 120mm. The molybdenum and tungsten ore raw materials after the coarse crushing step are sieved in a screening equipment (self-centered sieve or circular vibrating sieve) with a sieving particle size of 25 mm. Then, at least two magnetic separation treatments are performed on the undersized product of a screening step, which may be three times, four times or more times.
[0070] The on-screen product after a stage of sieving step is carried out in the inter...
PUM
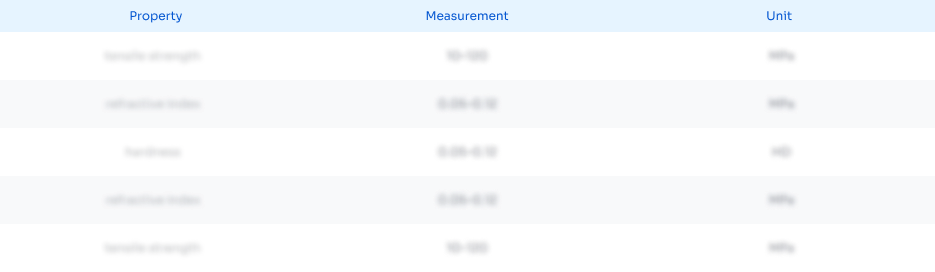
Abstract
Description
Claims
Application Information

- R&D Engineer
- R&D Manager
- IP Professional
- Industry Leading Data Capabilities
- Powerful AI technology
- Patent DNA Extraction
Browse by: Latest US Patents, China's latest patents, Technical Efficacy Thesaurus, Application Domain, Technology Topic, Popular Technical Reports.
© 2024 PatSnap. All rights reserved.Legal|Privacy policy|Modern Slavery Act Transparency Statement|Sitemap|About US| Contact US: help@patsnap.com