C/C-SiC composite material, and preparation method and application thereof
A technology of composite materials and prefabricated parts, applied in chemical instruments and methods, other chemical processes, etc., can solve the problems of not meeting the requirements of high-energy load brakes, reducing the friction stability of materials, and reducing the thermal conductivity of composite materials. Thermal conductivity and mechanical properties, improving friction stability, and the effect of improving friction stability
- Summary
- Abstract
- Description
- Claims
- Application Information
AI Technical Summary
Problems solved by technology
Method used
Image
Examples
Embodiment 1
[0044] A C / C-SiC composite material of the present invention, comprising a carbon fiber preform, a carbon matrix and a silicon carbide matrix introduced successively, the carbon matrix and the silicon carbide matrix are evenly filled in the pores of the carbon fiber preform, and the silicon carbide matrix includes a first A silicon carbide substrate and a second silicon carbide substrate, the second silicon carbide substrate is introduced by a vapor phase siliconizing and sintering process.
[0045] In this embodiment, the C / C-SiC composite material does not contain residual silicon.
[0046] In this embodiment, the first silicon carbide matrix is introduced by a chemical vapor infiltration process.
[0047] In this embodiment, in the C / C-SiC composite material, the volume fraction of the carbon matrix is 37%, the volume fraction of the first silicon carbide matrix is 10%, and the volume fraction of the second silicon carbide matrix is 20%, The porosity is 3%.
[004...
Embodiment 2
[0055] A C / C-SiC composite material of the present invention, comprising a carbon fiber preform, a carbon matrix and a silicon carbide matrix introduced successively, the carbon matrix and the silicon carbide matrix are evenly filled in the pores of the carbon fiber preform, and the silicon carbide matrix includes a first A silicon carbide substrate and a second silicon carbide substrate, the second silicon carbide substrate is introduced by a vapor phase siliconizing and sintering process.
[0056] In this embodiment, the C / C-SiC composite material does not contain residual silicon.
[0057] In this embodiment, the first silicon carbide matrix is introduced by a chemical vapor infiltration process.
[0058] In this embodiment, in the C / C-SiC composite material, the volume fraction of the carbon matrix is 23%, the volume fraction of the first silicon carbide matrix is 25%, and the volume fraction of the second silicon carbide matrix is 15%, The porosity is 2%.
[005...
Embodiment 3
[0066] A C / C-SiC composite material of the present invention, comprising a carbon fiber preform, a carbon matrix and a silicon carbide matrix introduced successively, the carbon matrix and the silicon carbide matrix are evenly filled in the pores of the carbon fiber preform, and the silicon carbide matrix includes a first A silicon carbide substrate and a second silicon carbide substrate, the second silicon carbide substrate is introduced by a vapor phase siliconizing and sintering process.
[0067] In this embodiment, the C / C-SiC composite material does not contain residual silicon.
[0068] In this embodiment, the first silicon carbide matrix is introduced by a chemical vapor infiltration process.
[0069] In this embodiment, in the C / C-SiC composite material, the volume fraction of the carbon matrix is 25%, the volume fraction of the first silicon carbide matrix is 17%, and the volume fraction of the second silicon carbide matrix is 25%, The porosity is 0%.
[007...
PUM
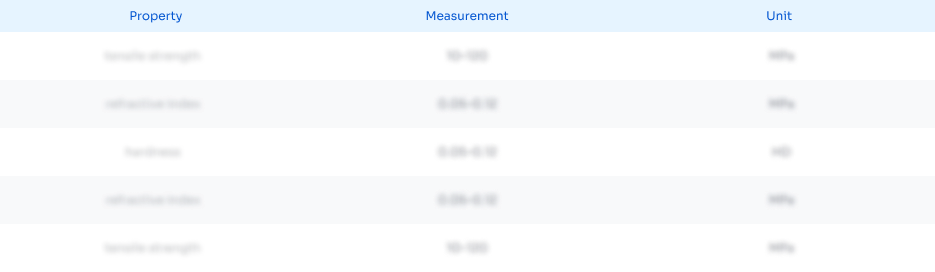
Abstract
Description
Claims
Application Information

- Generate Ideas
- Intellectual Property
- Life Sciences
- Materials
- Tech Scout
- Unparalleled Data Quality
- Higher Quality Content
- 60% Fewer Hallucinations
Browse by: Latest US Patents, China's latest patents, Technical Efficacy Thesaurus, Application Domain, Technology Topic, Popular Technical Reports.
© 2025 PatSnap. All rights reserved.Legal|Privacy policy|Modern Slavery Act Transparency Statement|Sitemap|About US| Contact US: help@patsnap.com