Production method of Mn-Cr high-performance gear steel
A gear steel, high-performance technology, applied in the field of alloy steel, can solve the problems of unstable carburized structure of gears, affect the precision and service life of gears, achieve optimal shape and distribution, solve the contradiction of deoxidation and sulfur retention, and optimize the refining process Effect
- Summary
- Abstract
- Description
- Claims
- Application Information
AI Technical Summary
Problems solved by technology
Method used
Examples
Embodiment 1
[0021] The process route of EAF-CONVERTER electric converter smelting→LF furnace refining→VD vacuum treatment→CCM continuous casting is used to produce Mn-Cr series high-performance gear steel.
[0022] Smelting product composition control: C: 0.17~0.22%, Si: 0.15~0.25%, Mn: 1.10~1.40%, Cr: 1.00~1.30%, Mo≤0.08%, B≤0.0005%, Cu≤0.02%, Ni≤ 0.02%, Al: 0.025-0.055%, P: ≤0.015%, S: 0.020-0.035%, N: ≤130ppm.
[0023] The total charge of the electric converter is controlled at 102.2 tons, the molten iron ratio is 90%, the pig iron addition is 3.6 tons, and the rest is high-quality steel scrap. Tapping end point composition C: 0.10%, P: 0.008%, tapping temperature T: 1645°C, tapping volume 86.3 tons; adding 100kg of Al blocks and 50kg of calcium carbide for deoxidation during tapping, adding 780kg of low-carbon ferromanganese and 220kg of low-titanium Ferrosilicon, 1550kg of low-carbon and low-titanium ferrochrome and 375kg of high-carbon ferromanganese are alloyed after the furnace, ...
Embodiment 2
[0029] The process route of EAF-CONVERTER electric converter smelting→LF furnace refining→VD vacuum treatment→CCM continuous casting is used to produce Mn-Cr series high-performance gear steel.
[0030] Smelting product composition control: C: 0.17~0.22%, Si: 0.15~0.25%, Mn: 1.10~1.40%, Cr: 1.00~1.30%, Mo≤0.08%, B≤0.0005%, Cu≤0.02%, Ni≤ 0.02%, Al: 0.025-0.055%, P: ≤0.015%, S: 0.020-0.035%, N: ≤130ppm.
[0031] The total charge of the electric converter is controlled at 103.4 tons, the molten iron ratio is 91%, the pig iron addition is 3.1 tons, and the rest is high-quality steel scrap. Tapping end point composition C: 0.12%, P: 0.0010%, tapping temperature T: 1641°C, tapping volume 86.8 tons; adding 100kg of Al blocks and 50kg of calcium carbide for deoxidation during tapping, adding 800kg of low-carbon ferromanganese and 210kg of low-titanium Ferrosilicon, 1750kg of low-carbon and low-titanium ferrochrome and 350kg of high-carbon ferromanganese are alloyed after the furnace,...
Embodiment 3
[0037] The process route of EAF-CONVERTER electric converter smelting→LF furnace refining→VD vacuum treatment→CCM continuous casting is used to produce Mn-Cr series high-performance gear steel.
[0038] Smelting product composition control: C: 0.17~0.22%, Si: 0.15~0.25%, Mn: 1.10~1.40%, Cr: 1.00~1.30%, Mo≤0.08%, B≤0.0005%, Cu≤0.02%, Ni≤ 0.02%, Al: 0.025-0.055%, P: ≤0.015%, S: 0.020-0.035%, N: ≤130ppm.
[0039] The total charge of the electric converter is controlled at 105.9 tons, the ratio of hot metal to 88%, the amount of pig iron added is 5.6 tons, and the rest is high-quality steel scrap. Tapping end point composition C: 0.08%, P: 0.006%, tapping temperature T: 1650°C, tapping amount 85.6 tons; adding 120kg of Al blocks and 50kg of calcium carbide for deoxidation, adding 700kg of low-carbon ferromanganese and 250kg of low-titanium Ferrosilicon, 1800kg of low-carbon and low-titanium ferrochrome and 500kg of high-carbon ferromanganese are alloyed after the furnace, and 750...
PUM
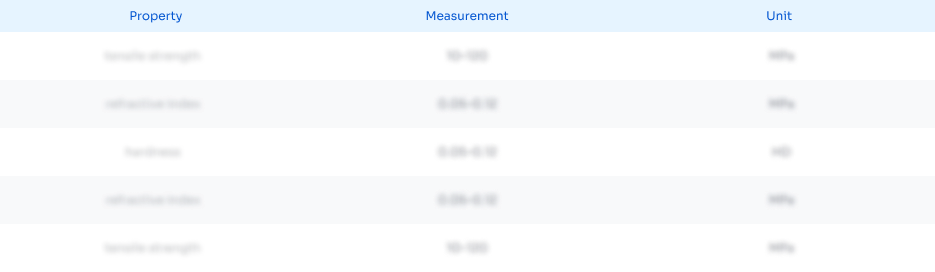
Abstract
Description
Claims
Application Information

- Generate Ideas
- Intellectual Property
- Life Sciences
- Materials
- Tech Scout
- Unparalleled Data Quality
- Higher Quality Content
- 60% Fewer Hallucinations
Browse by: Latest US Patents, China's latest patents, Technical Efficacy Thesaurus, Application Domain, Technology Topic, Popular Technical Reports.
© 2025 PatSnap. All rights reserved.Legal|Privacy policy|Modern Slavery Act Transparency Statement|Sitemap|About US| Contact US: help@patsnap.com