A production method for continuous casting of steel slabs containing rare earth elements
A rare earth element and slab continuous casting technology, applied in the field of steel smelting, can solve the problems of poor surface and center quality of the casting slab, unfavorable inclusions floating, difficulty in rare earth alloying, etc., and achieves good surface and center quality of the continuous casting slab. The effect of effectively removing inclusions and stabilizing the yield of rare earth
- Summary
- Abstract
- Description
- Claims
- Application Information
AI Technical Summary
Problems solved by technology
Method used
Image
Examples
Embodiment 1
[0026] The element ratio and some process parameters of the steel in this embodiment are shown in Table 1, Re: 0.15%, C: 0.01%, Si: 1.0%, Cr: 25%, Ni: 9%, N: 0.3%, and the rest The amount is iron and unavoidable impurities. The rare earth is RECe-48 or RECe-45.
[0027] During production, the main operations of the ladle furnace refining process and the continuous casting process are the same as those of the prior art. The total amount of Ca is 0.7kg / t, the weak stirring time for controlling the ladle furnace refining is 30min, the fluctuation area of the steel slag interface is less than 40%, and the rare earth alloy yield is controlled at 30-70%; in the continuous casting process, the middle The superheat of the molten steel in the ladle is controlled at 65°C, the insertion depth of the nozzle of the continuous casting mold is controlled at 135mm, the electromagnetic stirring and dynamic light reduction in the secondary cooling zone are increased, the stirring current is ...
Embodiment 2
[0029] The element ratio and some process parameters of the steel in this embodiment are shown in Table 1, Re: 0.10%, C: 0.10%, Si: 1.5%, Cr: 20%, Ni: 11%, N: 0.26%, and The amount is iron and unavoidable impurities. The rare earth is RECe-48 or RECe-45.
[0030] During production, the main operations of the ladle furnace refining process and the continuous casting process are the same as those of the prior art. The total amount of Ca is 0.45kg / t, the weak stirring time for controlling the ladle furnace refining is 20min, the fluctuation area of the steel slag interface is less than 40%, and the rare earth alloy yield is controlled at 30-70%; in the continuous casting process, the middle The superheat of the molten steel in the ladle is controlled at 60°C, the insertion depth of the nozzle of the continuous casting mold is controlled at 125mm, electromagnetic stirring and dynamic light reduction in the secondary cooling zone are added, the stirring current is controlled at ...
Embodiment 3
[0032] The element ratio and some process parameters of the steel in this embodiment are shown in Table 1, Re: 0.08%, C: 0.08%, Si: 1.7%, Cr: 22%, Ni: 12%, N: 0.20%, and The amount is iron and unavoidable impurities. The rare earth is RECe-48 or RECe-45.
[0033] During production, the main operations of the ladle furnace refining process and the continuous casting process are the same as those of the prior art. The total amount of Ca is 0.35kg / t, the weak stirring time for controlling the ladle furnace refining is 25min, the fluctuation area of the steel slag interface is less than 40%, and the rare earth alloy yield is controlled at 30-70%; in the continuous casting process, the middle The superheat of molten steel in the ladle is controlled at 40°C, the insertion depth of the nozzle of the continuous casting mold is controlled at 115mm, the electromagnetic stirring and dynamic light reduction in the secondary cooling zone are increased, the stirring current is controlled...
PUM
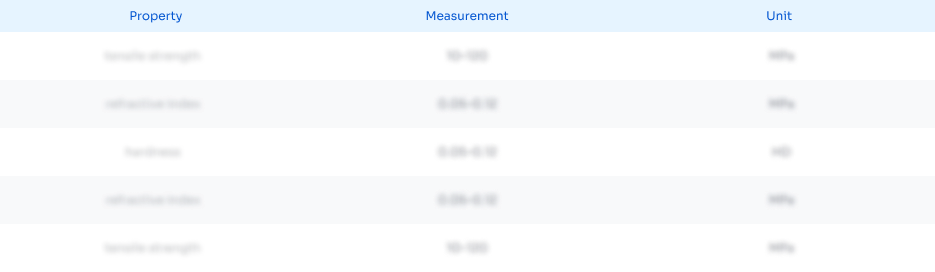
Abstract
Description
Claims
Application Information

- R&D
- Intellectual Property
- Life Sciences
- Materials
- Tech Scout
- Unparalleled Data Quality
- Higher Quality Content
- 60% Fewer Hallucinations
Browse by: Latest US Patents, China's latest patents, Technical Efficacy Thesaurus, Application Domain, Technology Topic, Popular Technical Reports.
© 2025 PatSnap. All rights reserved.Legal|Privacy policy|Modern Slavery Act Transparency Statement|Sitemap|About US| Contact US: help@patsnap.com