Production technology for anti-ultraviolet finishing liquid for elastic worsted fabric
A worsted fabric and anti-ultraviolet technology, which is applied in fiber treatment, textiles and papermaking, and light-resistant fibers, etc., can solve the problems of unsatisfactory film-forming elasticity and flexibility, and maintain anti-ultraviolet performance, good mechanical properties, and fracture The effect of large elongation
- Summary
- Abstract
- Description
- Claims
- Application Information
AI Technical Summary
Problems solved by technology
Method used
Examples
Embodiment 1
[0016] For realizing above-mentioned technical effect, the production technology of elastic worsted fabric anti-ultraviolet finishing solution in embodiment 1 comprises the following steps:
[0017] S1: Prepare wool keratin solution, immerse wool in imidazole-type ionic liquid, heat to 60°C under vacuum, keep stirring until the wool is completely dissolved into a beige liquid;
[0018] S2: preparing a sodium carboxymethyl cellulose solution, stirring and dissolving the sodium carboxymethyl cellulose powder in water at 45°C to prepare a sodium carboxymethyl cellulose solution with a concentration of 0.5% by weight;
[0019] S3: The wool keratin solution obtained in S1 is miscible with water in a ratio of 1:7, and the sodium carboxymethyl cellulose solution obtained in S2 is added. The volume ratio of the sodium carboxymethyl cellulose solution to water is 0.1:1, and then added to the A cross-linking agent is added into the mixed solution to obtain a wool keratin finishing solut...
Embodiment 2
[0024] The difference between embodiment 2 and embodiment 1 is:
[0025] S1: Heating to 80°C under vacuum;
[0026] S2: stirring and dissolving the sodium carboxymethyl cellulose powder in water at 50°C to prepare a sodium carboxymethyl cellulose solution with a concentration of 0.7% by weight;
[0027] S3: The wool keratin solution obtained in S1 is miscible with water at a ratio of 1:10, and the volume ratio of sodium carboxymethyl cellulose solution to water is 0.3:1.
[0028] Imidazole-type ionic liquid is a mixture of 1-butyl-3-methylimidazolium bromide and 1-butyl-3-methylimidazolium tetrafluoroborate. In imidazole-type ionic liquid, 1-butyl-3-methyl The weight ratio of imidazolium bromide is 30%.
[0029] The weight ratio of wool and ionic liquid mixed solution in S2 is 1:15.
[0030] The weight percent concentration of the crosslinking agent in the wool keratin finishing solution is 0.8%.
Embodiment 3
[0032] The difference between embodiment 3 and embodiment 1 is:
[0033] S1: Heating to 70°C under vacuum;
[0034] S2: stirring and dissolving the sodium carboxymethyl cellulose powder in water at 47°C to prepare a sodium carboxymethyl cellulose solution with a concentration of 0.6% by weight;
[0035] S3: The wool keratin solution obtained in S1 is miscible with water at a ratio of 1:8, and the volume ratio of sodium carboxymethylcellulose solution to water is 0.2:1.
[0036] Imidazole-type ionic liquid is a mixture of 1-butyl-3-methylimidazolium bromide and 1-butyl-3-methylimidazolium tetrafluoroborate. In imidazole-type ionic liquid, 1-butyl-3-methyl The weight ratio of imidazolium bromide is 40%.
[0037] The weight ratio of wool and ionic liquid mixed solution in S2 is 1:12.
[0038] The weight percent concentration of the crosslinking agent in the wool keratin finishing solution is 0.7%.
PUM
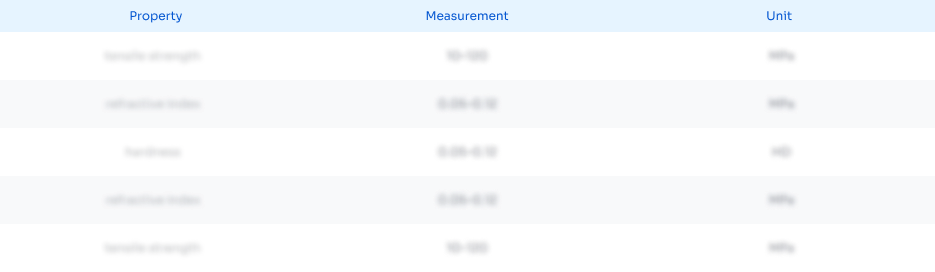
Abstract
Description
Claims
Application Information

- R&D Engineer
- R&D Manager
- IP Professional
- Industry Leading Data Capabilities
- Powerful AI technology
- Patent DNA Extraction
Browse by: Latest US Patents, China's latest patents, Technical Efficacy Thesaurus, Application Domain, Technology Topic, Popular Technical Reports.
© 2024 PatSnap. All rights reserved.Legal|Privacy policy|Modern Slavery Act Transparency Statement|Sitemap|About US| Contact US: help@patsnap.com