Preparation method of scandia-doped dispenser cathode material with turned surface
A cathode and car-making technology is applied in the field of preparation of scandium-containing diffusion surface car-made cathode materials, and can solve the problems of restricting the large-scale application of scandium-containing diffusion cathodes and the like
- Summary
- Abstract
- Description
- Claims
- Application Information
AI Technical Summary
Problems solved by technology
Method used
Image
Examples
Embodiment 1
[0017] Example 1 Dissolve 146.7g of ammonium metatungstate and 16.7g of scandium nitrate in water respectively, stir well and then mix. Powder was prepared by spray drying, and the powder was calcined and decomposed in a muffle furnace at 600°C for 2 hours. The decomposed product is reduced with hydrogen in a tube furnace. The reduction temperature is slowly heated from room temperature to 600°C, kept for 1 hour, continued to be slowly heated to 950°C, kept for 1 hour, and then slowly cooled. After that, pressing, sintering and impregnation are carried out, and the sintering temperature is 1450°C. Afterwards, the cathode is machined, and the cathode is processed into a cylindrical cathode with a diameter of 2mm and a thickness of 2mm (see figure 1 ). Place the prepared cathode in 2% dilute nitric acid aqueous solution for 15 seconds and wash it with deionized water and absolute ethanol. Afterwards, the cathode was placed in a hydrogen atmosphere and heated to 850°C for 20 m...
Embodiment 2
[0018] Example 2 Dissolve 152.9g of ammonium metatungstate and 3.34g of scandium nitrate in water respectively, stir well and then mix. Powder was prepared by spray drying, and the powder was calcined and decomposed in a muffle furnace at 600°C for 2 hours. The decomposed product is reduced with hydrogen in a tube furnace. The reduction temperature is slowly heated from room temperature to 600°C, kept for 1 hour, continued to be slowly heated to 950°C, kept for 1 hour, and then slowly cooled. After that, pressing, sintering and impregnation are carried out, and the sintering temperature is 1450°C. Afterwards, the cathode is machined, and the cathode is processed into a cylindrical cathode with a diameter of 2mm and a thickness of 2mm (see figure 1 ). Place the prepared cathode in 2% dilute nitric acid aqueous solution for 15 seconds and wash it with deionized water and absolute ethanol. Afterwards, the cathode was placed in a hydrogen atmosphere and heated to 850°C for 20 m...
Embodiment 3
[0019] Example 3 Dissolve 139.0g of ammonium metatungstate and 33.5g of scandium nitrate in water respectively, stir well and then mix. Powder was prepared by spray drying, and the powder was calcined and decomposed in a muffle furnace at 600°C for 2 hours. The decomposed product was reduced with hydrogen in a tube furnace. The reduction temperature was slowly heated from room temperature to 600°C, kept for 1 hour, continued to be slowly heated to 950°C, kept for 1 hour, and finally cooled slowly. After that, pressing, sintering and impregnation are carried out, and the sintering temperature is 1450°C. Afterwards, the cathode is machined, and the cathode is processed into a cylindrical cathode with a diameter of 2mm and a thickness of 2mm (see figure 1 ). Place the prepared cathode in 2% dilute nitric acid aqueous solution for 15 seconds and wash it with deionized water and absolute ethanol. Afterwards, the cathode was placed in a hydrogen atmosphere and heated to 850°C for...
PUM
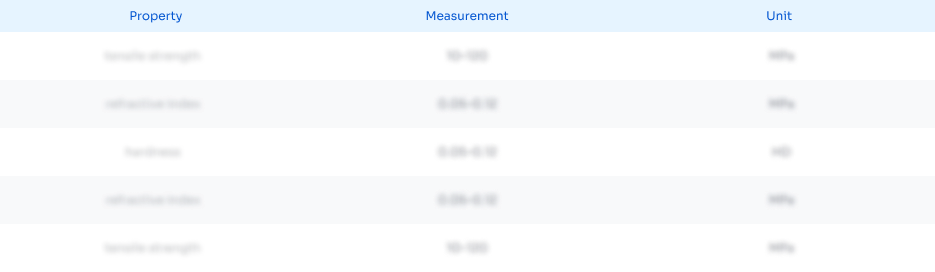
Abstract
Description
Claims
Application Information

- R&D Engineer
- R&D Manager
- IP Professional
- Industry Leading Data Capabilities
- Powerful AI technology
- Patent DNA Extraction
Browse by: Latest US Patents, China's latest patents, Technical Efficacy Thesaurus, Application Domain, Technology Topic, Popular Technical Reports.
© 2024 PatSnap. All rights reserved.Legal|Privacy policy|Modern Slavery Act Transparency Statement|Sitemap|About US| Contact US: help@patsnap.com