A method for synthesizing a spherical max phase powder material whose main phase is ti2alc
A powder material and main phase technology, which is applied in the field of synthesizing spherical MAX phase powder materials whose main phase is Ti2AlC, can solve the problem that the electrochemical and other activities of the powder are not high enough, the particle size and shape are difficult to accurately control, and it is easy to introduce other materials. Impurities and other problems, to achieve the effect of convenient large-scale production, simplified powder preparation process, and good fluidity
- Summary
- Abstract
- Description
- Claims
- Application Information
AI Technical Summary
Problems solved by technology
Method used
Image
Examples
Embodiment 1
[0035] TiH 2 , Al, TiC powder raw materials are n(TiH 2 ):n(Al):n(TiC)=1:1.1:1 ratio ingredients. Ti H 2 The average particle size of powder is 800nm, the purity is 99.9wt%, the average particle size of Al powder is 1 micron, the purity is 99.9wt%, the average particle size of TiC is 800nm, the purity is 99.5wt%. Such as Figure 4 As shown in the particle size distribution of the raw material powder, the powder contains many components with different particle sizes and thus presents a bimodal distribution.
[0036] Add 1.5Kg of absolute ethanol to the evenly mixed powder, and put it into a 3L beaker. Place the beaker in a high-power ultrasonic cleaning machine for dispersion and stir with a stirrer at the same time, the stirring speed is 250r / min, and the time is 30min. The slurry is spray-dried with an organic solvent-based laboratory spray dryer with an inert gas closed cycle function, using a two-fluid nozzle with a nozzle diameter of 2mm, the air inlet temperature is ...
Embodiment 2
[0038] TiH 2 , Al, TiC powder raw materials are n(TiH 2 ):n(Al):n(TiC)=1:1.1:1 ratio ingredients. Ti H 2 The average particle size of powder is 800nm, the purity is 99.9wt%, the average particle size of Al powder is 1 micron, the purity is 99.9wt%, the average particle size of TiC is 800nm, the purity is 99.5wt%, the total raw material is 1Kg, and it is mixed with a mixer for 30 minutes. Add 1.5Kg of absolute ethanol to the uniformly mixed powder, and put it into a 5L stirring ball mill for ball milling for 30 minutes. Place the beaker in a high-power ultrasonic cleaning machine for dispersion and stir with a stirrer at the same time, the stirring speed is 250r / min, and the time is 30min. Dry the slurry with a centrifugal atomizing dryer with a closed-cycle function. A centrifugal atomizing nozzle is used. The diameter of the atomizing disc is 50mm. The atomizer speed is 20000r / min. Peristaltic pump speed 30r / min, heating power 9KW. The dried powder was placed in an alumi...
Embodiment 3
[0040] TiH 2 , Al, TiC powder raw materials are n(TiH 2 ):n(Al):n(TiC)=1:1.1:1 ratio ingredients. Ti H 2 The average particle size of powder is 800nm, the purity is 99.9wt%, the average particle size of Al powder is 1 micron, the purity is 99.9wt%, the average particle size of TiC is 800nm, the purity is 99.5wt%, the total raw material is 3Kg, and it is mixed with a mixer for 30min. Add 4.5Kg of absolute ethanol to the uniformly mixed powder, and put it into a 10L vibratory ball milling device with a vibration frequency of 50 Hz, an amplitude of 5 mm, and a ball milling time of 30 minutes. Pour out the ball-milled slurry and put it into a 10L beaker while stirring with a stirrer at a stirring speed of 250r / min for 30min. The slurry is dried with a large centrifugal atomization dryer with a closed cycle function, a centrifugal atomization nozzle is used, the diameter of the atomization disc is 120mm, and the rotation speed of the atomizer is 15000r / min. The air inlet temper...
PUM
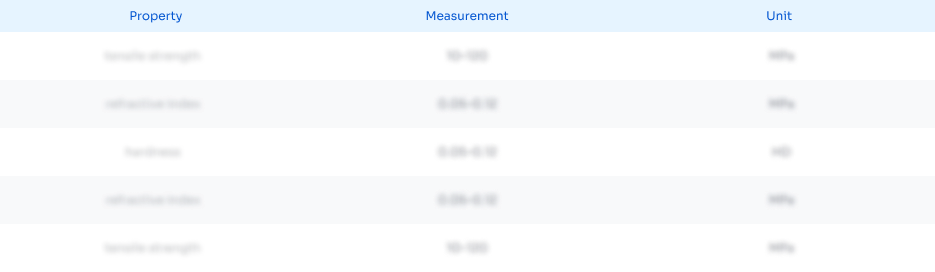
Abstract
Description
Claims
Application Information

- R&D
- Intellectual Property
- Life Sciences
- Materials
- Tech Scout
- Unparalleled Data Quality
- Higher Quality Content
- 60% Fewer Hallucinations
Browse by: Latest US Patents, China's latest patents, Technical Efficacy Thesaurus, Application Domain, Technology Topic, Popular Technical Reports.
© 2025 PatSnap. All rights reserved.Legal|Privacy policy|Modern Slavery Act Transparency Statement|Sitemap|About US| Contact US: help@patsnap.com