Method for improving room-temperature fracture toughness of Nb-Si-based multi-element alloy
A fracture toughness and alloy technology, applied in the field of ultra-high temperature structural materials, can solve problems such as poor fracture toughness, and achieve the effects of high density, improved fracture toughness at room temperature, and bright and clean powder surface.
- Summary
- Abstract
- Description
- Claims
- Application Information
AI Technical Summary
Problems solved by technology
Method used
Image
Examples
Embodiment 1
[0033] Using the combination of plasma rotating electrode atomization technology and spark plasma sintering technology to improve room temperature fracture toughness of Nb-Si based multi-component alloys, the steps are as follows:
[0034] 1. Using Nb, Si, Ti, Cr, Al as synthetic raw materials, using vacuum non-consumable arc melting technology and induction melting casting technology to obtain Nb-22Si-24Ti-2Cr-2Al alloy rods, the size is Φ75mm×150mm, the surface is ground light, dry after washing;
[0035] 2. Fix the Nb-22Si-24Ti-2Cr-2Al alloy rod in the sample loading room of the plasma rotary electrode atomization equipment, and fill the sealing device with high-purity argon (99.99%) for atmosphere protection after vacuumizing;
[0036]3. Set the process parameters such as plasma gun power, plasma arc current and electrode rod speed, so that the end of the high-speed rotating Nb-22Si-24Ti-2Cr-2Al alloy rod is melted, and the melted body is atomized into liquid droplets unde...
Embodiment 2
[0043] Using the plasma rotating electrode atomization method + spark plasma sintering method to improve the room temperature fracture toughness of Nb-Si based multi-component alloys, the steps are as follows:
[0044] 1. Using Nb, Si, Ti, Cr, and Al as synthetic raw materials, the Nb-18Si-24Ti-2Cr-2Al alloy rod is obtained by using vacuum non-consumable arc melting technology and induction melting casting technology, and the sample size is Φ75mm×150mm;
[0045] 2. Fix the Nb-18Si-24Ti-2Cr-2Al alloy sample in the sample loading room of the plasma rotating electrode equipment, and fill the sealing device with high-purity argon (99.99%) for atmosphere protection after vacuumizing;
[0046] 3. Set the process parameters such as plasma gun power, plasma arc current and electrode rod speed, so that the end of the high-speed rotating Nb-18Si-24Ti-2Cr-2Al alloy rod is melted, and the melted body is atomized into liquid droplets under the action of centrifugal force. Shot out, while r...
PUM
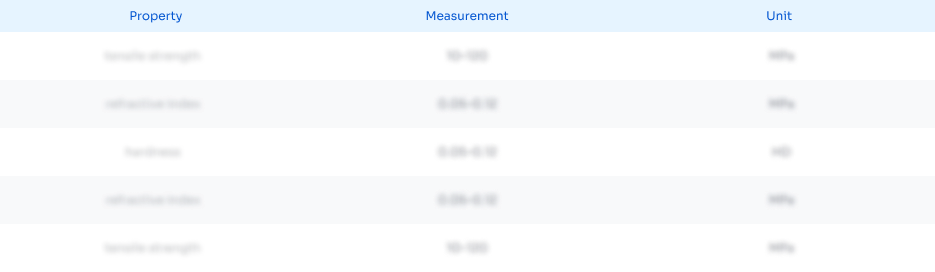
Abstract
Description
Claims
Application Information

- R&D Engineer
- R&D Manager
- IP Professional
- Industry Leading Data Capabilities
- Powerful AI technology
- Patent DNA Extraction
Browse by: Latest US Patents, China's latest patents, Technical Efficacy Thesaurus, Application Domain, Technology Topic, Popular Technical Reports.
© 2024 PatSnap. All rights reserved.Legal|Privacy policy|Modern Slavery Act Transparency Statement|Sitemap|About US| Contact US: help@patsnap.com