Hole-creating corrosion method for controlling length and consistency of aluminium foil tunnel hole
A consistent, tunneling technology, applied in capacitors, circuits, electrical components, etc., can solve the problems of uneven length of tunnel holes, low production efficiency of single-V corrosion in aluminum foil industry, hindering the improvement of specific capacitance of aluminum foil, etc., to improve production efficiency. , the effect of increasing the specific capacitance
- Summary
- Abstract
- Description
- Claims
- Application Information
AI Technical Summary
Problems solved by technology
Method used
Image
Examples
Embodiment 1
[0029] The technological process of the on-off current waveform corrosion method for controlling the length and consistency of aluminum foil tunnel holes of the present invention includes: pretreatment, on-off attenuation current waveform hole corrosion, hole expansion corrosion, post-treatment and other steps. details as follows:
[0030] (1) Pretreatment: Soak an aluminum foil with a purity of 99.99%, a thickness of 120 μm, and a cubic texture occupancy of more than 95% in a mixed solution of 1M HCl+3.5M H2SO4 at a temperature of 80°C for 120s.
[0031](2) On-off decay current waveform porosity corrosion: When the required aluminum foil tunnel hole length is approximately 30 μm, place the pretreated aluminum foil in 0.8N HCl+0.8N A13++7.2N H2SO4 at a temperature of 72°C In the mixed solution, according to the basic growth curve and passivation current density of the tunnel hole in the pitting corrosion system at this temperature, an on-off parabolic decay current waveform is...
Embodiment 2
[0038] The difference from Example 1 is that in the on-off decaying current waveform porosity corrosion step of this example, when the required length of the aluminum foil tunnel hole is approximately 40 μm, the pretreated aluminum foil is placed in a 0.8N at a temperature of 72°C In the mixed solution of HCl+0.8N Al3++7.2N H2SO4, according to the basic growth curve and passivation current density of the tunnel hole in the pitting corrosion system at this temperature, the channel to control the length of the tunnel hole and improve the length consistency can be obtained. Broken parabolic decay current waveform. The number of on-off waveforms is 6, and the initial current density i0 is 600mA cm-2. Each power-on time is 15s, each power-off time is 15s, and the final corrosion current density is 50mA cm-2.
Embodiment 3
[0042] The difference from Example 1 is that in the on-off decaying current waveform pitting corrosion step of this example, when the required length of the tunnel hole of the aluminum foil is approximately 45 μm, the pretreated aluminum foil is placed in a 0.8N at a temperature of 72°C In the mixed solution of HCl+0.8N Al3++7.2N H2SO4, according to the basic growth curve and passivation current density of the tunnel hole in the pitting corrosion system at this temperature, the channel to control the length of the tunnel hole and improve the length consistency can be obtained. Broken parabolic decay current waveform. The number of on-off waveforms is 6, and the initial current density i0 is 650mA cm-2. Each power-on time is 20s, each power-off time is 20s, and the final corrosion current density is 50mA cm-2.
PUM
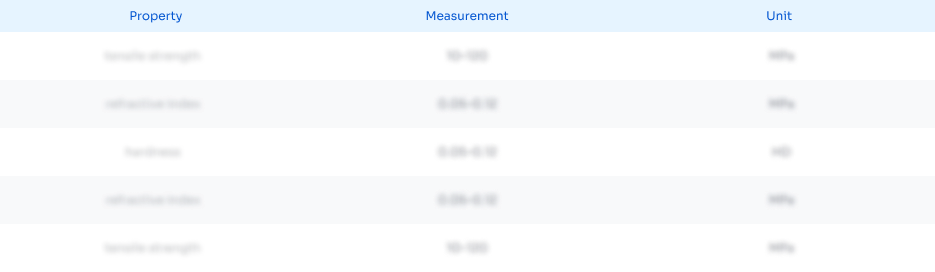
Abstract
Description
Claims
Application Information

- R&D Engineer
- R&D Manager
- IP Professional
- Industry Leading Data Capabilities
- Powerful AI technology
- Patent DNA Extraction
Browse by: Latest US Patents, China's latest patents, Technical Efficacy Thesaurus, Application Domain, Technology Topic, Popular Technical Reports.
© 2024 PatSnap. All rights reserved.Legal|Privacy policy|Modern Slavery Act Transparency Statement|Sitemap|About US| Contact US: help@patsnap.com