A kind of thermoplastic phosphogypsum filling material and preparation method thereof
A filling material and phosphogypsum technology, which is applied in the deep processing modification and application field of phosphate rock by-products, can solve the problems of restricting the large-scale industrial application of phosphogypsum, difficulty in reflecting the high consumption of phosphogypsum, and the low addition and usage of phosphogypsum. , to avoid the effects of toxic and side effects, excellent flame retardancy and thermal stability, uniform dispersion
- Summary
- Abstract
- Description
- Claims
- Application Information
AI Technical Summary
Problems solved by technology
Method used
Examples
Embodiment 1
[0040] 1) Mix phosphogypsum with 20% free moisture and calcium hydroxide stacked outdoors in a mixer evenly at a mass ratio of 100:5, let it age for 2 days, and then send it to a single-rotor hammer dryer with the temperature set at Under the condition of 200°C, the water vaporized by the dried object is discharged through a dry dust collector, a wet dust collector, and a condenser, and dried for 1 hour to remove volatile matter, free water and part of crystal water to obtain dry powder phosphogypsum;
[0041] 2) The dry powder phosphogypsum obtained in step 1) is cold mixed with inorganic lubricant powder and dispersant at a mass ratio of 100:5:2, and then sent to a vortex jet mill, and the dry powder is made by the high-speed vortex formed by high-speed gas rotation. Phosphogypsum collides with inorganic lubricating powder and dispersant, grinds and refines each other, and inorganic lubricating powder is embedded with phosphogypsum during the refinement process of dry powder ...
Embodiment 2
[0046] 1) Mix phosphogypsum with free moisture of 25% and calcium hydroxide stacked outdoors in a mixer evenly at a mass ratio of 100:3, let it stand for 2 days, and then send it to a rotary dryer with the temperature set at 300°C Under certain conditions, the water vaporized by the dried object is discharged through a dry dust collector, a wet dust collector, and a condenser, and dried for 1 hour to remove volatile matter, free water and part of crystal water to obtain dry powder phosphogypsum;
[0047] 2) Mix the dry phosphogypsum powder obtained in step 1) with inorganic lubricating powder and dispersant in a mass ratio of 100:5:2, and then send it into a fluidized bed jet mill to form a high-speed vortex through high-speed gas rotation. Make the dry powder phosphogypsum collide with the inorganic lubricating powder and dispersant, grind and refine each other, and the inorganic lubricating powder is inlaid with the phosphogypsum through the anchoring group of the dispersant ...
Embodiment 3
[0052] 1) Mix the phosphogypsum powder and calcium hydroxide naturally stacked outdoors evenly at a mass ratio of 100:3, put it in the oven for more than 36 hours, then send it to a stirring dryer, and dry it at 150°C for 2 hours to remove volatile matter and free water and part of crystal water to obtain dry powder phosphogypsum;
[0053] 2) Mix the dry phosphogypsum powder obtained in step 1) with inorganic lubricating powder and dispersant in a mass ratio of 100:4:3, and then send it into the rotary jet jet mill, and use the high-speed vortex formed by high-speed gas rotation to make Dry powder phosphogypsum collides with inorganic lubricating powder and dispersant, grinds and refines each other, and inorganic lubricating powder is embedded with phosphogypsum through the anchoring group of dispersant during the refinement process of dry powder phosphogypsum to form a composite powder with good self-fluidity body, that is, the first layer of coating layer with fluidity and l...
PUM
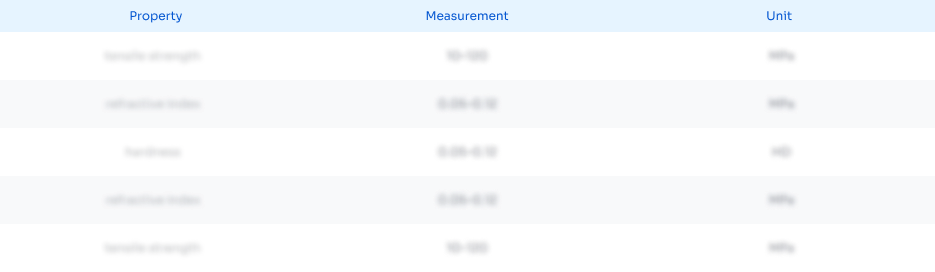
Abstract
Description
Claims
Application Information

- R&D
- Intellectual Property
- Life Sciences
- Materials
- Tech Scout
- Unparalleled Data Quality
- Higher Quality Content
- 60% Fewer Hallucinations
Browse by: Latest US Patents, China's latest patents, Technical Efficacy Thesaurus, Application Domain, Technology Topic, Popular Technical Reports.
© 2025 PatSnap. All rights reserved.Legal|Privacy policy|Modern Slavery Act Transparency Statement|Sitemap|About US| Contact US: help@patsnap.com