Anti-acid and anti-alkali insulating material and production process thereof
An insulating material and anti-acid and alkali technology, which is applied in the field of insulating material preparation, can solve the problems of chemical corrosion and affecting service life, etc., and achieve the effects of long service life, enhanced acid and alkali resistance, and simple production process
- Summary
- Abstract
- Description
- Claims
- Application Information
AI Technical Summary
Problems solved by technology
Method used
Examples
Embodiment 1
[0015] The component ratios used are: nitrile rubber 30 parts, epoxy modified furan resin 18 parts, alkali-resistant glass fiber 20 parts, polyphenylene sulfide fiber 15 parts, basalt fiber 10 parts, phthalocyanine compound 10 parts, nano silicon 10 parts of micropowder, 8 parts of polyvinyl chloride, 8 parts of silicon carbide fine powder, 15 parts of nano-modified epoxy resin, 8 parts of active calcium silicate, 8 parts of trimethylolpropane, 10 parts of zinc dialkyldithiophosphate .
[0016] The production process of this embodiment includes the following steps:
[0017] A. Mix alkali-resistant glass fiber, polyphenylene sulfide fiber, basalt fiber, phthalocyanine compound, nano silicon powder, and polyvinyl chloride and add it to the reactor for heating. The heating temperature is 80℃, the heating time is 30min, and then the temperature is constant. 20min, get A mixture;
[0018] B. Add silicon carbide fine powder, nano-modified epoxy resin, active calcium silicate, trimethylol...
Embodiment 2
[0022] The component ratios used are: nitrile rubber 32 parts, epoxy modified furan resin 20 parts, alkali-resistant glass fiber 25 parts, polyphenylene sulfide fiber 17 parts, basalt fiber 15 parts, phthalocyanine compound 12 parts, nano silicon 12 parts of micro powder, 9 parts of polyvinyl chloride, 9 parts of silicon carbide fine powder, 17 parts of nano-modified epoxy resin, 9 parts of active calcium silicate, 9 parts of trimethylolpropane, 11 parts of zinc dialkyl dithiophosphate .
[0023] The production process of this embodiment includes the following steps:
[0024] A. Mix the alkali-resistant glass fiber, polyphenylene sulfide fiber, basalt fiber, phthalocyanine compound, nano silicon powder, and polyvinyl chloride into the reactor for heating. The heating temperature is 85℃, the heating time is 32min, and then the temperature is constant. 20min, get A mixture;
[0025] B. Add silicon carbide fine powder, nano-modified epoxy resin, active calcium silicate, trimethylolpro...
Embodiment 3
[0029] The component ratios used are: nitrile rubber 40 parts, epoxy modified furan resin 25 parts, alkali-resistant glass fiber 40 parts, polyphenylene sulfide fiber 25 parts, basalt fiber 30 parts, phthalocyanine compound 20 parts, nano silicon 25 parts of micropowder, 15 parts of polyvinyl chloride, 12 parts of silicon carbide fine powder, 25 parts of nano-modified epoxy resin, 17 parts of active calcium silicate, 12 parts of trimethylolpropane, 15 parts of zinc dialkyldithiophosphate .
[0030] The production process of this embodiment includes the following steps:
[0031] A. Mix the alkali-resistant glass fiber, polyphenylene sulfide fiber, basalt fiber, phthalocyanine compound, nano silicon powder, and polyvinyl chloride into the reactor for heating. The heating temperature is 100°C, the heating time is 40 minutes, and then the temperature is constant. 20min, get A mixture;
[0032] B. Add silicon carbide fine powder, nano-modified epoxy resin, active calcium silicate, trime...
PUM
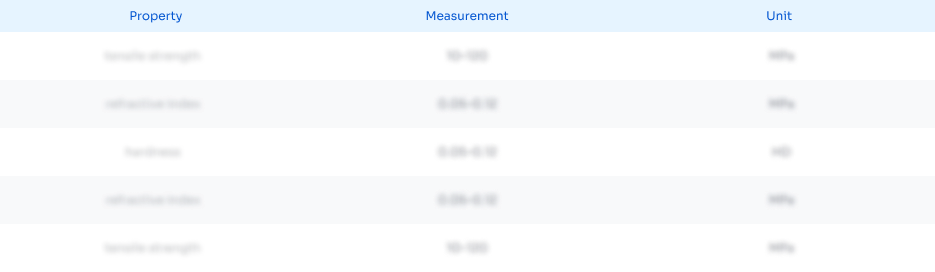
Abstract
Description
Claims
Application Information

- R&D
- Intellectual Property
- Life Sciences
- Materials
- Tech Scout
- Unparalleled Data Quality
- Higher Quality Content
- 60% Fewer Hallucinations
Browse by: Latest US Patents, China's latest patents, Technical Efficacy Thesaurus, Application Domain, Technology Topic, Popular Technical Reports.
© 2025 PatSnap. All rights reserved.Legal|Privacy policy|Modern Slavery Act Transparency Statement|Sitemap|About US| Contact US: help@patsnap.com