High-tensile strength cable protective casing and production method
A high tensile strength, cable protection technology, applied in the direction of insulated cables, cables, circuits, etc., can solve problems such as unsatisfactory, and achieve the effects of high oxygen index, excellent weather resistance, and good flame retardant performance
- Summary
- Abstract
- Description
- Claims
- Application Information
AI Technical Summary
Problems solved by technology
Method used
Examples
Embodiment 1
[0018] A high tensile strength cable sheath tube, which is composed of the following raw materials in parts by weight: 116 parts of acrylonitrile-butadiene-styrene copolymer, 25 parts of polyvinyl chloride, 13 parts of chicken feather hydrolyzed powder, 0.38 parts of sodium pentanesulfonate 7 parts of myristyl stearate, 0.58 parts of γ-aminoethylaminopropyl trimethoxysilane, 5 parts of diethyl azodicarboxylate, 0.14 parts of polypropylene glycol dioxirane methyl ether 0.4 parts of nano-silicon carbide, 0.6 parts of nano-magnesium nitride, 0.2 parts of nano-alumina, 4.2 parts of gum arabic, and 0.8 parts of white carbon black.
[0019] The production method of the sheath tube is as follows:
[0020] Mix the ingredients except gum arabic and white carbon black in proportion, stir at a speed of 900r / min for 10min, and then melt blend at 170°C for 28min to obtain a rubber compound; crosslink the rubber compound at 190°C for 16 minutes , then add gum arabic and white carbon black,...
Embodiment 2
[0023] A high tensile strength cable sheath tube, which is composed of the following raw materials in parts by weight: 110 parts of acrylonitrile-butadiene-styrene copolymer, 22 parts of polyvinyl chloride, 12 parts of chicken feather hydrolyzed powder, and 0.41 parts of sodium pentanesulfonate 6 parts, 6 parts of myristyl stearate, 0.77 parts of γ-aminoethylaminopropyl trimethoxysilane, 4.2 parts of diethyl azodicarboxylate, 0.18 parts of polypropylene glycol dioxirane methyl ether 0.3 parts of nano-silicon carbide, 0.4 parts of nano-magnesium nitride, 0.1 parts of nano-alumina, 4 parts of gum arabic, and 0.5 parts of white carbon black.
[0024] The production method of the sheath tube is as follows:
[0025] Mix the ingredients except gum arabic and white carbon black in proportion, stir at a speed of 900r / min for 10min, and then melt blend at 165-180°C for 25-30min to obtain a rubber compound; put the rubber compound at 180°C-200 After crosslinking at ℃ for 15-18 minutes,...
Embodiment 3
[0028] A high tensile strength cable sheath tube, which is composed of the following raw materials in parts by weight: 108 parts of acrylonitrile-butadiene-styrene copolymer, 28 parts of polyvinyl chloride, 11 parts of chicken feather hydrolyzed powder, and 0.36 parts of sodium pentanesulfonate 9 parts, 9 parts of myristyl stearate, 0.69 parts of γ-aminoethylaminopropyl trimethoxysilane, 3.5 parts of diethyl azodicarboxylate, 0.12 parts of polypropylene glycol dioxirane methyl ether 0.42 parts of nano-silicon carbide, 0.7 parts of nano-magnesium nitride, 0.28 parts of nano-alumina, 5 parts of gum arabic, and 1 part of white carbon black.
[0029] The production method of the sheath tube is as follows:
[0030] Mix the ingredients except gum arabic and white carbon black in proportion, stir at a speed of 950r / min for 10min, and then melt blend at 180°C for 26min to obtain the rubber compound; crosslink the rubber compound at 180°C for 16min, Then add gum arabic and white carbo...
PUM
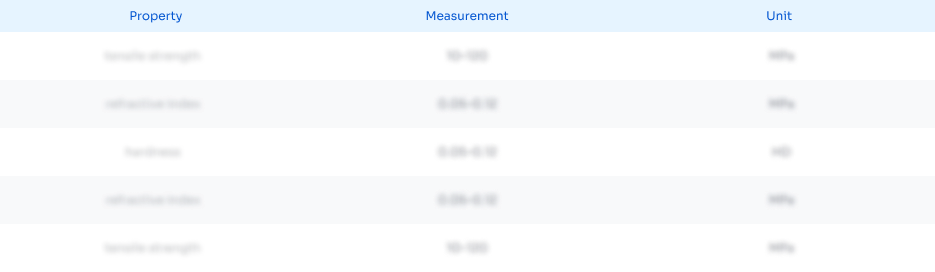
Abstract
Description
Claims
Application Information

- R&D
- Intellectual Property
- Life Sciences
- Materials
- Tech Scout
- Unparalleled Data Quality
- Higher Quality Content
- 60% Fewer Hallucinations
Browse by: Latest US Patents, China's latest patents, Technical Efficacy Thesaurus, Application Domain, Technology Topic, Popular Technical Reports.
© 2025 PatSnap. All rights reserved.Legal|Privacy policy|Modern Slavery Act Transparency Statement|Sitemap|About US| Contact US: help@patsnap.com