Method for preparing chalcopyrite electrode
A chalcopyrite and electrode technology, applied in the direction of material electrochemical variables, measuring devices, instruments, etc., can solve the problems that affect the electrochemical corrosion results of chalcopyrite, poor ductility, chalcopyrite brittleness, etc.
- Summary
- Abstract
- Description
- Claims
- Application Information
AI Technical Summary
Problems solved by technology
Method used
Examples
preparation example Construction
[0030] A kind of preparation method of chalcopyrite electrode, it comprises
[0031] Step 1, select chalcopyrite particles;
[0032] Step 2, cleaning and drying the chalcopyrite particles for subsequent use;
[0033] Step 3. Weigh 0.5-0.7 g of the dried chalcopyrite particles, grind them into a powder of more than 200 meshes, press the chalcopyrite powder into a chalcopyrite cylinder with a pressure of 2 MPa in a powder tablet press and use silver foil wrapping;
[0034] Step 4. Weigh 1.2-1.4g of sodium chloride and grind it into a powder of more than 200 meshes, place the sodium chloride powder in an oven and dry at 150°C for 1-5 hours;
[0035] Step 5, preparing a sodium chloride cylinder containing a chalcopyrite cylinder with the dried sodium chloride powder;
[0036] Step 6, putting the sodium chloride cylinder obtained in step 5 into a high-pressure assembly block, and performing heating and pressure sintering;
[0037] Step 7. After the sintering is completed, the s...
Embodiment example 1
[0054] Break the chalcopyrite-containing rock into 40-60 meshes, select the chalcopyrite particles with a purity of 99%-100% under the binocular lens, ultrasonically clean them with acetone for 10-20 minutes, and then clean them with absolute ethanol. Then place it in an oven at a temperature of 30-60°C for 5-30 minutes and then dry it for later use. Weigh 0.5g-0.7g of chalcopyrite particles, grind it into a powder of more than 200 mesh, press it into a cylinder under the condition of 2MPa in a powder tablet press, and wrap it with silver foil. Weigh 1.2-1.4g of sodium chloride and grind it into a powder of more than 200 mesh, place it in an oven at 150°C for 1-5h, and then dry it for later use. Weigh 0.55-0.65g of sodium chloride, press it into a cylindrical shape in a powder tablet press, then place the chalcopyrite cylinder in the middle of the upper surface of the sodium chloride cylinder, and then pour 0.65-0.75g of sodium chloride Sodium covering, compaction under the c...
Embodiment example 2
[0060] Break the chalcopyrite-containing rock into 40-60 meshes, select the chalcopyrite particles with a purity of 99%-100% under the binocular lens, ultrasonically clean them with acetone for 10-20 minutes, and then clean them with absolute ethanol. Then place it in an oven at a temperature of 30-60°C for 5-30 minutes and then dry it for later use. Weigh 0.5g-0.7g of chalcopyrite particles, grind it into a powder of more than 200 mesh, press it into a cylinder under the condition of 2MPa in a powder tablet press, and wrap it with silver foil. Weigh 1.2-1.4g of sodium chloride and grind it into a powder of more than 200 mesh, place it in an oven at 150°C for 1-5h, and then dry it for later use. Weigh 0.55-0.65g of sodium chloride, press it into a cylindrical shape in a powder tablet machine, then place the chalcopyrite cylinder in the middle of the upper surface of the sodium chloride cylinder, and then pour 0.65-0.75g of sodium chloride Sodium covering, compaction under the...
PUM
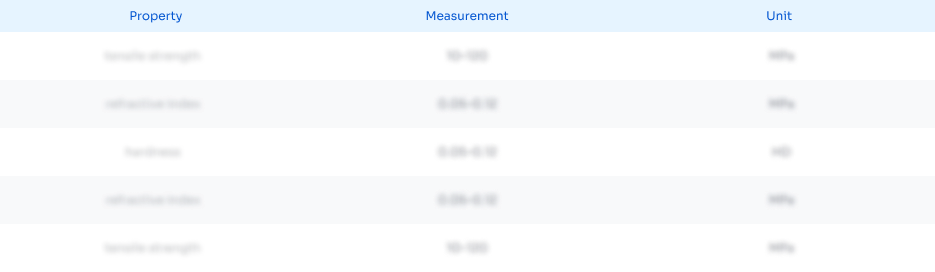
Abstract
Description
Claims
Application Information

- R&D
- Intellectual Property
- Life Sciences
- Materials
- Tech Scout
- Unparalleled Data Quality
- Higher Quality Content
- 60% Fewer Hallucinations
Browse by: Latest US Patents, China's latest patents, Technical Efficacy Thesaurus, Application Domain, Technology Topic, Popular Technical Reports.
© 2025 PatSnap. All rights reserved.Legal|Privacy policy|Modern Slavery Act Transparency Statement|Sitemap|About US| Contact US: help@patsnap.com